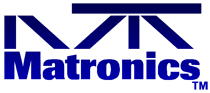 |
Matronics Email Lists Web Forum Interface to the Matronics Email Lists
|
View previous topic :: View next topic |
Author |
Message |
Phil.Perry(at)netapp.com Guest
|
Posted: Tue Sep 29, 2009 8:42 am Post subject: QB Feedback |
|
|
For those of you who have recently received (or will soon be receiving) your QB fuselage’s, here is some feedback I sent to Vans today.
You might want to pack it away some place special and double check these area when yours arrives. Some of it is nit-picky, but I wanted to be as thorough as I could possibly be.
Phil
Hello,
My QB Fuselage (40750) arrived a couple of weeks ago and I thought I’d share some feedback and some inventory discrepancies.
I’ve spent the past couple of weeks walking through the steps and I have currently made it through section 29. Generally speaking, the quality of the work is actually quite nice and the kit was well work the wait. Rivet work looks good and it’s generally deburred quite well.
I have found a few issues with their attention to detail.
These are the most concerning areas of workmanship:
28-4 Step #1) “Radius the corners and remove material from the middle of both control column mounts.” (Remove hatched area).
This step was completely ignored. The control column mounts were deburred and simply bolted into position.
29-6 Step #7) “Draw a line on the flange of the F-10102A and B Baggage Door Seal Angles 3/8” from the lower face of the F-1046-L Mid Fuse Longeron as show in Figure 4. Remove the baggage door seal angles and trim off the portion of the flange below this line. Note that once trimmed, the flange on the F-10102B will be shorter than the flange on F-10102A”
This step was completely ignored. They just riveted the piece into the airplane and left it. Now I’m trying to figure out the best way to trim the part per the plans. I wish they had paid attention and trimmed the part before riveting, or not riveted it at all.
29-9 Step #5) “Check the distance between the aft most rivet hole and the aft end of the F-1013-L and –R Fwd Fuse Longerons per the dimensions in Figure 3. Pull away the F-1070L and –R Mid Side Skins and trim the longerons if necessary (or wait until fwd fuselage longerons are disassembled, but don’t forget).”
This step was ignored and the longerons were just riveted to the skin. They’re not slightly long, but way too long. So long that the left one sticks into the baggage door opening. Now I’m drilling rivets in the skin/longeron and trying to slide a piece of stainless between the two so I can cut them to the proper length before riveting them again. If they wanted to leave them long, they should have never riveted them.
Torque Wrench Use:)
Upon checking the torque value of the AN-3 bolts, it’s quite obvious that they don’t have one on the floor. All of the bolts are over torque by 2X. I’m now backing off all of the nuts to neutral and re-torquing them to 25 inches.
=========================================
Other items of omission…..
25-5 Step #7) The Snap Bushings were not installed – And not included in the kit.
25-6 Step #4) The Snap Bushings were not installed – And not included in the kit.
25-6 Step #5,6,7) The UMHW plastic was not installed – And not included in the kit.
27-6 Step #4) The Snap Bushings were not installed and not included in the kit.
29-19 Step # The 5610-90-31 washers were not included in the kit.
28-6 Step #2) None of the F-1084B’s were shipped with the kit. The A’s are riveted to the floor but they didn’t include the other half (B)’s.
30-4 Step #2) The AN3-20A’s for the steps was not included in the kit. They shipped a 24 with a stack of AN960-10 washers.
Many other sections) They completely ignored dimpling/countersinking and chose to install pan head interior screws as opposed the flush. I cannot speak to the problems this might cause right now – but I’m sure I’ll have a better understand of it as I go forward.
=========================================
Inventory omissions (summarized above):
SB750-10 QTY 8
SB625-8 QTY 2
UHMW-125X1/2X5 QTY 1
Washer 5610-18-31 QTY 2
F-1084B QTY 4
AN3-20A QTY 2
MS21042-3 QTY 2
=========================================
I’m sure I’ll find a few more omissions and areas of concern as I continue through the kit, but these are the ones I have on my list right now. Generally speaking, the kit is great though. I just wanted to provide my findings/feedback upon a closer inspection – since the new factory is now running.
If you have any questions, let me know.
