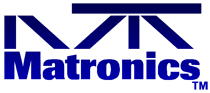 |
Matronics Email Lists Web Forum Interface to the Matronics Email Lists
|
View previous topic :: View next topic |
Author |
Message |
sean(at)stephensville.com Guest
|
Posted: Fri Apr 29, 2011 7:09 am Post subject: Flare Fitting Torque |
|
|
On 4/28/11 2:03 PM, John Cox wrote:
Quote: | As a Tech Advisor, no one wants to hear from us how often we find flares
on tubing incorrectly manufactured or improperly torqued (under and
over)
I changed the subject line to start a new thread here.
|
Yes, this brought me back to reviewing what I need to do in the tunnel.
I wanted to put this info out there to make sure I am "doing it right".
In AC 43.13-1B CHG1 on page 9-19 there is a table for flare nut torque
values.
-4 nut = 50-65 inch pounds
-6 nut = 110-130 inch pounds
Also on page 7-8 of AC 43.13-1B there is a formula for determining the
correct torque reading when using adapters such as crows feet.
E - Distance from drive centerline to adapter centerline
T - Recommended torque value
L - Length or torque wrench, drive centerline to handle centerline
Y - What the wrench should be set at with adapter in place
TxL / L+E = Y
So for my wrench with a crows foot and to torque a -6 flare nut to 110
inch lbs works out like this...
110x10 / 10+1 = 100
My wrench should be set at 100 and *not* 110 in this case.
So, do I have all this right? A few questions..
1. I've seen different tables out there with different torque values
for the flare nuts. Is what I'm using above correct?
2. So the torque range for -4 above is 50-65. What do people use to
set their wrench? low end of 50? high end of 65? Split the difference
for 57?
2. There are some places in the tunnel where it just doesn't work
getting a torque wrench in there even with a crows foot and/or
extension. What are folks doing in this case?
-Sean #40303
| - The Matronics RV10-List Email Forum - | | Use the List Feature Navigator to browse the many List utilities available such as the Email Subscriptions page, Archive Search & Download, 7-Day Browse, Chat, FAQ, Photoshare, and much more:
http://www.matronics.com/Navigator?RV10-List |
|
|
|
Back to top |
|
 |
AV8ORJWC
Joined: 13 Jul 2006 Posts: 1149 Location: Aurora, Oregon "Home of VANS"
|
Posted: Fri Apr 29, 2011 10:48 am Post subject: Flare Fitting Torque |
|
|
Each builder is the Manufacturer (not VANS), many have happily followed
the mantra "just build it". Every builder receiving my Tech Inspection
hears the story of hats. On this list most of the readers are wearing
"The Builder/Manufacturer" hat. The moment the DAR is through with his
paperwork, you will learn the perspective of wearing "The Technician's"
hat. Often profanity follows and a dialog which goes something like
"Why didn't I think of that".
Access to an area, service loops, application of torque to any fitting
carrying fluids, support of electrical wires from chafing, they all play
into the dialog.
The reason for at least two tables are possibly the difference in B nut
construction between aluminum or steel. The proper use of a torque
wrench requires access, range of movement and proper application.
Hopefully the torque reading required is not at the lowest or highest
end of the measurement range. Both "under-torque" or more common "over
torque" lead to potential leaks and product failures. Every time you
open/loosen a fitting on a fluid line, you should pressurize, fly the
aircraft then reinspect for telltale signs. An improperly formed flare,
an over-torqued fitting, weak aluminum tubing or angular mis-match can
lead to potential leaks. Always remember to have the input or output
tubing with a bend to take up errors of using a straight run that can be
too short or too long.
Access to the tunnel whether from your favorite side or from the bottom
seem good points of consideration.
Think about what it will feel like when you re-enter a space for
servicing. Several of the readers have been great on the "I would have
done it this way, or I am thinking about changing" the product provided
or method suggested by a parts supplier.
AC 43.13 is only a baseline in the absence of one selected method or
standard by the responsible manufacturer. Often, such as with
electrical considerations, much has improved over the ideas of the
1940's - 50s techniques. Chose wisely.
In the absence of a standard in Experimental Built, Anything Goes. It's
an experiment. We are blessed with many somewhat similar aircraft in
reasonably similar construction.
