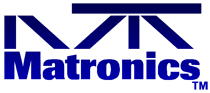 |
Matronics Email Lists Web Forum Interface to the Matronics Email Lists
|
View previous topic :: View next topic |
Author |
Message |
loboflyer(at)gmail.com Guest
|
Posted: Fri Aug 26, 2011 7:26 pm Post subject: RV-6A load analysis/architecture |
|
|
'Lectric Listers,
We're re-doing the entire panel on a flying RV-6A, replacing the vacuum gauges with GRT, going with dual Lightspeed ignitions, solving noise problems, cleaning up wire routing, and generally bringing it up to "Aeroelectric" best practices. The aircraft belongs to my father-in-law, who bought it flying from the original builder. I am the sucker, I mean electrical engineer, who volunteered to do all the design work. Being an EE means I tend to over-analyze things, so if you all think I'm being too concerned here or there, feel free to tell me so.
With that in mind, I would appreciate feedback on the load analysis and architecture selection. I have attached a .pdf of the latest rendition. Items highlighted in yellow are total guesses -- if anyone knows better numbers, by all means speak up. Items in bold/italic are items that will remain powered via e-bus if the primary alternator fails. If anyone would like a copy of the original spreadsheet, e-mail me off-list and I'll send it to you.
Mission: Day/Night VFR, future IFR when pilots appropriately rated (we're both private, non-instrument rated).
We will include the SD-8 alternator, and use dual displays (GRT HX and HS) with dual AHRS for redundancy.
Architecture: I am recommending Z-10/8 to avoid rebooting the displays upon startup. It adds a contactor, but my FIL requested that the displays remain up during cranking.
Is there anything missing from the analysis?
Have I chosen appropriate flight phases and loads?
The flight current loads seem smaller than I was expecting, since I've heard people clamoring for 60+ amp alternators. The current main alternator is a special case, so I'll reserve discussion for a separate e-mail post.
____________
-Jeff-
Albuquerque, NM
| - The Matronics AeroElectric-List Email Forum - | | Use the List Feature Navigator to browse the many List utilities available such as the Email Subscriptions page, Archive Search & Download, 7-Day Browse, Chat, FAQ, Photoshare, and much more:
http://www.matronics.com/Navigator?AeroElectric-List |
|
Description: |
|
 Download |
Filename: |
load_analysis.pdf |
Filesize: |
77.96 KB |
Downloaded: |
2399 Time(s) |
|
|
Back to top |
|
 |
sprocket(at)vx-aviation.c Guest
|
Posted: Sat Aug 27, 2011 8:07 am Post subject: RV-6A load analysis/architecture |
|
|
Your analysis is the right way to approach this.
Some additions:
-battery charging current (peaks after start-up)
-alternator field current (if you have an external regulator)
But here’s the big issue: Sometimes maximum loads are experienced with the engine at low rpm (taxiing, approach). This stresses the alternator more. Not a problem for short durations (that’s what the battery is for), but it can overheat the alternator (low rpm, low airflow, high load). My personal opinion is that a larger capacity alternator will be less stressed than one that is just ‘adequate’.
Your analysis shows that a 35A alternator would probably be adequate (even allowing for charging and alt field current), but I would recommend one with higher capacity. I’ve fried a 35A on the ground with just a 15A load during taxi and a 80F OAT. My next plane will have a 60A alternator. Also, pay attention to alternator diode cooling—mine had been melted right off, even with a blast tube. In fact, if you have a spare thermometer input, epoxy a sensor to the alternator diode pack. You may be surprised.
V
From: Jeff B. (loboflyer(at)gmail.com)
Sent: Friday, August 26, 2011 8:22 PM
To: aeroelectric-list(at)matronics.com (aeroelectric-list(at)matronics.com)
Subject: RV-6A load analysis/architecture
'Lectric Listers,
We're re-doing the entire panel on a flying RV-6A, replacing the vacuum gauges with GRT, going with dual Lightspeed ignitions, solving noise problems, cleaning up wire routing, and generally bringing it up to "Aeroelectric" best practices. The aircraft belongs to my father-in-law, who bought it flying from the original builder. I am the sucker, I mean electrical engineer, who volunteered to do all the design work. Being an EE means I tend to over-analyze things, so if you all think I'm being too concerned here or there, feel free to tell me so.
