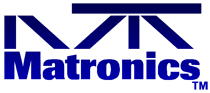 |
Matronics Email Lists Web Forum Interface to the Matronics Email Lists
|
View previous topic :: View next topic |
Author |
Message |
rparigoris
Joined: 24 Nov 2009 Posts: 804
|
Posted: Wed Mar 31, 2010 6:40 pm Post subject: Timing question for brushed motor |
|
|
I have a long can speed 400 electric motor with a folding propellor that is being used to aid cooling in the radiator duct of my 914 Rotax powered Europa. Maximum about 70 watts in forward direction and 35 watts in reverse (to hinder cooling). It is a brushed motor controlled by a pulse width modulated speed controller.It will most likely see forward direction 75% of the time when used. Think I could get away with 5 degree advance (forward) and not kill brushes and armature too quickly when running in reverse (5 degrees retarded)?Thx.Ron Parigoris [quote][b]
| - The Matronics AeroElectric-List Email Forum - | | Use the List Feature Navigator to browse the many List utilities available such as the Email Subscriptions page, Archive Search & Download, 7-Day Browse, Chat, FAQ, Photoshare, and much more:
http://www.matronics.com/Navigator?AeroElectric-List |
|
|
|
Back to top |
|
 |
nuckolls.bob(at)aeroelect Guest
|
Posted: Wed Mar 31, 2010 7:08 pm Post subject: Timing question for brushed motor |
|
|
At 09:36 PM 3/31/2010, you wrote:
Quote: | I have a long can speed 400 electric motor with a folding propellor
that is being used to aid cooling in the radiator duct of my 914
Rotax powered Europa. Maximum about 70 watts in forward direction
and 35 watts in reverse (to hinder cooling). It is a brushed motor
controlled by a pulse width modulated speed controller.
It will most likely see forward direction 75% of the time when used.
Think I could get away with 5 degree advance (forward) and not kill
brushes and armature too quickly when running in reverse (5 degrees retarded)?
|
Are you certain that the brush clocking has been
optimized for one direction over another? As I recall
my days at Electro-Mech, I don't think that brush
clocking was much of an issue for motors below a half
h.p. or so . . . I think brush life in small motors
has more to do with simple wear out-as opposed to
electrical efficiency. This is because they tend to
run small motors very fast to improve on h.p. to
weight ratio.
Bob . . .
| - The Matronics AeroElectric-List Email Forum - | | Use the List Feature Navigator to browse the many List utilities available such as the Email Subscriptions page, Archive Search & Download, 7-Day Browse, Chat, FAQ, Photoshare, and much more:
http://www.matronics.com/Navigator?AeroElectric-List |
|
|
|
Back to top |
|
 |
rparigoris
Joined: 24 Nov 2009 Posts: 804
|
Posted: Wed Mar 31, 2010 10:09 pm Post subject: Timing question for brushed motor |
|
|
Hi BobThx. for the reply."Are you certain that the brush clocking has been optimized for one direction over another?"Timing on a brushed motor is every bit as important as timing on a internal combustion engine. A small displacement high performance 2 stroke, even though it has a small displacement is making a lot of HP for its size and timing is critical. Same goes for small high RPM electric motors. There is an ideal timing setting depending on what you are looking for. Best efficency will net less heat build up and longer life with less arcing, but does not make best amount of power. Often with electric models motors are pushed to get best power to weight. A neutral timed motor, meaning that current draw unloaded with not so much voltage as to over speed is the same forward as reverse direction will yield a motor that works equally bad in both directions. That said it works OK but makes not best HP at high RPM. Advancing does good things for RPM and HP with just a tad more current draw. Now for retarded timing, it is bad all around. It draws more current, arcs and spits and does not make much HP or RPMs. I never fooled with measuring or failing motors at reduced power settings and only 5 degrees retarded. A motor like this I may push in a model well over 125 watts for short times, and advancing will bring out more power. depending on motor, prop and duration and voltage and I may go as high as 15 plus degrees advanced. I do want a pitch speed of 80MPH plus so in a climb can keep things cooler and that has the motor cranking some RPMs. Keeping watts to 75 max and probably only using that sparingly with lesser throttle most of the time, I am hoping for a reasonable motor life, this would be with motor going in the forward direction. After soaring and starting motor in air, or starting a cold motor, by reversing direction of motor it will constipate air in radiator duct and quicken warm up. In addition I think reverse can be used in flight to decrease some cooling drag and keep temps where I want them, kinda like a cowl flap. I was hoping someone had a better feel than I for running a motor with 5 degrees retarded timing for long periods.Ron Parigoris [quote][b]
| - The Matronics AeroElectric-List Email Forum - | | Use the List Feature Navigator to browse the many List utilities available such as the Email Subscriptions page, Archive Search & Download, 7-Day Browse, Chat, FAQ, Photoshare, and much more:
http://www.matronics.com/Navigator?AeroElectric-List |
|
|
|
Back to top |
|
 |
nuckolls.bob(at)aeroelect Guest
|
Posted: Thu Apr 01, 2010 5:22 am Post subject: Timing question for brushed motor |
|
|
At 01:06 AM 4/1/2010, you wrote:
Quote: | Hi Bob
Thx. for the reply.
