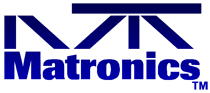 |
Matronics Email Lists Web Forum Interface to the Matronics Email Lists
|
View previous topic :: View next topic |
Author |
Message |
email(at)jaredyates.com Guest
|
Posted: Wed Jan 19, 2011 5:52 am Post subject: Crimping Big Lugs |
|
|
I've been crimping a few 4-gauge welding cables with lugs that I also got from the welding supplier. The lugs and cable are both labeled #4, but the lugs are bigger than I would think that they should be. The fit is very loose before crimping, which means that after I crimp them in my whack-a-mole crimper I end up with quite a bit of daylight on either side of the cable strands. While I'm keeping in mind that the term "gas tight" describes the ideal crimp, I'm concerned that these crimps may not be optimal. Has anyone else noticed this problem? Is it a problem, or does it just look odd? These are obviously some pretty important connections that I'd rather not have any trouble out of once they are in service. [quote][b]
| - The Matronics AeroElectric-List Email Forum - | | Use the List Feature Navigator to browse the many List utilities available such as the Email Subscriptions page, Archive Search & Download, 7-Day Browse, Chat, FAQ, Photoshare, and much more:
http://www.matronics.com/Navigator?AeroElectric-List |
|
|
|
Back to top |
|
 |
recapen(at)earthlink.net Guest
|
Posted: Wed Jan 19, 2011 6:07 am Post subject: Crimping Big Lugs |
|
|
When I did mine I couldn't see through them at the end after they were completed.
I got my lugs from the same folks that sold me the Whack-A-Mole crimper....B&C if I recall correctly......
--
| - The Matronics AeroElectric-List Email Forum - | | Use the List Feature Navigator to browse the many List utilities available such as the Email Subscriptions page, Archive Search & Download, 7-Day Browse, Chat, FAQ, Photoshare, and much more:
http://www.matronics.com/Navigator?AeroElectric-List |
|
|
|
Back to top |
|
 |
email(at)jaredyates.com Guest
|
Posted: Wed Jan 19, 2011 6:35 am Post subject: Crimping Big Lugs |
|
|
The end is closed on these lugs, so I can't see through them, but there is a lot of space in the finished lug.
On Jan 19, 2011, at 9:04, "Ralph E. Capen" <recapen(at)earthlink.net> wrote:
[quote]
When I did mine I couldn't see through them at the end after they were completed.
I got my lugs from the same folks that sold me the Whack-A-Mole crimper....B&C if I recall correctly......
--
| - The Matronics AeroElectric-List Email Forum - | | Use the List Feature Navigator to browse the many List utilities available such as the Email Subscriptions page, Archive Search & Download, 7-Day Browse, Chat, FAQ, Photoshare, and much more:
http://www.matronics.com/Navigator?AeroElectric-List |
|
|
|
Back to top |
|
 |
recapen(at)earthlink.net Guest
|
Posted: Wed Jan 19, 2011 6:45 am Post subject: Crimping Big Lugs |
|
|
I would be concerned that I have used the correct size lug for the wire?!
--
| - The Matronics AeroElectric-List Email Forum - | | Use the List Feature Navigator to browse the many List utilities available such as the Email Subscriptions page, Archive Search & Download, 7-Day Browse, Chat, FAQ, Photoshare, and much more:
http://www.matronics.com/Navigator?AeroElectric-List |
|
|
|
Back to top |
|
 |
nuckolls.bob(at)aeroelect Guest
|
Posted: Wed Jan 19, 2011 6:53 am Post subject: Crimping Big Lugs |
|
|
At 08:46 AM 1/19/2011, you wrote:
I've been crimping a few 4-gauge welding cables with lugs that I also
got from the welding supplier. The lugs and cable are both labeled
#4, but the lugs are bigger than I would think that they should
be. The fit is very loose before crimping, which means that after I
crimp them in my whack-a-mole crimper I end up with quite a bit of
daylight on either side of the cable strands. While I'm keeping in
mind that the term "gas tight" describes the ideal crimp, I'm
concerned that these crimps may not be optimal.
