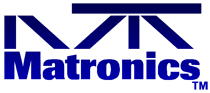 |
Matronics Email Lists Web Forum Interface to the Matronics Email Lists
|
View previous topic :: View next topic |
Author |
Message |
teamgrumman(at)YAHOO.COM Guest
|
Posted: Wed Jun 23, 2010 12:07 pm Post subject: Interior plastic |
|
|
I'm installing windows and new plastic in a Cheetah. New headliner in the cabin and canopy too.
The new stuff is semi-trimmed to fit as it comes. That saves a lot of time. I've mentioned to Garner before about the poor fitting of the plastic. I know it isn't his fault. I would have thought by now, with planes as recent as 2005, that the tooling would have been corrected. The added time to install stuff that doesn't fit surely must add to the time it takes to build the plane.
Canopy plastic:
Garner, get both pieces and lay them side-by-side. Compare the back of each piece to each other. You'll notice the shape of the right piece, at the aft edge, is molded quite differently from the left. The left is correct. The right side is also about 1/4 inch too short. It's impossible to rivet it to the trailing edge as was done at the factory. Now, compare the height of the piece that goes across the front, the area that rivets to the canopy. The right side is .1 inches shorter.
Rear side moldings:
These seem to fit pretty well. I was surprised. The contour on both pieces, however, at the rear, is not the same shape as the window. This requires trim-to-fit distance to the window to be shallow in the middle of the molding. The left piece is not molded correctly at the top front corner. It's actually curved too much. I had to heat it with a heat gun and reshape so the corner fit.
I'm sure a lot of you have not had any trouble installing this plastic. My objection is, too much time is spent 'trim-to-fit' on nearly all parts for planes. It doesn't need to be this way. Including, holding the little butterfly clips in place on some of the instruments with one hand and putting a screw in with the other. How difficult would it be to change the drawing to include a threaded hole?
If Kevin wanted to really make some money on these, he should consider items that should be changed to make assembly the plane as straight forward and efficient as possible. Suggestion: Headliners on cars are a molded piece of cardboard with the headliner material on it. That piece could me made to incorporate the rear window moldings as well. Imagine, installing the complete cabin interior by popping in preformed panels that include the window moldings and headliner. Save about 10 hours. It would weigh about the same too. Plus, it would add sound deadening with no extra weight penalty.
[quote][b]
| - The Matronics TeamGrumman-List Email Forum - | | Use the List Feature Navigator to browse the many List utilities available such as the Email Subscriptions page, Archive Search & Download, 7-Day Browse, Chat, FAQ, Photoshare, and much more:
http://www.matronics.com/Navigator?TeamGrumman-List |
|
|
|
Back to top |
|
 |
garnerrice(at)hotmail.com Guest
|
Posted: Wed Jun 23, 2010 3:36 pm Post subject: Interior plastic |
|
|
Garyly
�
The pastics are from Vantage Plane Plastics in Oklahoma. It's not factory or mine, so changing things up woudl be the responsibility of the production holder. If you look at the PMA tag on the parts, it will show what is required per part 45.
I know that someday you will be happy when you get some new trifocals. You old fart
�
I have an extra walker for you at the convention.
�
Garner
�
�
Date: Wed, 23 Jun 2010 13:07:07 -0700
From: teamgrumman(at)YAHOO.COM
Subject: Interior plastic
To: teamgrumman-list(at)matronics.com; JKevinL(at)bellsouth.net
.ExternalClass DIV {;} I'm installing windows and new plastic in a Cheetah. �New headliner in the cabin and canopy too. �
The new stuff is semi-trimmed to fit as it comes. �That saves a lot of time. �I've mentioned to Garner before about the poor fitting of the plastic. �I know it isn't his fault. �I would have thought by now, with planes as recent as 2005, that the tooling would have been corrected. �The added time to install stuff that doesn't fit surely must add to the time it takes to build the plane. �
Canopy plastic: �
��Garner, get both pieces and lay them side-by-side. �Compare the back of each piece to each other. �You'll notice the shape of the right piece, at the aft edge, is molded quite differently from the left. �The left is correct. �The right side is also about 1/4 inch too short. �It's impossible to rivet it to the trailing edge as was done at the factory. �Now, compare the height of the piece that goes across the front, the area that rivets to the canopy. �The right side is .1 inches shorter. �
Rear side moldings:
�These seem to fit pretty well. �I was surprised. �The contour on both pieces, however, at the rear, is not the same shape as the window. �This requires trim-to-fit distance to the window to be shallow in the middle of the molding. �The left piece is not molded correctly at the top front corner. �It's actually curved too much. �I had to heat it with a heat gun and reshape so the corner fit. �
I'm sure a lot of you have not had any trouble installing this plastic. �My objection is, too much time is spent 'trim-to-fit' on nearly all parts for planes. �It doesn't need to be this way. �Including, holding the little butterfly clips in place on some of the instruments with one hand and putting a screw in with the other. �How difficult would it be to change the drawing to include a threaded hole?