"Are you certain that the brush clocking has been optimized for one
direction over another?"
Timing on a brushed motor is every bit as important as timing on a
internal combustion engine. A small displacement high performance 2
stroke, even though it has a small displacement is making a lot of
HP for its size and timing is critical.
|
But was your motor received from the factory
optimized for one direction? And if so, at what
load? When we build PM motors as catalog items,
it is assumed that an end user may run it either
direction. Hence the brush clocking is centered
on the net field for zero-torque.
Quote: | Same goes for small high RPM electric motors. There is an ideal
timing setting depending on what you are looking for. Best
efficency will net less heat build up and longer life with less
arcing, but does not make best amount of power. Often with electric
models motors are pushed to get best power to weight. A neutral
timed motor, meaning that current draw unloaded with not so much
voltage as to over speed is the same forward as reverse direction
will yield a motor that works equally bad in both directions.
|
The reason for seeking an optimized brush
position is because the magnetic flux generated
in armature reacts with the fixed field flux
and distorts or "twists" the net field for
ideal commutation. This distortion is a function
of ampere-turns of flux generating power
at the operating point of interest. Change
the torque setting and the optimum point shifts.
This is why large motors have compensating
field windings in series with the brushes
that tend to stabilize the rotation of net
flux as the armature current increases.
But since compensating windings are physically
offset in fixed rotation from the main
field windings, compensation can be accomplished
only for one direction. Our 3 hp air conditioner
motors were fitted with compensation windings
as were our 10 hp hydraulic pump motors.
Quote: | That said it works OK but makes not best HP at high RPM. Advancing
does good things for RPM and HP with just a tad more current draw.
Now for retarded timing, it is bad all around. It draws more
current, arcs and spits and does not make much HP or RPMs. I never
fooled with measuring or failing motors at reduced power settings
and only 5 degrees retarded. A motor like this I may push in a
model well over 125 watts for short times, and advancing will
bring out more power. depending on motor, prop and duration and
voltage and I may go as high as 15 plus degrees advanced.
|
I'm not sure the motors you've been working with
were optimized so much for efficiency as for
hp/weight ratio. There's a bucket full of trade-offs
when designing motors. When optimizing costs
and gross performance in small motors for models
I suspect other features like commutation
efficiency suffers . . .
To determine if your cooling fan application
would benefit from fine tuning of brush position
would take some bench study on a dynamometer
and precision instrumentation.
You would want to get torque and rpm targets
for the two modes of operation . . . but since
you're PWM controlling for speed, you may
have operating points scattered all over the
place.
The short answer to you original question
is, "Yes, there are things you can do to research
and perhaps optimize performance of the motor
at some point in constellation of operating
points. But without the benefit of dynamic
compensation, you'll have to select the one
place where all is "right with the world"
and let the rest of the conditions fall where
they may.
This could very well turn into a pretty detailed
science project. What's the design goal and what's
the expected benefit for achieving it. And how do
you gage the return on investment for doing the
science?
Bob . . .
| - The Matronics AeroElectric-List Email Forum - | | Use the List Feature Navigator to browse the many List utilities available such as the Email Subscriptions page, Archive Search & Download, 7-Day Browse, Chat, FAQ, Photoshare, and much more:
http://www.matronics.com/Navigator?AeroElectric-List |
|
|
|
Back to top |
|
 |
|
|
You cannot post new topics in this forum You cannot reply to topics in this forum You cannot edit your posts in this forum You cannot delete your posts in this forum You cannot vote in polls in this forum You cannot attach files in this forum You can download files in this forum
|
Powered by phpBB © 2001, 2005 phpBB Group
|