On your torque calculation problem you did not mention if the 1" was
straight in line, at a 90 degree or some variant. Prop Hub bolts
provide a challenge.
John -#40600
--
| - The Matronics RV10-List Email Forum - | | Use the List Feature Navigator to browse the many List utilities available such as the Email Subscriptions page, Archive Search & Download, 7-Day Browse, Chat, FAQ, Photoshare, and much more:
http://www.matronics.com/Navigator?RV10-List |
|
|
|
Back to top |
|
 |
Deems Davis
Joined: 09 Jan 2006 Posts: 925
|
Posted: Fri Apr 29, 2011 11:15 am Post subject: Flare Fitting Torque |
|
|
Perhaps a larger potential problem than torque values for B nuts , is
how to construct the proper flare. There are several different tools for
doing so, and the techniques of using the tools vary, It's quite
possible with at least one tool (Parker) to 'over torque' the flaring
tool and product a flare that becomes too thin and subject to breaking.
(Ask me how I know:-) ). Years ago I posted my experience of
'accidentally' finding that some fuel lines in the tunnel had been 'over
flared' and 'over torqued' and resulted in the flare breaking and the
line pulling free from the B nut! Fortunately I found it and redid all
of the alum lines, or I would have found myself in a similar situation
as Ted.
Deems
| - The Matronics RV10-List Email Forum - | | Use the List Feature Navigator to browse the many List utilities available such as the Email Subscriptions page, Archive Search & Download, 7-Day Browse, Chat, FAQ, Photoshare, and much more:
http://www.matronics.com/Navigator?RV10-List |
|
|
|
Back to top |
|
 |
sean(at)stephensville.com Guest
|
Posted: Fri Apr 29, 2011 11:26 am Post subject: Flare Fitting Torque |
|
|
Sorry, yes the 1" is straight inline.
So if I understand correctly with the torque range, it's best to split
the difference as to be further away from both under and over torque.
The range numbers I gave were for Aluminum. Are the numbers below what
other builders are using? I'd like to "chose wisely" in this particular
case, but my choice is what the piece of paper tells me.
-4 nut = 50-65 inch pounds
-6 nut = 110-130 inch pounds
Thanks,
-Sean #40303
On 4/29/11 1:42 PM, John Cox wrote:
[quote]
Each builder is the Manufacturer (not VANS), many have happily followed
the mantra "just build it". Every builder receiving my Tech Inspection
hears the story of hats. On this list most of the readers are wearing
"The Builder/Manufacturer" hat. The moment the DAR is through with his
paperwork, you will learn the perspective of wearing "The Technician's"
hat. Often profanity follows and a dialog which goes something like
"Why didn't I think of that".
Access to an area, service loops, application of torque to any fitting
carrying fluids, support of electrical wires from chafing, they all play
into the dialog.
The reason for at least two tables are possibly the difference in B nut
construction between aluminum or steel. The proper use of a torque
wrench requires access, range of movement and proper application.
Hopefully the torque reading required is not at the lowest or highest
end of the measurement range. Both "under-torque" or more common "over
torque" lead to potential leaks and product failures. Every time you
open/loosen a fitting on a fluid line, you should pressurize, fly the
aircraft then reinspect for telltale signs. An improperly formed flare,
an over-torqued fitting, weak aluminum tubing or angular mis-match can
lead to potential leaks. Always remember to have the input or output
tubing with a bend to take up errors of using a straight run that can be
too short or too long.
Access to the tunnel whether from your favorite side or from the bottom
seem good points of consideration.
Think about what it will feel like when you re-enter a space for
servicing. Several of the readers have been great on the "I would have
done it this way, or I am thinking about changing" the product provided
or method suggested by a parts supplier.
AC 43.13 is only a baseline in the absence of one selected method or
standard by the responsible manufacturer. Often, such as with
electrical considerations, much has improved over the ideas of the
1940's - 50s techniques. Chose wisely.
In the absence of a standard in Experimental Built, Anything Goes. It's
an experiment. We are blessed with many somewhat similar aircraft in
reasonably similar construction.
On your torque calculation problem you did not mention if the 1" was
straight in line, at a 90 degree or some variant. Prop Hub bolts
provide a challenge.