It is a certainty that they are not . . .
Has anyone else noticed this problem? Is it a problem, or does it
just look odd? These are obviously some pretty important connections
that I'd rather not have any trouble out of once they are in service.
What you're experiencing first hand is an enduring
question as to effectiveness of mating wire size (A)
with terminal (B) installed with tool (C) operated
by craftsman (D).
Companies like AMP, T&B, Daniels, Molex, et. als.
have invested $millions$ in designing and fabricating
both tools and terminals that minimize risks in the
A+B+C+D equation.
I produced two articles some years back. Several of which
spoke to the idealized end-game for terminal
application
www.aeroelectric.com/articles/terminal.pdf
www.aeroelectric.com/articles/CrimpTools/crimptools.html
and another which provided a work-around for
making high quality installations of big terminals
with virtually zero-risk for loss of electrical
integrity with time in service . . .
www.aeroelectric.com/articles/big_term.pdf
We also discussed a number of articles wherein
the authors seemed not to know or care about
the simple-ideas that support all the work
and receipes for success developed by the companies
cited above.
http://www.aeroelectric.com/articles/rules/review.html
www.aeroelectric.com/articles/Wired_for_Disaster.pdf
A couple of years ago, we all read in wonderment
about an unplanned arrival with the earth experienced
by an RV builder wherein accident investigators
noted "wires pulled from their terminals" either
as a result of the accident or perhaps they came
out before and contributed to the accident. This
was an extreme example to be sure.
But why treat your terminal applications any
differently than you would treat installation
of a rivet? The problem is that the quality
of an rivet installation is a pretty much a
visual inspection thing. What goes on down
inside the strands of wire being joined to
a terminal is quite another matter.
The hedge against building un-inspectable risk
into your project is to exploit recipes for success.
Any time a particular combination of A+B+C+D
come together, they should be evaluated for
the suitability of EACH ingredient.
It sounds like the terminals (B) you spoke of are
not matched to the wire (A) and the suggested tool (C)
is perhaps not matched to either.
For myself, I don't even own crimping tools
that are whacked or jacked together with
screws. I have some low cost, tools that
are used with attention to detail based on
decades of experience. For all the problems
you have to wrestle with in fabricating your
airplane, terminal application should be the
very least of your worries. Clearly a new
combination of A+B+C is called for.
The good news is that the craftsman (D) has
observed, "maybe that doesn't look right".
Bob . . .
| - The Matronics AeroElectric-List Email Forum - | | Use the List Feature Navigator to browse the many List utilities available such as the Email Subscriptions page, Archive Search & Download, 7-Day Browse, Chat, FAQ, Photoshare, and much more:
http://www.matronics.com/Navigator?AeroElectric-List |
|
|
|
Back to top |
|
 |
email(at)jaredyates.com Guest
|
Posted: Wed Jan 19, 2011 7:24 am Post subject: Crimping Big Lugs |
|
|
Thanks Bob, I hadn't seen all of those articles yet. The "big terminal" article looks especially helpful.
On Wed, Jan 19, 2011 at 8:48 AM, Robert L. Nuckolls, III <nuckolls.bob(at)aeroelectric.com (nuckolls.bob(at)aeroelectric.com)> wrote:
[quote]--> AeroElectric-List message posted by: "Robert L. Nuckolls, III" <nuckolls.bob(at)aeroelectric.com (nuckolls.bob(at)aeroelectric.com)>
At 08:46 AM 1/19/2011, you wrote:
I've been crimping a few 4-gauge welding cables with lugs that I also got from the welding supplier. The lugs and cable are both labeled #4, but the lugs are bigger than I would think that they should be. The fit is very loose before crimping, which means that after I crimp them in my whack-a-mole crimper I end up with quite a bit of daylight on either side of the cable strands. While I'm keeping in mind that the term "gas tight" describes the ideal crimp, I'm concerned that these crimps may not be optimal.