Thanks,
Phil
[quote][b]
| - The Matronics RV10-List Email Forum - | | Use the List Feature Navigator to browse the many List utilities available such as the Email Subscriptions page, Archive Search & Download, 7-Day Browse, Chat, FAQ, Photoshare, and much more:
http://www.matronics.com/Navigator?RV10-List |
|
|
|
Back to top |
|
 |
rbibb
Joined: 16 Jul 2009 Posts: 37
|
Posted: Tue Sep 29, 2009 9:14 am Post subject: QB Feedback |
|
|
It is obvious from reading Phil’s feedback that Van’s subcontractor does not have even a rudimentary QC System in place. It is also obvious that Van’s doesn’t have much of a QC process in place either from an incoming inspection standpoint as some of the items could not be missed with even the most cursory inspection of the items (thinking longeron length).
Excuses can be imagined centered around the ramp up of the new subcontractor location and the emphasis to clear backlog of unhappy customers, neither of which is good enough in my opinion.
In my business (fabricating aerospace parts) this would result in a rejection and me having to remake the item to spec. I realize this is a different world but this level of sloppiness is unacceptable IMO.
Glad I’m building a slow-build.
Don’t get me wrong I love Van’s but this doesn’t live up to the standard I’m used to seeing from them.
Richard Bibb
972-771-2598
972-835-5979 mobile
[quote] [b]
| - The Matronics RV10-List Email Forum - | | Use the List Feature Navigator to browse the many List utilities available such as the Email Subscriptions page, Archive Search & Download, 7-Day Browse, Chat, FAQ, Photoshare, and much more:
http://www.matronics.com/Navigator?RV10-List |
|
|
|
Back to top |
|
 |
jesse(at)saintaviation.co Guest
|
Posted: Tue Sep 29, 2009 10:39 am Post subject: QB Feedback |
|
|
In talking to Van's, they say that they certainly could do better QC, but that would raise the cost of every kit. For them, it's cheaper in the long run to replace or fix mistakes than to spend what it would cost to fix them before they go out the door, thus keeping down the cost of the kit.
do not archive
Jesse Saint
Saint Aviation, Inc.
jesse(at)saintaviation.com (jesse(at)saintaviation.com)
Cell: 352-427-0285
Fax: 815-377-3694
On Sep 29, 2009, at 1:13 PM, Richard Bibb wrote:
Quote: | It is obvious from reading Phil’s feedback that Van’s subcontractor does not have even a rudimentary QC System in place. It is also obvious that Van’s doesn’t have much of a QC process in place either from an incoming inspection standpoint as some of the items could not be missed with even the most cursory inspection of the items (thinking longeron length).
Excuses can be imagined centered around the ramp up of the new subcontractor location and the emphasis to clear backlog of unhappy customers, neither of which is good enough in my opinion.
In my business (fabricating aerospace parts) this would result in a rejection and me having to remake the item to spec. I realize this is a different world but this level of sloppiness is unacceptable IMO.
Glad I’m building a slow-build.
Don’t get me wrong I love Van’s but this doesn’t live up to the standard I’m used to seeing from them.
Richard Bibb
972-771-2598
972-835-5979 mobile
Quote: |
style="color: blue; text-decoration: underline; ">http://www.matronics.com/Navigator?RV10-List
blue; text-decoration: underline; ">http://forums.matronics.com
style="color: blue; text-decoration: underline; ">http://www.matronics.com/contribution
|
|
[quote][b]
| - The Matronics RV10-List Email Forum - | | Use the List Feature Navigator to browse the many List utilities available such as the Email Subscriptions page, Archive Search & Download, 7-Day Browse, Chat, FAQ, Photoshare, and much more:
http://www.matronics.com/Navigator?RV10-List |
|
|
|
Back to top |
|
 |
Phil.Perry(at)netapp.com Guest
|
Posted: Tue Sep 29, 2009 10:41 am Post subject: QB Feedback |
|
|
Attached are two photos of four offenses.
Baggage Seal photo shows:
The longeron extending into the baggage door opening.
The baggage door seal angles (top of baggage door) – not trimmed.
1084 and Control Column mount photo shows:
The 1084B’s missing. The bottom half is riveted to the floor
The control column brackets without the hatched area removed.