John -#40600
--
| - The Matronics RV10-List Email Forum - | | Use the List Feature Navigator to browse the many List utilities available such as the Email Subscriptions page, Archive Search & Download, 7-Day Browse, Chat, FAQ, Photoshare, and much more:
http://www.matronics.com/Navigator?RV10-List |
|
|
|
Back to top |
|
 |
Tim Olson
Joined: 25 Jan 2007 Posts: 2879
|
Posted: Fri Apr 29, 2011 11:40 am Post subject: Flare Fitting Torque |
|
|
This was one of my motivations for going to flex lines. At least
in that case you're going with lines that have no need to flare,
no worries about improper flares, no "learning curve" to getting
the right flare quality. I wanted my lines to be leak free
and work right out of the box...and the best way to do that is
to 1) eliminate as many connection points as you can, and 2) use
some pre-made lines. The quality of the tubing I had received
was also questionable...at times it would develop what was
kind of like galling and sometimes cracking, along what appeared
to be a grain in the metal somewhat. I ordered some additional
tubing from ACS and from Vans, and different batches of the same
material weren't as bad. So I never really fully trusted
the 3/8" lines that were produced from the material I got.
I'm still leery of the one going to the firewall...and would
love to change it out some day.
Tim Olson - RV-10 N104CD
do not archive
On 4/29/2011 2:10 PM, Deems Davis wrote:
Quote: |
Perhaps a larger potential problem than torque values for B nuts , is
how to construct the proper flare. There are several different tools for
doing so, and the techniques of using the tools vary, It's quite
possible with at least one tool (Parker) to 'over torque' the flaring
tool and product a flare that becomes too thin and subject to breaking.
(Ask me how I know:-) ). Years ago I posted my experience of
'accidentally' finding that some fuel lines in the tunnel had been 'over
flared' and 'over torqued' and resulted in the flare breaking and the
line pulling free from the B nut! Fortunately I found it and redid all
of the alum lines, or I would have found myself in a similar situation
as Ted.
Deems
|
| - The Matronics RV10-List Email Forum - | | Use the List Feature Navigator to browse the many List utilities available such as the Email Subscriptions page, Archive Search & Download, 7-Day Browse, Chat, FAQ, Photoshare, and much more:
http://www.matronics.com/Navigator?RV10-List |
|
|
|
Back to top |
|
 |
rv10flyer
Joined: 25 Aug 2009 Posts: 364
|
Posted: Fri Apr 29, 2011 4:35 pm Post subject: Use 5052-O aluminum tubing for fuel and brake lines |
|
|
instead of Van's supplied 3003-O. My 3003-O went in with my aluminum hvac scrap.
5052 has nearly twice the fatigue and tensile strength. 5052-O is used on certified aircraft for a reason. As noted above it flares much nicer. I used Bonaco flex hoses at the pedals and down the gear legs.
| - The Matronics RV10-List Email Forum - | | Use the List Feature Navigator to browse the many List utilities available such as the Email Subscriptions page, Archive Search & Download, 7-Day Browse, Chat, FAQ, Photoshare, and much more:
http://www.matronics.com/Navigator?RV10-List |
|
_________________ Wayne G. |
|
Back to top |
|
 |
AV8ORJWC
Joined: 13 Jul 2006 Posts: 1149 Location: Aurora, Oregon "Home of VANS"
|
Posted: Fri Apr 29, 2011 10:02 pm Post subject: Flare Fitting Torque |
|
|
Improved product quality helps in the overall build. Getting rid of
H-5606 and upgrading hydraulic fluid is another Manufacturer decision.
Great call Wayne.
John
--
| - The Matronics RV10-List Email Forum - | | Use the List Feature Navigator to browse the many List utilities available such as the Email Subscriptions page, Archive Search & Download, 7-Day Browse, Chat, FAQ, Photoshare, and much more:
http://www.matronics.com/Navigator?RV10-List |
|
|
|
Back to top |
|
 |
kearney
Joined: 20 Sep 2008 Posts: 563
|
Posted: Sat Apr 30, 2011 7:07 pm Post subject: Flare Fitting Torque |
|
|
John et al
The flash point of Aeroshell 31 is 83 degrees C. The flash point of
Aeroshell 41 is 254 degreees C. Take you pick. I seem to recall reading of
brake fires due to leaking brake fluid onto hot brakes.