If Kevin wanted to really make some money on these, he should consider items that should be changed to make assembly the plane as straight forward and efficient as possible. �Suggestion: �Headliners on cars are a molded piece of cardboard with the headliner material on it. �That piece could me made to incorporate the rear window moldings as well. �Imagine, installing the complete cabin interior by popping in preformed panels that include the window moldings and headliner. �Save about 10 hours. �It would weigh about the same too. �Plus, it would add sound deadening with no extra weight penalty. �
Quote: |
List">http://www.matronics.com/Navigator?TeamGrumman-List
ronics.com
ww.matronics.com/contribution
| The New Busy think 9 to 5 is a cute idea. Combine multiple calendars with Hotmail. Get busy. [quote][b]
| - The Matronics TeamGrumman-List Email Forum - | | Use the List Feature Navigator to browse the many List utilities available such as the Email Subscriptions page, Archive Search & Download, 7-Day Browse, Chat, FAQ, Photoshare, and much more:
http://www.matronics.com/Navigator?TeamGrumman-List |
|
|
|
Back to top |
|
 |
teamgrumman(at)YAHOO.COM Guest
|
Posted: Wed Jun 23, 2010 7:51 pm Post subject: Interior plastic |
|
|
I wish I had the spare time and money to make plastic parts that actually fit. I still haven't made the tooling for the cup holder.
From: Garner Rice <garnerrice(at)hotmail.com>
To: teamgrumman-list(at)matronics.com
Sent: Wed, June 23, 2010 4:30:36 PM
Subject: RE: Interior plastic
Garyly
The pastics are from Vantage Plane Plastics in Oklahoma. It's not factory or mine, so changing things up woudl be the responsibility of the production holder. If you look at the PMA tag on the parts, it will show what is required per part 45.
I know that someday you will be happy when you get some new trifocals. You old fart
I have an extra walker for you at the convention.
Garner
Date: Wed, 23 Jun 2010 13:07:07 -0700
From: teamgrumman(at)YAHOO.COM
Subject: Interior plastic
To: teamgrumman-list(at)matronics.com; JKevinL(at)bellsouth.net
.ExternalClass DIV {} I'm installing windows and new plastic in a Cheetah. New headliner in the cabin and canopy too.
The new stuff is semi-trimmed to fit as it comes. That saves a lot of time. I've mentioned to Garner before about the poor fitting of the plastic. I know it isn't his fault. I would have thought by now, with planes as recent as 2005, that the tooling would have been corrected. The added time to install stuff that doesn't fit surely must add to the time it takes to build the plane.
Canopy plastic:
Garner, get both pieces and lay them side-by-side. Compare the back of each piece to each other. You'll notice the shape of the right piece, at the aft edge, is molded quite differently from the left. The left is correct. The right side is also about 1/4 inch too short. It's impossible to rivet it to the trailing edge as was done at the factory. Now, compare the height of the piece that goes across the front, the area that rivets to the canopy. The right side is .1 inches shorter.
Rear side moldings:
These seem to fit pretty well. I was surprised. The contour on both pieces, however, at the rear, is not the same shape as the window. This requires trim-to-fit distance to the window to be shallow in the middle of the molding. The left piece is not molded correctly at the top front corner. It's actually curved too much. I had to heat it with a heat gun and reshape so the corner fit.
I'm sure a lot of you have not had any trouble installing this plastic. My objection is, too much time is spent 'trim-to-fit' on nearly all parts for planes. It doesn't need to be this way. Including, holding the little butterfly clips in place on some of the instruments with one hand and putting a screw in with the other. How difficult would it be to change the drawing to include a threaded hole?
If Kevin wanted to really make some money on these, he should consider items that should be changed to make assembly the plane as straight forward and efficient as possible. Suggestion: Headliners on cars are a molded piece of cardboard with the headliner material on it. That piece could me made to incorporate the rear window moldings as well. Imagine, installing the complete cabin interior by popping in preformed panels that include the window moldings and headliner. Save about 10 hours. It would weigh about the same too. Plus, it would add sound deadening with no extra weight penalty.
The New Busy think 9 to 5 is a cute idea. Combine multiple calendars with Hotmail. Get busy.
[quote][b]
| - The Matronics TeamGrumman-List Email Forum - | | Use the List Feature Navigator to browse the many List utilities available such as the Email Subscriptions page, Archive Search & Download, 7-Day Browse, Chat, FAQ, Photoshare, and much more:
http://www.matronics.com/Navigator?TeamGrumman-List |
|
|
|
Back to top |
|
 |
|
|
You cannot post new topics in this forum You cannot reply to topics in this forum You cannot edit your posts in this forum You cannot delete your posts in this forum You cannot vote in polls in this forum You cannot attach files in this forum You can download files in this forum
|
Powered by phpBB © 2001, 2005 phpBB Group
|