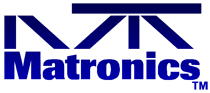 |
Matronics Email Lists Web Forum Interface to the Matronics Email Lists
|
View previous topic :: View next topic |
Author |
Message |
nuckolls.bob(at)aeroelect Guest
|
Posted: Fri Feb 19, 2010 8:57 pm Post subject: B&C Regulators and water-falls |
|
|
Received at AeroElectric Connection today . . .
Bill Harrelson and I had a chance to review the investigation and preliminary causes of an in-flight fire in a Lancair IV-P that occurred last spring (2009). The findings and conclusions are not yet established, but the investigator felt that some of the information discovered was not in question, and would be useful to the experimental community. We agreed to help spread the word�as follows:
The accident aircraft experienced an in-flight battery fire of the secondary electrical system shortly after takeoff. The pilot was able to return to the airport and extinguish the fire in the tail section of the aircraft after landing. The battery, case, and nearby components were consumed/destroyed, and the aircraft fuselage sustained significant heat damage from the aft pressure bulkhead to the elevators/rudder. The cause of the fire has not been absolutely determined, but the lead/acid battery vents had apparently been obstructed, resulting in a case rupture and venting of hydrogen gas into the tail section of the airplane. The exact cause of this apparent over pressurization and rupture awaits additional information and analysis. This finding and the final NTSB report are expected within a month and we will disseminate this report through the LML and LOBO newsletter.
One initial result of the investigation was that the B&C regulator for the secondary electrical system was inoperative upon post-flight analysis. The NTSB investigator conducted a detailed examination and analysis of the defective unit and determined that the electrical design was robust and appropriate to the task. The unit was mounted to the engine side of the firewall with the spade terminal connectors projecting to the side of the aircraft. This unit is not sealed, and at some point liquid (probably water) entered the metal box, most likely through the opening around the spade terminals,
Hmmm . . . They speak of "spade" terminals . . . I presume they're
referring to the screw-terminal strip.
and filled it to a depth of 1/4 to 1/2 inch. The liquid allowed arcing among internal components and to the case ground, leaving carbon tracks on the circuit board and case, and destroying the electrical functionality.
It is certain that water and electronics don't
mix well. I'm not certain that mounting on the firewall
is an automatic no-no . . . we've been tying stuff
to firewalls since day-one but it IS a unique environment.
Shucks, look at all the firewall mounted electro-whizzies
on this airplane . . .
http://aeroelectric.com/Pictures/Wiring_Technique/Firewall_Ckt_Protection.jpg
Way back when, Cessna modified the cowl attach fittings
to set on shock mounts instead of the firewall bulkhead.
It reduced cabin noise significantly. However, the gap
around the aft edge of the "floating cowl" allowed water
to run down the windshield of parked aircraft right down the
firewall. Believe it or not, there was a period of
time when Cessna was adding brushed on EPOXY seals to
the S701 style battery and starter contactors!
Seems that on a nice hot day, the contactor would exhale.
Then a nice cool shower came along and bathed the contactor
which inhaled liquid water thought the non-hermetic
cap seals. Now the water could only get out as a vapor
through repeated atmospheric transfers of gas from the
semi-tight enclosure.
Needless to day, even epoxy sealing was only marginally
successful in forestalling premature contactor death
due to rust. Those were the years I did my first alternator
regulator design for Cessna that featured an injection
molded case with o-ring sealed lid. It was a couple bux
more expensive than somebody else's design that was
manually doped with sealant at the enclosure gaps. A
risky, process sensitive design . . . but they liked
it.
A review of installation instructions provided with B&C regulators recommends they be installed inside the cockpit or in a similar environmentally-protected area. This regulator was mounted inside the engine compartment, as we believe are the vast majority of Lancair installations. When so installed, regulators are subject to additional heat and cooling stresses, as well as water/solvents from engine cleaning and other maintenance when the cowling is removed. If mounted in any position other than with the spades down, liquid can enter in the area of the spade terminals and will then be trapped within the lower part of the enclosure, immersing part of the main circuit board.
Right . . . so mount the terminal strips down and be cognizant
of the fact that you can't just spray everything down when
cleaning the engine. B&C suffered some bearing failures in
alternators way back when due to over-zealous use of high-
pressure, soapy-water.
If you are still building and have the option, review the B&C recommendations on mounting location and consider locating your B&C regulator(s) inside the cockpit; preferably with the spades down if there is any possibility of liquid exposure. No matter the location, mount them in such a way that they cannot ingest and retain water.
Excellent suggestion which applies to ALL accessories
not suitably protected from either nature or owner-generated
moisture issues. Shucks, we had many killobux of warranty
hassles on the C337 that featured a really nice radio
access hatch in the cowl deck forward of the windshield
but aft of the firewall. Seems the hatch seals liked to leak
a drip into the radios.