With that in mind, I would appreciate feedback on the load analysis and architecture selection. I have attached a .pdf of the latest rendition. Items highlighted in yellow are total guesses -- if anyone knows better numbers, by all means speak up. Items in bold/italic are items that will remain powered via e-bus if the primary alternator fails. If anyone would like a copy of the original spreadsheet, e-mail me off-list and I'll send it to you.
Mission: Day/Night VFR, future IFR when pilots appropriately rated (we're both private, non-instrument rated).
We will include the SD-8 alternator, and use dual displays (GRT HX and HS) with dual AHRS for redundancy.
Architecture: I am recommending Z-10/8 to avoid rebooting the displays upon startup. It adds a contactor, but my FIL requested that the displays remain up during cranking.
Is there anything missing from the analysis?
Have I chosen appropriate flight phases and loads?
The flight current loads seem smaller than I was expecting, since I've heard people clamoring for 60+ amp alternators. The current main alternator is a special case, so I'll reserve discussion for a separate e-mail post.
____________
-Jeff-
Albuquerque, NM
No virus found in this message.
Checked by AVG - www.avg.com
Version: 10.0.1392 / Virus Database: 1520/3860 - Release Date: 08/26/11
[quote][b]
| - The Matronics AeroElectric-List Email Forum - | | Use the List Feature Navigator to browse the many List utilities available such as the Email Subscriptions page, Archive Search & Download, 7-Day Browse, Chat, FAQ, Photoshare, and much more:
http://www.matronics.com/Navigator?AeroElectric-List |
|
|
|
Back to top |
|
 |
klehman(at)albedo.net Guest
|
Posted: Sat Aug 27, 2011 11:22 am Post subject: RV-6A load analysis/architecture |
|
|
I favour a small alternator for less energy and slower voltage rise if
it runs away, and of course for the lighter weight. With modern
internally regulated alternators I wonder if any have thermal
protection. Certainly lots of cheap discrete power ic's have integral
temperature protection. Anybody know if there is any temperature
protection in modern alternators? The ones I've had apart have separate
diode assemblies so perhaps not for the diodes.
Ken
On 8/27/2011 12:02 PM, Vern Little wrote:
Quote: | Your analysis is the right way to approach this.
Some additions:
-battery charging current (peaks after start-up)
-alternator field current (if you have an external regulator)
But here’s the big issue: Sometimes maximum loads are experienced with
the engine at low rpm (taxiing, approach). This stresses the alternator
more. Not a problem for short durations (that’s what the battery is
for), but it can overheat the alternator (low rpm, low airflow, high
load). My personal opinion is that a larger capacity alternator will be
less stressed than one that is just ‘adequate’.
Your analysis shows that a 35A alternator would probably be adequate
(even allowing for charging and alt field current), but I would
recommend one with higher capacity. I’ve fried a 35A on the ground with
just a 15A load during taxi and a 80F OAT. My next plane will have a 60A
alternator. Also, pay attention to alternator diode cooling—mine had
been melted right off, even with a blast tube. In fact, if you have a
spare thermometer input, epoxy a sensor to the alternator diode pack.
You may be surprised.
V
|
| - The Matronics AeroElectric-List Email Forum - | | Use the List Feature Navigator to browse the many List utilities available such as the Email Subscriptions page, Archive Search & Download, 7-Day Browse, Chat, FAQ, Photoshare, and much more:
http://www.matronics.com/Navigator?AeroElectric-List |
|
|
|
Back to top |
|
 |
loboflyer(at)gmail.com Guest
|
Posted: Sat Aug 27, 2011 9:07 pm Post subject: RV-6A load analysis/architecture |
|
|
Vern & Ken, thanks for the input. I figured 10A or so ought to cover charging, but after a cold day start that battery might be pretty taxed. I did forget to consider the lower RPM during taxi and such.
Alternator: here's where I don't understand the present installation.
The present installation has an "Overhauled lightweight 35 Amp alternator" from Mark Landoll's Electrical Service. It includes a Transpo F7078 external regulator. The sales documentation (attached) shows the regulator installed as attached to the alternator. But, the as-built has the regulator installed behind the instrument panel, separated from the alternator. The field line appears to be directly switched. The regulation signal, as stated by the Landoll data sheet as "the wye junction of the Ford stator is the source of the signal for the F7078 regulator. At 1200 RPM, the stator magnitude is only 35 mV." I'm not up to snuff on my motor/generator theory, so I can't visualize what is happening with this setup. This setup doesn't seem to match what I see in the Aeroelectric Connection. Is this an optimal way of doing things, or are there advantages to the ways that Bob describes vs. this Transpo setup? Will the split between alternator and regulator create unforeseen issues?