From: Richard Bibb [mailto:rbibb(at)tomet.net]
Sent: Tuesday, September 29, 2009 12:14 PM
To: rv10-list(at)matronics.com
Subject: RE: QB Feedback
It is obvious from reading Phil’s feedback that Van’s subcontractor does not have even a rudimentary QC System in place. It is also obvious that Van’s doesn’t have much of a QC process in place either from an incoming inspection standpoint as some of the items could not be missed with even the most cursory inspection of the items (thinking longeron length).
Excuses can be imagined centered around the ramp up of the new subcontractor location and the emphasis to clear backlog of unhappy customers, neither of which is good enough in my opinion.
In my business (fabricating aerospace parts) this would result in a rejection and me having to remake the item to spec. I realize this is a different world but this level of sloppiness is unacceptable IMO.
Glad I’m building a slow-build.
Don’t get me wrong I love Van’s but this doesn’t live up to the standard I’m used to seeing from them.
Richard Bibb
972-771-2598
972-835-5979 mobile
Quote: | http://www.matronics.com/Navigator?RV10-List | 01234567890
| - The Matronics RV10-List Email Forum - | | Use the List Feature Navigator to browse the many List utilities available such as the Email Subscriptions page, Archive Search & Download, 7-Day Browse, Chat, FAQ, Photoshare, and much more:
http://www.matronics.com/Navigator?RV10-List |
|
Description: |
|
Filesize: |
131.83 KB |
Viewed: |
3215 Time(s) |
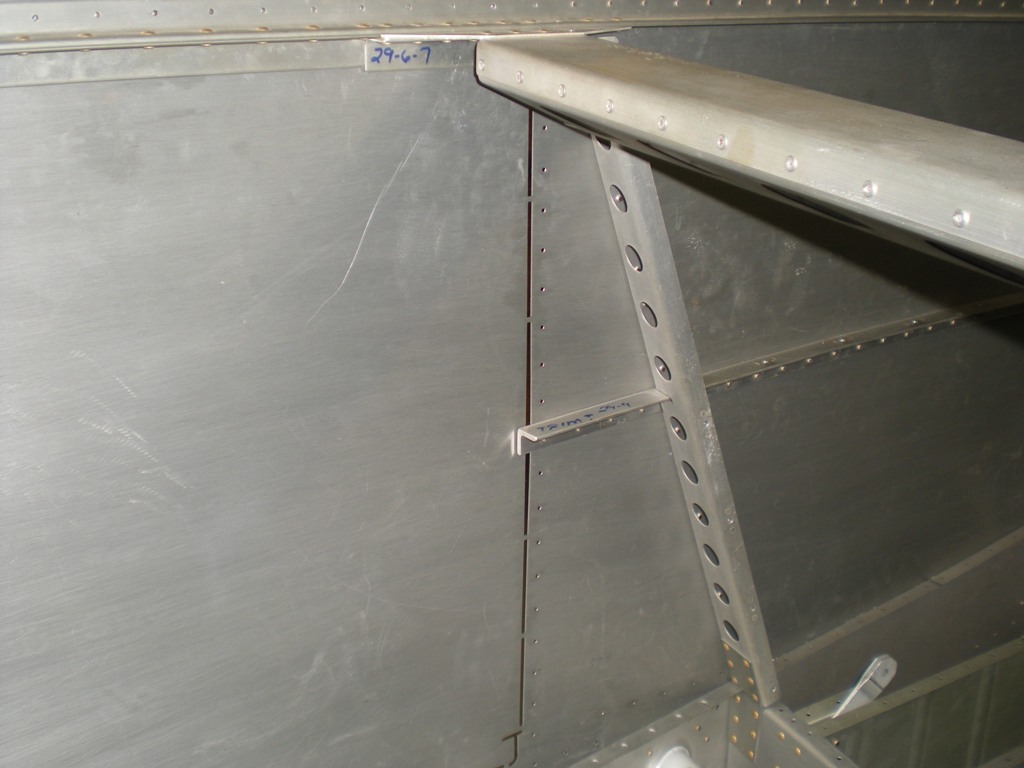
|
Description: |
|
Filesize: |
131.53 KB |
Viewed: |
3215 Time(s) |
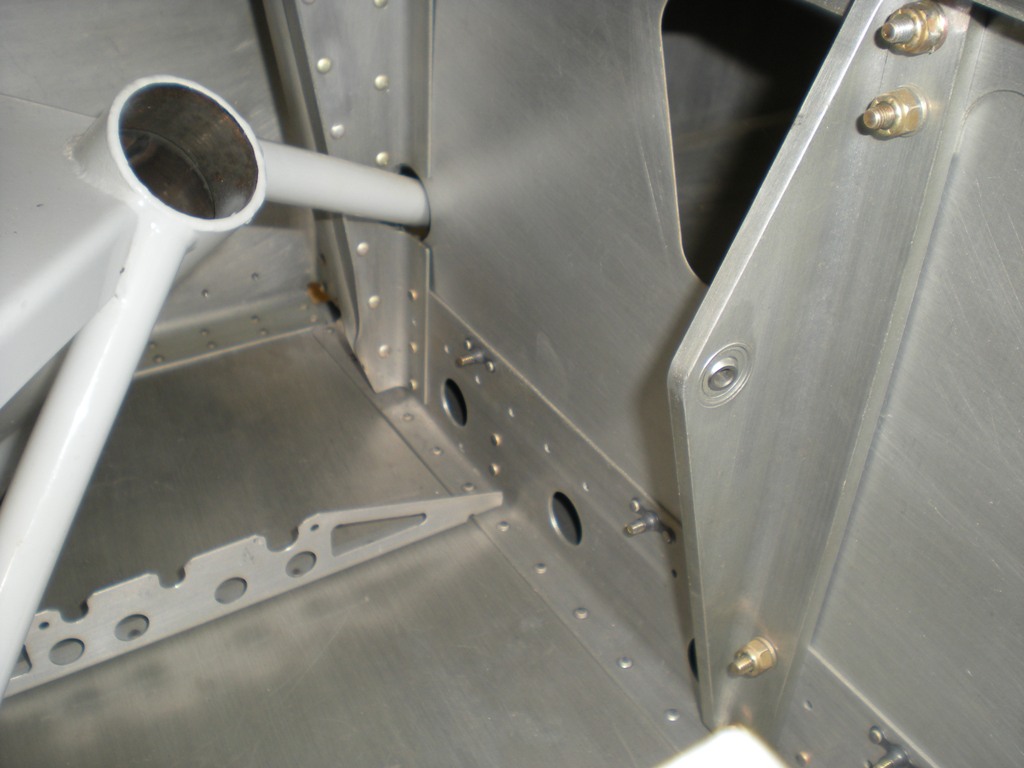
|
|
|
Back to top |
|
 |
rbibb
Joined: 16 Jul 2009 Posts: 37
|
Posted: Tue Sep 29, 2009 11:22 am Post subject: QB Feedback |
|
|