It is a certainty that they are not . . .
Has anyone else noticed this problem? Is it a problem, or does it just look odd? These are obviously some pretty important connections that I'd rather not have any trouble out of once they are in service.
What you're experiencing first hand is an enduring
question as to effectiveness of mating wire size (A)
with terminal (B) installed with tool (C) operated
by craftsman (D).
Companies like AMP, T&B, Daniels, Molex, et. als.
have invested $millions$ in designing and fabricating
both tools and terminals that minimize risks in the
A+B+C+D equation.
I produced two articles some years back. Several of which
spoke to the idealized end-game for terminal
application
www.aeroelectric.com/articles/terminal.pdf
www.aeroelectric.com/articles/CrimpTools/crimptools.html
and another which provided a work-around for
making high quality installations of big terminals
with virtually zero-risk for loss of electrical
integrity with time in service . . .
www.aeroelectric.com/articles/big_term.pdf
We also discussed a number of articles wherein
the authors seemed not to know or care about
the simple-ideas that support all the work
and receipes for success developed by the companies
cited above.
http://www.aeroelectric.com/articles/rules/review.html
www.aeroelectric.com/articles/Wired_for_Disaster.pdf
A couple of years ago, we all read in wonderment
about an unplanned arrival with the earth experienced
by an RV builder wherein accident investigators
noted "wires pulled from their terminals" either
as a result of the accident or perhaps they came
out before and contributed to the accident. This
was an extreme example to be sure.
But why treat your terminal applications any
differently than you would treat installation
of a rivet? The problem is that the quality
of an rivet installation is a pretty much a
visual inspection thing. What goes on down
inside the strands of wire being joined to
a terminal is quite another matter.
The hedge against building un-inspectable risk
into your project is to exploit recipes for success.
Any time a particular combination of A+B+C+D
come together, they should be evaluated for
the suitability of EACH ingredient.
It sounds like the terminals (B) you spoke of are
not matched to the wire (A) and the suggested tool (C)
is perhaps not matched to either.
For myself, I don't even own crimping tools
that are whacked or jacked together with
screws. I have some low cost, tools that
are used with attention to detail based on
decades of experience. For all the problems
you have to wrestle with in fabricating your
airplane, terminal application should be the
very least of your worries. Clearly a new
combination of A+B+C is called for.
The good news is that the craftsman (D) has
observed, "maybe that doesn't look right".
Bob . . .
===========
-List" target="_blank">http://www.matronics.com/Navigator?AeroElectric-List
===========
http://forums.matronics.com
===========
le, List Admin.
="_blank">http://www.matronics.com/contribution
===========
[b]
| - The Matronics AeroElectric-List Email Forum - | | Use the List Feature Navigator to browse the many List utilities available such as the Email Subscriptions page, Archive Search & Download, 7-Day Browse, Chat, FAQ, Photoshare, and much more:
http://www.matronics.com/Navigator?AeroElectric-List |
|
|
|
Back to top |
|
 |
Float Flyr
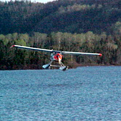
Joined: 19 Jul 2006 Posts: 2704 Location: Campbellton, Newfoundland
|
Posted: Wed Jan 19, 2011 7:39 am Post subject: Crimping Big Lugs |
|
|
Sounds to me like your crimp is not right. I would try inserting the wire into the lug and then collapsing the middle of the crimp ring with a cold chisel positioned parallel to the wire in the ring then fold the ring almost in half and give it the what for with your “Wack-a-mole” crimper.
If you can see light through the crimp that is a place for corrosion to start leading to inevitable failure.
