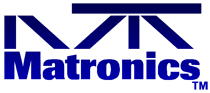 |
Matronics Email Lists Web Forum Interface to the Matronics Email Lists
|
View previous topic :: View next topic |
Author |
Message |
MauleDriver(at)nc.rr.com Guest
|
Posted: Mon Dec 14, 2009 6:59 pm Post subject: Weld-On case study #605 |
|
|
I just finished doing my 2 right side windows using Weld-On. It went
well and I feel confident finishing up with it. Thought I'd share the
experience.
Going into it, I bought the Weld-On before thoroughly researching
peoples' experiences documented here on the list. In the end, I decided
that I wouldn't go the epoxy resin and flock route because I sensed this
would be the least strong solution. I didn't take Dave Saylor's
approach to an easily replaceable window because it was the most
demanding in terms of craftsmanship. In any case, I intended to
overlay the joint with cloth and resin for a good finish. I would have
probably tried one of the other adhesives discussed here by others but I
had already made the investment in Weld-On from Vans. So I went with
the factory solution.
Weld-on has a strong chemical/plastic kind of smell and it can linger.
Might not be the best thing to use in an attached garage. Even though
it was cold out, I ran an exhaust fan and let some air thru so the
smell didn't build up. I wore a simple paper mask the first time but
used a mask with fresh filter cannisters the second and felt better
about it. Closing up the containers and otherwise disposing of all
droppings helps.
I used the aluminum fingers and cleco clamping method exclusively. I
removed the fingers about 90 minutes after setting them. Works well so
far.
Weld-on sets up fast but not too fast. My shop was probably in the low
70s and dropping. When I added the catalyst, I didn't try to get every
last drop. Mixed for 3 minutes and started applying it using an acid
brush.
Is Weld-on is too thin and runny? It's ok, at least at 70F degrees.
Not that hard to handle.
Per some advice here on the list, I put a thick lumpy bead near the
outside edge of the cutout. That is, in the crotch of the "L". On the
first window I didn't apply any directly to the window. On the second,
I put a thin layer on the window with the same bead on the fuselage. As
someone said, it easier to clean up the excess than to fill up any
gaps. That worked well. I was really rushed trying to make sure I
didn't run out of working time but there was no need. It seems to skin
over pretty quickly but actually a certain amount of drying seems to
form a skin on small portions of adhesive. But if you go back to the
mixing cup, you won't find a skin and there's no change in consistency
after say 15 or 20 minutes. So you actually have lots of working time.
When it does set, it does heat up in the cup so be careful about
disposing in the trash before set up.
Weld-on forms messy little strings if you try to work with it quickly.
The solution here is to slow down and don't form strings. There's
plenty of time. And it cleans up easily even after it starts to set up.
Regarding surface prep and clean-up; I used acetone as the last step in
surface prep with the thought that "it does matter how much you use".
For clean-up I used a 50:50 mix of acetone and mineral spirits. This
works pretty well even an hour or two after starting.
I found that brush on protective film from Spruce useful. I tried
keeping the plastic from the factory on the Plexiglas but found that
replacing it with the brush on stuff gave me a clearer view of things.
So once I trimmed the plexi down to it's final size, I removed the outer
plastic and brushed on the blue stuff from Spruce. Then I removed the
plastic from the inner surface and used plastic tape to mask the glue
line. I used paper to mask of the inner surface to protect from the
Weld-on. After gluing and clamping the plexi in place, I cleaned up
the squeezed out Weld-on with the 50:50 mix, Then removed the tape and
paper on the inner surface. This left a pretty clean line but a small
spatula helped cleanup up some squeeze-out and the 50:50 mix cleaned up
the rest. I'll probably coat the inner surface with the brush on film
to protect from scratches during interior work.
There seems to be several workable approaches to gluing in the windows.
The factory approach with Weld-on seems to work well when combined with
the intelligence on this list.
Thanks to those who wrote up their experiences before.
Bill "window 3 is teed up for tomorrow" Watson
40605
| - The Matronics RV10-List Email Forum - | | Use the List Feature Navigator to browse the many List utilities available such as the Email Subscriptions page, Archive Search & Download, 7-Day Browse, Chat, FAQ, Photoshare, and much more:
http://www.matronics.com/Navigator?RV10-List |
|
|
|
Back to top |
|
 |
Strasnuts
Joined: 10 Feb 2009 Posts: 502 Location: Salt Lake City, UT
|
Posted: Mon Dec 14, 2009 7:44 pm Post subject: Weld-On case study #605 |
|
|
Thanks for the helpful write-up. I will be using Weld-On as well and it's
coming up soon on my build.