I understand that argument but don’t buy it. It always costs less to do it right the first time. This gets offset, somewhat, by the fact that a lot of their “rework” costs are absorbed by the customer. I was a study once that concluded it basically cost 10X to fix a mistake for every level in a supply chain before the error was detected and corrected.
QC does not, in the long run, cost money but saves it as it prevents having to do things over again. I would think, as the RV-12s ramp up this is going to be a greater problem for them as they need to provide a better documentation trail to deliver conforming kits to their certificate.
The kinds of mistakes Phil has documented just indicate there are no real work standards or requirements placed on the subs. So as long as they get away with it they have no incentive to change.
A good quality system doesn’t prevent mistakes – it prevents making them more than once.
DO NOT ARCHIVE
Richard Bibb
972-771-2598
972-835-5979 mobile
From: owner-rv10-list-server(at)matronics.com [mailto:owner-rv10-list-server(at)matronics.com] On Behalf Of Jesse Saint
Sent: Tuesday, September 29, 2009 1:29 PM
To: rv10-list(at)matronics.com
Subject: Re: QB Feedback
In talking to Van's, they say that they certainly could do better QC, but that would raise the cost of every kit. For them, it's cheaper in the long run to replace or fix mistakes than to spend what it would cost to fix them before they go out the door, thus keeping down the cost of the kit.
do not archive
Jesse Saint
Saint Aviation, Inc.
jesse(at)saintaviation.com (jesse(at)saintaviation.com)
Cell: 352-427-0285
Fax: 815-377-3694
On Sep 29, 2009, at 1:13 PM, Richard Bibb wrote:
It is obvious from reading Phil’s feedback that Van’s subcontractor does not have even a rudimentary QC System in place. It is also obvious that Van’s doesn’t have much of a QC process in place either from an incoming inspection standpoint as some of the items could not be missed with even the most cursory inspection of the items (thinking longeron length).