Noel
From: owner-aeroelectric-list-server(at)matronics.com [mailto:owner-aeroelectric-list-server(at)matronics.com] On Behalf Of Jared Yates
Sent: January 19, 2011 10:16 AM
To: aeroelectric-list(at)matronics.com
Subject: Crimping Big Lugs
I've been crimping a few 4-gauge welding cables with lugs that I also got from the welding supplier. The lugs and cable are both labeled #4, but the lugs are bigger than I would think that they should be. The fit is very loose before crimping, which means that after I crimp them in my whack-a-mole crimper I end up with quite a bit of daylight on either side of the cable strands. While I'm keeping in mind that the term "gas tight" describes the ideal crimp, I'm concerned that these crimps may not be optimal. Has anyone else noticed this problem? Is it a problem, or does it just look odd? These are obviously some pretty important connections that I'd rather not have any trouble out of once they are in service. Quote: | http://www.matronics.com/Navigator?AeroElectric-List | 01234567
[quote][b]
| - The Matronics AeroElectric-List Email Forum - | | Use the List Feature Navigator to browse the many List utilities available such as the Email Subscriptions page, Archive Search & Download, 7-Day Browse, Chat, FAQ, Photoshare, and much more:
http://www.matronics.com/Navigator?AeroElectric-List |
|
_________________ Noel Loveys
Kitfox III-A
Aerocet 1100 Floats |
|
Back to top |
|
 |
Float Flyr
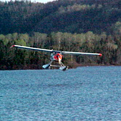
Joined: 19 Jul 2006 Posts: 2704 Location: Campbellton, Newfoundland
|
Posted: Wed Jan 19, 2011 8:08 am Post subject: Crimping Big Lugs |
|
|
The end of the lug should be open so you can be sure of proper penetration
into the fitting.
Noel
--
| - The Matronics AeroElectric-List Email Forum - | | Use the List Feature Navigator to browse the many List utilities available such as the Email Subscriptions page, Archive Search & Download, 7-Day Browse, Chat, FAQ, Photoshare, and much more:
http://www.matronics.com/Navigator?AeroElectric-List |
|
_________________ Noel Loveys
Kitfox III-A
Aerocet 1100 Floats |
|
Back to top |
|
 |
pwmac(at)sisna.com Guest
|
Posted: Wed Jan 19, 2011 8:55 am Post subject: Crimping Big Lugs |
|
|
These discussions on crimoing big lugs is interesting.
My method is to take the parts to the battery store and have them
crimp them with their high leverage crimper. They have dies for all
sizes and combos of lugs & wires. The same store stocks lugs (open or
closed) and the welding cable in several styles. The cost for the
crimping was minimal and they always included the heat shrink in
black or red. They were glad to help.
To find a proper battery store look for the stores that cater to
the solar people.
Paul
===========
| - The Matronics AeroElectric-List Email Forum - | | Use the List Feature Navigator to browse the many List utilities available such as the Email Subscriptions page, Archive Search & Download, 7-Day Browse, Chat, FAQ, Photoshare, and much more:
http://www.matronics.com/Navigator?AeroElectric-List |
|
|
|
Back to top |
|
 |
nuckolls.bob(at)aeroelect Guest
|
Posted: Wed Jan 19, 2011 9:23 am Post subject: Crimping Big Lugs |
|
|
At 11:50 AM 1/19/2011, you wrote:
These discussions on crimoing big lugs is interesting.
My method is to take the parts to the battery store and have them
crimp them with their high leverage crimper. They have dies for all
sizes and combos of lugs & wires. The same store stocks lugs (open or
closed) and the welding cable in several styles. The cost for the
crimping was minimal and they always included the heat shrink in
black or red. They were glad to help.
To find a proper battery store look for the stores that cater to the
solar people.
An excellent A + B + C + D = recipe for success!