---
| - The Matronics RV10-List Email Forum - | | Use the List Feature Navigator to browse the many List utilities available such as the Email Subscriptions page, Archive Search & Download, 7-Day Browse, Chat, FAQ, Photoshare, and much more:
http://www.matronics.com/Navigator?RV10-List |
|
_________________ 40936
RV-10 SB N801VR Flying
780 Hours
SuperSTOL 60 hours |
|
Back to top |
|
 |
nukeflyboy
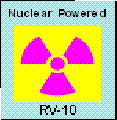
Joined: 05 Jan 2008 Posts: 162 Location: Granbury, TX
|
Posted: Mon Dec 14, 2009 7:52 pm Post subject: Re: Weld-On case study #605 |
|
|
Bill,
My experience was very similar to yours. I had no difficulty with the Weld-on except I was too stingy with my first window. Put it on thick is the best advice. It comes off easy enough with a little attention. The trick is to not wait too long to start the cleanup but not start it too early. I also used the aluminum clips to hold it in place.
The only caution is to be careful with acetone near the plexi. All ketones are damaging and can cause crazing or clouding of the plexi. As long as you only use it where you plan to cover it with a layer of glass you should be ok.
Having had a fiberglass strip epoxied to an RV-6 canopy depart in flight (two separate occasions) I don't trust epoxy to bond to plexiglass.
| - The Matronics RV10-List Email Forum - | | Use the List Feature Navigator to browse the many List utilities available such as the Email Subscriptions page, Archive Search & Download, 7-Day Browse, Chat, FAQ, Photoshare, and much more:
http://www.matronics.com/Navigator?RV10-List |
|
_________________ Dave Moore
RV-6 built and sold
RV-10 built and flying |
|
Back to top |
|
 |
daveleikam(at)wi.rr.com Guest
|
Posted: Mon Dec 14, 2009 8:41 pm Post subject: Weld-On case study #605 |
|
|
I found putting the mixed Weldon in a triangular squeeze bag with about a
1/4 inch cut opening works really well to apply a nice bead. And yes, you
have to work steady, but there is plenty of time to do a good job.
Dave Leikam
---
| - The Matronics RV10-List Email Forum - | | Use the List Feature Navigator to browse the many List utilities available such as the Email Subscriptions page, Archive Search & Download, 7-Day Browse, Chat, FAQ, Photoshare, and much more:
http://www.matronics.com/Navigator?RV10-List |
|
|
|
Back to top |
|
 |
johngoodman

Joined: 18 Sep 2006 Posts: 530 Location: GA
|
Posted: Tue Dec 15, 2009 6:34 am Post subject: Re: Weld-On case study #605 |
|
|
Read the can carefully. If you can smell it, you're doing it wrong.
John
| - The Matronics RV10-List Email Forum - | | Use the List Feature Navigator to browse the many List utilities available such as the Email Subscriptions page, Archive Search & Download, 7-Day Browse, Chat, FAQ, Photoshare, and much more:
http://www.matronics.com/Navigator?RV10-List |
|
_________________ #40572 Phase One complete in 2011 |
|
Back to top |
|
 |
Mike Whisky

Joined: 05 Jun 2006 Posts: 336 Location: Switzerland
|
Posted: Wed Dec 16, 2009 11:18 am Post subject: Re: Weld-On case study #605 |
|
|
Did I understand this correctly that you use weld-on for the windscreen only for the plexiglass-composit (cabintop) connection, right?!
The fuselagetop -windscreen connection is achieved by epoxy/flox and glass strips.
Thanks
Michael
| - The Matronics RV10-List Email Forum - | | Use the List Feature Navigator to browse the many List utilities available such as the Email Subscriptions page, Archive Search & Download, 7-Day Browse, Chat, FAQ, Photoshare, and much more:
http://www.matronics.com/Navigator?RV10-List |
|
_________________ RV-10 builder (flying)
#511 |
|
Back to top |
|
 |
MauleDriver(at)nc.rr.com Guest
|
Posted: Wed Dec 16, 2009 2:19 pm Post subject: Weld-On case study #605 |
|
|
Yes. I haven't done the windsheild yet but that is my understanding.
Weld-on wouldn't do much with the aluminum I wouldn't think.
Michael Wellenzohn wrote:
Quote: |
Did I understand this correctly that you use weld-on for the windscreen only for the plexiglass-composit (cabintop) connection, right?!
The fuselagetop -windscreen connection is achieved by epoxy/flox and glass strips.
Thanks
Michael
--------
RV-10 builder (avionics, wiring)
#511
Read this topic online here:
http://forums.matronics.com/viewtopic.php?p 77760#277760
|
| - The Matronics RV10-List Email Forum - | | Use the List Feature Navigator to browse the many List utilities available such as the Email Subscriptions page, Archive Search & Download, 7-Day Browse, Chat, FAQ, Photoshare, and much more:
http://www.matronics.com/Navigator?RV10-List |
|
|
|
Back to top |
|
 |
|
|
You cannot post new topics in this forum You cannot reply to topics in this forum You cannot edit your posts in this forum You cannot delete your posts in this forum You cannot vote in polls in this forum You cannot attach files in this forum You can download files in this forum
|
Powered by phpBB © 2001, 2005 phpBB Group
|