Excuses can be imagined centered around the ramp up of the new subcontractor location and the emphasis to clear backlog of unhappy customers, neither of which is good enough in my opinion.
In my business (fabricating aerospace parts) this would result in a rejection and me having to remake the item to spec. I realize this is a different world but this level of sloppiness is unacceptable IMO.
Glad I’m building a slow-build.
Don’t get me wrong I love Van’s but this doesn’t live up to the standard I’m used to seeing from them.
Richard Bibb
972-771-2598
972-835-5979 mobile
Quote: | style="color: blue; text-decoration: underline; ">http://www.matronics.com/Navigator?RV10-Listblue; text-decoration: underline; ">http://forums.matronics.comstyle="color: blue; text-decoration: underline; ">http://www.matronics.com/contribution |
[quote]
href="http://www.matronics.com/Navigator?RV10-List">http://www.matronics.com/Navigator?RV10-List
href="http://forums.matronics.com">http://forums.matronics.com
href="http://www.matronics.com/contribution">http://www.matronics.com/c
[b]
| - The Matronics RV10-List Email Forum - | | Use the List Feature Navigator to browse the many List utilities available such as the Email Subscriptions page, Archive Search & Download, 7-Day Browse, Chat, FAQ, Photoshare, and much more:
http://www.matronics.com/Navigator?RV10-List |
|
|
|
Back to top |
|
 |
Phil.Perry(at)netapp.com Guest
|
Posted: Wed Sep 30, 2009 8:55 am Post subject: QB Feedback |
|
|
Thought I’d share Scott’s response.
It was well received. I have a couple of more build misses that I’ll forgot to include and I will be adding them to the list and resending to the group.
Phil
Phil, Really appreciate the input! We'll get the missing inventory out to you asap and I'll forward the info you've provided to our QC guys and to the assembly crew in the Philippines.
If you need help with specific 'fix' options for any of the items you listed, please let us know.
Thanks again, Scott at Van's
From: Perry, Phil
Sent: Tuesday, September 29, 2009 1:39 PM
To: rv10-list(at)matronics.com
Subject: RE: QB Feedback
Attached are two photos of four offenses.
Baggage Seal photo shows:
The longeron extending into the baggage door opening.
The baggage door seal angles (top of baggage door) – not trimmed.
1084 and Control Column mount photo shows:
The 1084B’s missing. The bottom half is riveted to the floor
The control column brackets without the hatched area removed.
From: Richard Bibb [mailto:rbibb(at)tomet.net]
Sent: Tuesday, September 29, 2009 12:14 PM
To: rv10-list(at)matronics.com
Subject: RE: QB Feedback
It is obvious from reading Phil’s feedback that Van’s subcontractor does not have even a rudimentary QC System in place. It is also obvious that Van’s doesn’t have much of a QC process in place either from an incoming inspection standpoint as some of the items could not be missed with even the most cursory inspection of the items (thinking longeron length).
Excuses can be imagined centered around the ramp up of the new subcontractor location and the emphasis to clear backlog of unhappy customers, neither of which is good enough in my opinion.
In my business (fabricating aerospace parts) this would result in a rejection and me having to remake the item to spec. I realize this is a different world but this level of sloppiness is unacceptable IMO.
Glad I’m building a slow-build.
Don’t get me wrong I love Van’s but this doesn’t live up to the standard I’m used to seeing from them.
Richard Bibb
972-771-2598
972-835-5979 mobile
Quote: | http://www.matronics.com/Navigator?RV10-List http://forums.matronics.com http://www.matronics.com/contribution | 0
[quote][b]
| - The Matronics RV10-List Email Forum - | | Use the List Feature Navigator to browse the many List utilities available such as the Email Subscriptions page, Archive Search & Download, 7-Day Browse, Chat, FAQ, Photoshare, and much more:
http://www.matronics.com/Navigator?RV10-List |
|
|
|
Back to top |
|
 |
|
|
You cannot post new topics in this forum You cannot reply to topics in this forum You cannot edit your posts in this forum You cannot delete your posts in this forum You cannot vote in polls in this forum You cannot attach files in this forum You can download files in this forum
|
Powered by phpBB © 2001, 2005 phpBB Group
|