Bob . . .
| - The Matronics AeroElectric-List Email Forum - | | Use the List Feature Navigator to browse the many List utilities available such as the Email Subscriptions page, Archive Search & Download, 7-Day Browse, Chat, FAQ, Photoshare, and much more:
http://www.matronics.com/Navigator?AeroElectric-List |
|
|
|
Back to top |
|
 |
icubob(at)gmail.com Guest
|
Posted: Wed Jan 19, 2011 10:55 am Post subject: Crimping Big Lugs |
|
|
before i crimped i put as many 1/2'', 12 or 14 solid copper wire pieces in the lug as i could fit/tap in. then the lug didn't deform so much when crimped and it was TIGHT.
bob noffs
On Wed, Jan 19, 2011 at 9:37 AM, Noel Loveys <noelloveys(at)yahoo.ca (noelloveys(at)yahoo.ca)> wrote:
[quote]
Sounds to me like your crimp is not right. I would try inserting the wire into the lug and then collapsing the middle of the crimp ring with a cold chisel positioned parallel to the wire in the ring then fold the ring almost in half and give it the what for with your “Wack-a-mole” crimper.
If you can see light through the crimp that is a place for corrosion to start leading to inevitable failure.
Noel
From: owner-aeroelectric-list-server(at)matronics.com (owner-aeroelectric-list-server(at)matronics.com) [mailto:owner-aeroelectric-list-server(at)matronics.com (owner-aeroelectric-list-server(at)matronics.com)] On Behalf Of Jared Yates
Sent: January 19, 2011 10:16 AM
To: aeroelectric-list(at)matronics.com (aeroelectric-list(at)matronics.com)
Subject: Crimping Big Lugs
I've been crimping a few 4-gauge welding cables with lugs that I also got from the welding supplier. The lugs and cable are both labeled #4, but the lugs are bigger than I would think that they should be. The fit is very loose before crimping, which means that after I crimp them in my whack-a-mole crimper I end up with quite a bit of daylight on either side of the cable strands. While I'm keeping in mind that the term "gas tight" describes the ideal crimp, I'm concerned that these crimps may not be optimal. Has anyone else noticed this problem? Is it a problem, or does it just look odd? These are obviously some pretty important connections that I'd rather not have any trouble out of once they are in service. 0 1234
5 67
8
[b]
| - The Matronics AeroElectric-List Email Forum - | | Use the List Feature Navigator to browse the many List utilities available such as the Email Subscriptions page, Archive Search & Download, 7-Day Browse, Chat, FAQ, Photoshare, and much more:
http://www.matronics.com/Navigator?AeroElectric-List |
|
|
|
Back to top |
|
 |
nuckolls.bob(at)aeroelect Guest
|
Posted: Wed Jan 19, 2011 11:16 am Post subject: Crimping Big Lugs |
|
|
At 01:51 PM 1/19/2011, you wrote:
Quote: | before i crimped i put as many 1/2'', 12 or 14 solid copper wire
pieces in the lug as i could fit/tap in. then the lug didn't deform
so much when crimped and it was TIGHT.
|
But was it GAS TIGHT? Unless you cross-section
the joint and get a picture like
http://aeroelectric.com/articles/CrimpTools/GL.jpg
moisture and oxygen can get in and start working
on the joint. It's like copper eating termites.
This is particularly important with fat-wires where
the corrosion process is aided and abetted by the
flow of electrons across the compromised areas of
the joint.
Just because your finished task is mechanically
'tight' is not 99.9% probability of good outcome.
Bob . . .
| - The Matronics AeroElectric-List Email Forum - | | Use the List Feature Navigator to browse the many List utilities available such as the Email Subscriptions page, Archive Search & Download, 7-Day Browse, Chat, FAQ, Photoshare, and much more:
http://www.matronics.com/Navigator?AeroElectric-List |
|
|
|
Back to top |
|
 |
|
|
You cannot post new topics in this forum You cannot reply to topics in this forum You cannot edit your posts in this forum You cannot delete your posts in this forum You cannot vote in polls in this forum You cannot attach files in this forum You can download files in this forum
|
Powered by phpBB © 2001, 2005 phpBB Group
|