I believe the cost difference is trival.
Cheers
Les
--
| - The Matronics RV10-List Email Forum - | | Use the List Feature Navigator to browse the many List utilities available such as the Email Subscriptions page, Archive Search & Download, 7-Day Browse, Chat, FAQ, Photoshare, and much more:
http://www.matronics.com/Navigator?RV10-List |
|
|
|
Back to top |
|
 |
AV8ORJWC
Joined: 13 Jul 2006 Posts: 1149 Location: Aurora, Oregon "Home of VANS"
|
Posted: Sat Apr 30, 2011 7:51 pm Post subject: Flare Fitting Torque |
|
|
After seeing brake fluid fires, I do not recommend H-5606. Then again working with Skydrol (phosphate ester), I won't chose that either. Tim posted sources for 1 gallon cans of Aeroshell 41. It can make all the difference in a better day with composite wheel pants in close proximity to the heat and fuel.
John Cox
From: owner-rv10-list-server(at)matronics.com on behalf of Les Kearney
Sent: Sat 4/30/2011 9:13 AM
To: rv10-list(at)matronics.com
Subject: RE: Re: Flare Fitting Torque
--> RV10-List message posted by: "Les Kearney" <kearney(at)shaw.ca>
John et al
The flash point of Aeroshell 31 is 83 degrees C. The flash point of
Aeroshell 41 is 254 degreees C. Take you pick. I seem to recall reading of
brake fires due to leaking brake fluid onto hot brakes.
I believe the cost difference is trival.
Cheers
Les
--
| - The Matronics RV10-List Email Forum - | | Use the List Feature Navigator to browse the many List utilities available such as the Email Subscriptions page, Archive Search & Download, 7-Day Browse, Chat, FAQ, Photoshare, and much more:
http://www.matronics.com/Navigator?RV10-List |
|
|
|
Back to top |
|
 |
Kelly McMullen
Joined: 16 Apr 2008 Posts: 1188 Location: Sun Lakes AZ
|
Posted: Sun May 01, 2011 3:39 am Post subject: Flare Fitting Torque |
|
|
http://www.skygeek.com/royco-782-synthetic-fire-resistant-hydraulic-fluid.html
If you don't mind another brand, and don't want to have 3.5 qts unused for the life of your plane.
On Sat, Apr 30, 2011 at 12:13 PM, Les Kearney <kearney(at)shaw.ca (kearney(at)shaw.ca)> wrote:
[quote] --> RV10-List message posted by: "Les Kearney" <kearney(at)shaw.ca (kearney(at)shaw.ca)>
John et al
The flash point of Aeroshell 31 is 83 degrees C. The flash point of
Aeroshell 41 is 254 degreees C. Take you pick. I seem to recall reading of
brake fires due to leaking brake fluid onto hot brakes.
I believe the cost difference is trival.
Cheers
Les
--
| - The Matronics RV10-List Email Forum - | | Use the List Feature Navigator to browse the many List utilities available such as the Email Subscriptions page, Archive Search & Download, 7-Day Browse, Chat, FAQ, Photoshare, and much more:
http://www.matronics.com/Navigator?RV10-List |
|
_________________ Kelly McMullen
A&P/IA, EAA Tech Counselor
KCHD |
|
Back to top |
|
 |
dlm34077(at)q.com Guest
|
Posted: Sun May 01, 2011 7:15 am Post subject: Flare Fitting Torque |
|
|
another reason to pitch the vans tubing solution and install manufactured
Teflon lines with the stainless steel braid from fuselage bulkhead fitting
to brake..
---
| - The Matronics RV10-List Email Forum - | | Use the List Feature Navigator to browse the many List utilities available such as the Email Subscriptions page, Archive Search & Download, 7-Day Browse, Chat, FAQ, Photoshare, and much more:
http://www.matronics.com/Navigator?RV10-List |
|
|
|
Back to top |
|
 |
partner14
Joined: 12 Jan 2008 Posts: 540 Location: Granbury Texas
|
Posted: Sun May 01, 2011 7:42 am Post subject: Flare Fitting Torque |
|
|
Les, I think you got it backwards... Aeroshell 31 is 205C, and 41 is 90C.