If you are not able to locate the regulator(s) as recommended by B&C, consider shielding the terminal strip area from liquids. We expect to contact B&C about the feasibility of other improvements that could be made, but will refrain from making any recommendations until we receive their comments.
All good suggestions and plans for action . . . but I'll
suggest overly simplistic. These are increasingly
complex machines with features that do not fare well
when subjected to soapy water, snow, ice, rain-water,
ozone, hydraulic fluids, spilled 7-up, etc. etc.
By the way, when the B&C "regulators" were originally
conceived, we considered offering the regulator, LV-protection
and LV-warn as a trio of separate components. But it
was our design goal that EVERY user of B&C regulators
received the benefit of OV-protection and active notification
of low voltage. Hence the rather expensive "regulator" which
was really an "alternator control system".
The failure in the Lancair points out a weakness of
that design philosophy. Filling the box with water poses
a risk of killing both OV protection --AND-- regulator
functionality. I.e., SINGLE POINT OF FAILURE that produces
an uncontrolled runaway. Given what we know now, would
we have done it any different back then? Hard to tell.
We can learn from this failure instance and be cognizant
of as many risks as one can deduce individually and
collectively. This is what FMEA is all about. The
process benefits greatly from lessons learned . . . whether
on last months's battery fire or the last century�s leaky
cowls.
Bob . . .
[quote][b]
| - The Matronics AeroElectric-List Email Forum - | | Use the List Feature Navigator to browse the many List utilities available such as the Email Subscriptions page, Archive Search & Download, 7-Day Browse, Chat, FAQ, Photoshare, and much more:
http://www.matronics.com/Navigator?AeroElectric-List |
|
|
|
Back to top |
|
 |
ronburnett(at)charter.net Guest
|
Posted: Sat Feb 20, 2010 5:13 am Post subject: B&C Regulators and water-falls |
|
|
My firewall mounted tray supplied for my electric dependent engine contains two Oddessey 680 batts., but I drilled lightening holes in it which should also preclude water/glycol retension.
Ron Burnett RV-6A forever finishing
Subaru H4--
---- "Robert L. Nuckolls wrote:
=============
Received at AeroElectric Connection today . . .
Bill Harrelson and I had a chance to review the
investigation and preliminary causes of an
in-flight fire in a Lancair IV-P that occurred
last spring (2009). The findings and conclusions
are not yet established, but the investigator
felt that some of the information discovered was
not in question, and would be useful to the
experimental community. We agreed to help spread the word
as follows:
The accident aircraft experienced an in-flight
battery fire of the secondary electrical system
shortly after takeoff. The pilot was able to
return to the airport and extinguish the fire in
the tail section of the aircraft after landing.
The battery, case, and nearby components were
consumed/destroyed, and the aircraft fuselage
sustained significant heat damage from the aft
pressure bulkhead to the elevators/rudder. The
cause of the fire has not been absolutely
determined, but the lead/acid battery vents had
apparently been obstructed, resulting in a case
rupture and venting of hydrogen gas into the tail
section of the airplane. The exact cause of this
apparent over pressurization and rupture awaits
additional information and analysis. This finding
and the final NTSB report are expected within a
month and we will disseminate this report through the LML and LOBO newsletter.
One initial result of the investigation was that
the B&C regulator for the secondary electrical
system was inoperative upon post-flight analysis.
The NTSB investigator conducted a detailed
examination and analysis of the defective unit
and determined that the electrical design was
robust and appropriate to the task. The unit was
mounted to the engine side of the firewall with
the spade terminal connectors projecting to the
side of the aircraft. This unit is not sealed,
and at some point liquid (probably water) entered
the metal box, most likely through the opening around the spade terminals,
Hmmm . . . They speak of "spade" terminals . . . I presume they're
referring to the screw-terminal strip.
and filled it to a depth of 1/4 to 1/2 inch. The
liquid allowed arcing among internal components
and to the case ground, leaving carbon tracks on
the circuit board and case, and destroying the electrical functionality.
It is certain that water and electronics don't
mix well. I'm not certain that mounting on the firewall
is an automatic no-no . . . we've been tying stuff
to firewalls since day-one but it IS a unique environment.
| - The Matronics AeroElectric-List Email Forum - | | Use the List Feature Navigator to browse the many List utilities available such as the Email Subscriptions page, Archive Search & Download, 7-Day Browse, Chat, FAQ, Photoshare, and much more:
http://www.matronics.com/Navigator?AeroElectric-List |
|
|
|
Back to top |
|
 |
|
|
You cannot post new topics in this forum You cannot reply to topics in this forum You cannot edit your posts in this forum You cannot delete your posts in this forum You cannot vote in polls in this forum You cannot attach files in this forum You can download files in this forum
|
Powered by phpBB © 2001, 2005 phpBB Group
|