Don McDonald
From: Les Kearney <kearney(at)shaw.ca>
To: rv10-list(at)matronics.com
Sent: Sat, April 30, 2011 11:13:07 AM
Subject: RE: Re: Flare Fitting Torque
--> RV10-List message posted by: "Les Kearney" <kearney(at)shaw.ca (kearney(at)shaw.ca)>
John et al
The flash point of Aeroshell 31 is 83 degrees C. The flash point of
Aeroshell 41 is 254 degreees C. Take you pick. I seem to recall reading of
brake fires due to leaking brake fluid onto hot brakes.
I believe the cost difference is trival.
Cheers
Les
--
| - The Matronics RV10-List Email Forum - | | Use the List Feature Navigator to browse the many List utilities available such as the Email Subscriptions page, Archive Search & Download, 7-Day Browse, Chat, FAQ, Photoshare, and much more:
http://www.matronics.com/Navigator?RV10-List |
|
_________________ Don A. McDonald
40636 |
|
Back to top |
|
 |
gengrumpy(at)aol.com Guest
|
Posted: Sun May 01, 2011 8:38 am Post subject: Flare Fitting Torque |
|
|
Guys,
In the FWIW category, here is what I've been using for brake fluid since first flight in Nov 2006:
Valvoline DEX/MERC auto trans fluid VV324, flash point 202° C / 395° F.
It is readily available and very affordable.grumpy
N184JM
On May 1, 2011, at 10:40 AM, Don McDonald wrote:
[quote]Les, I think you got it backwards... Aeroshell 31 is 205C, and 41 is 90C.
Don McDonald
From: Les Kearney <kearney(at)shaw.ca (kearney(at)shaw.ca)>
To: rv10-list(at)matronics.com (rv10-list(at)matronics.com)
Sent: Sat, April 30, 2011 11:13:07 AM
Subject: RE: Re: Flare Fitting Torque
--> RV10-List message posted by: "Les Kearney" <kearney(at)shaw.ca (kearney(at)shaw.ca)>
John et al
The flash point of Aeroshell 31 is 83 degrees C. The flash point of
Aeroshell 41 is 254 degreees C. Take you pick. I seem to recall reading of
brake fires due to leaking brake fluid onto hot brakes.
I believe the cost difference is trival.
Cheers
Les
--
| - The Matronics RV10-List Email Forum - | | Use the List Feature Navigator to browse the many List utilities available such as the Email Subscriptions page, Archive Search & Download, 7-Day Browse, Chat, FAQ, Photoshare, and much more:
http://www.matronics.com/Navigator?RV10-List |
|
|
|
Back to top |
|
 |
AV8ORJWC
Joined: 13 Jul 2006 Posts: 1149 Location: Aurora, Oregon "Home of VANS"
|
Posted: Sun May 01, 2011 11:13 am Post subject: Flare Fitting Torque |
|
|
Milspec H-83282 is the improved product over H-5606 regardless of manufacturer name. Coming in hot on a short runway requires converting the energy to heat transferred into the rotors. Another improvement is increased rotor mass or larger surface area of calipers. You cannot go wrong increasing a safety margin regarding fire. Tim James went with improved mass and pad area.
John
From: owner-rv10-list-server(at)matronics.com [mailto:owner-rv10-list-server(at)matronics.com] On Behalf Of Kelly McMullen
Sent: Sunday, May 01, 2011 4:36 AM
To: rv10-list(at)matronics.com
Subject: Re: Re: Flare Fitting Torque
http://www.skygeek.com/royco-782-synthetic-fire-resistant-hydraulic-fluid.html
If you don't mind another brand, and don't want to have 3.5 qts unused for the life of your plane.
On Sat, Apr 30, 2011 at 12:13 PM, Les Kearney <kearney(at)shaw.ca (kearney(at)shaw.ca)> wrote:
--> RV10-List message posted by: "Les Kearney" <kearney(at)shaw.ca (kearney(at)shaw.ca)>
John et al
The flash point of Aeroshell 31 is 83 degrees C. The flash point of
Aeroshell 41 is 254 degreees C. Take you pick. I seem to recall reading of
brake fires due to leaking brake fluid onto hot brakes.
I believe the cost difference is trival.
Cheers
Les
--
| - The Matronics RV10-List Email Forum - | | Use the List Feature Navigator to browse the many List utilities available such as the Email Subscriptions page, Archive Search & Download, 7-Day Browse, Chat, FAQ, Photoshare, and much more:
http://www.matronics.com/Navigator?RV10-List |
|
|
|
Back to top |
|
 |
dlm34077(at)q.com Guest
|
Posted: Sun May 01, 2011 11:38 am Post subject: Flare Fitting Torque |
|
|
Several improvements can be made to stopping distances; Matco is developing a wheel/brake (dual puck) which can be used in lieu of the Cleveland mains; secondly making certain that the prop control is full forward will increase aerodynamic braking.
On a different note using Arial font and size 12 will increase the readability of the email; my main computer display is an HD TV screen, so I am sitting 6-8 feet from the screen. You last answer must have been about size 8 and faint. Thanks.
[quote] ---
| - The Matronics RV10-List Email Forum - | | Use the List Feature Navigator to browse the many List utilities available such as the Email Subscriptions page, Archive Search & Download, 7-Day Browse, Chat, FAQ, Photoshare, and much more:
http://www.matronics.com/Navigator?RV10-List |
|
|
|
Back to top |
|
 |
kearney
Joined: 20 Sep 2008 Posts: 563
|
Posted: Sun May 01, 2011 7:45 pm Post subject: Flare Fitting Torque |
|
|
Don
That was a test! You passed. The specs from Shell say that the fire point on the Aeroshell 31 is 254C so you only get part marks <vbg>.
Brett at Bonaco Inc does a wonderful job supplying high quality brake / fuel lines. I have eliminated the plastic lines in the Van's spec and have also used his hoses on the gear legs to the brakes.
All my fuel lines will be / are braided steel lines.
Cheers
Les
From: owner-rv10-list-server(at)matronics.com [mailto:owner-rv10-list-server(at)matronics.com] On Behalf Of Don McDonald
Sent: May-01-11 9:40 AM
To: rv10-list(at)matronics.com
Subject: Re: Re: Flare Fitting Torque
Les, I think you got it backwards... Aeroshell 31 is 205C, and 41 is 90C.
Don McDonald
From: Les Kearney <kearney(at)shaw.ca>
To: rv10-list(at)matronics.com
Sent: Sat, April 30, 2011 11:13:07 AM
Subject: RE: Re: Flare Fitting Torque
--> RV10-List message posted by: "Les Kearney" <kearney(at)shaw.ca (kearney(at)shaw.ca)>
John et al
The flash point of Aeroshell 31 is 83 degrees C. The flash point of
Aeroshell 41 is 254 degreees C. Take you pick. I seem to recall reading of
brake fires due to leaking brake fluid onto hot brakes.
I believe the cost difference is trival.
Cheers
Les
-----Original Message-----
From: owner-rv10-list-server(at)matronics.com (owner-rv10-list-server(at)matronics.com)
[mailto:owner-rv10-list-server(at)matronics.com (owner-rv10-list-server(at)matronics.com)] On Behalf Of John Cox
Sent: April-29-11 11:59 PM
To: rv10-list(at)matronics.com (rv10-list(at)matronics.com)
Subject: RE: Re: Flare Fitting Torque
--> RV10-List message posted by: "John Cox" <johnwcox(at)pacificnw.com (johnwcox(at)pacificnw.com)>
Improved product quality helps in the overall build. Getting rid of
H-5606 and upgrading hydraulic fluid is another Manufacturer decision.
Great call Wayne.
John
--
| - The Matronics RV10-List Email Forum - | | Use the List Feature Navigator to browse the many List utilities available such as the Email Subscriptions page, Archive Search & Download, 7-Day Browse, Chat, FAQ, Photoshare, and much more:
http://www.matronics.com/Navigator?RV10-List |
|
|
|
Back to top |
|
 |
|
|
You cannot post new topics in this forum You cannot reply to topics in this forum You cannot edit your posts in this forum You cannot delete your posts in this forum You cannot vote in polls in this forum You cannot attach files in this forum You can download files in this forum
|
Powered by phpBB © 2001, 2005 phpBB Group
|