Even if we kept the alternator, I would change the panel mounted B-lead breaker protection to ANL style near the battery.
We might up the size of the alternator a bit and go with simple external regulation (generic Ford regulator or such). So, my questions about operation and potential for problems is mostly to satisfy my desire to learn.
Second question: We will have a crowbar circuit for OVP, but does anyone see a problem with relying on the GRT EIS4000 to supply the "low voltage" warning? The EIS has a low-RPM maskable low voltage alert.
-Jeff-
| - The Matronics AeroElectric-List Email Forum - | | Use the List Feature Navigator to browse the many List utilities available such as the Email Subscriptions page, Archive Search & Download, 7-Day Browse, Chat, FAQ, Photoshare, and much more:
http://www.matronics.com/Navigator?AeroElectric-List |
|
Description: |
|
 Download |
Filename: |
RV-6A_Landoll_Transpo_Alt_and_Diagram.pdf |
Filesize: |
171.79 KB |
Downloaded: |
619 Time(s) |
|
|
Back to top |
|
 |
sprocket(at)vx-aviation.c Guest
|
Posted: Sun Aug 28, 2011 9:41 am Post subject: RV-6A load analysis/architecture |
|
|
There is nothing fundamentally wrong with any of this. The recommendation to switch the output of the voltage regulator eliminates a lot of problems with switching the input/sense side of some regulators (Bob has a lot of documentation on this problem).
The Wye center point is just like the neutral in your house wiring... it should always be close to ground potential except when something bad happens. My guess is the regulator can sense this (similar to a ground fault detector). Not sure what it does when something goes wrong.
As for the crowbar... yes! It’s very simple and cheap insurance. Don’t depend on an audible warning. The OVP protection is much faster.
The only issue is keeping the alternator cool when loaded to full capacity at low airspeeds and taxiing. You should be fine if you pay attention to cooling, but there’s not a lot of margin. If you can, my suggestion of attaching a temperature probe to the alternator may help—program the GRT EIS to provide a warning when exceeding about 150C on the diodes so you can do some load shedding. This applies to any rating of alternator.
V
From: Jeff B. (loboflyer(at)gmail.com)
Sent: Saturday, August 27, 2011 10:03 PM
To: aeroelectric-list(at)matronics.com (aeroelectric-list(at)matronics.com)
Subject: Re: RV-6A load analysis/architecture
Vern & Ken, thanks for the input. I figured 10A or so ought to cover charging, but after a cold day start that battery might be pretty taxed. I did forget to consider the lower RPM during taxi and such.
Alternator: here's where I don't understand the present installation.
The present installation has an "Overhauled lightweight 35 Amp alternator" from Mark Landoll's Electrical Service. It includes a Transpo F7078 external regulator. The sales documentation (attached) shows the regulator installed as attached to the alternator. But, the as-built has the regulator installed behind the instrument panel, separated from the alternator. The field line appears to be directly switched. The regulation signal, as stated by the Landoll data sheet as "the wye junction of the Ford stator is the source of the signal for the F7078 regulator. At 1200 RPM, the stator magnitude is only 35 mV." I'm not up to snuff on my motor/generator theory, so I can't visualize what is happening with this setup. This setup doesn't seem to match what I see in the Aeroelectric Connection. Is this an optimal way of doing things, or are there advantages to the ways that Bob describes vs. this Transpo setup? Will the split between alternator and regulator create unforeseen issues?
Even if we kept the alternator, I would change the panel mounted B-lead breaker protection to ANL style near the battery.
We might up the size of the alternator a bit and go with simple external regulation (generic Ford regulator or such). So, my questions about operation and potential for problems is mostly to satisfy my desire to learn.
Second question: We will have a crowbar circuit for OVP, but does anyone see a problem with relying on the GRT EIS4000 to supply the "low voltage" warning? The EIS has a low-RPM maskable low voltage alert.
-Jeff-
No virus found in this message.
Checked by AVG - www.avg.com
Version: 10.0.1392 / Virus Database: 1520/3863 - Release Date: 08/28/11
[quote][b]
| - The Matronics AeroElectric-List Email Forum - | | Use the List Feature Navigator to browse the many List utilities available such as the Email Subscriptions page, Archive Search & Download, 7-Day Browse, Chat, FAQ, Photoshare, and much more:
http://www.matronics.com/Navigator?AeroElectric-List |
|
|
|
Back to top |
|
 |
nuckolls.bob(at)aeroelect Guest
|
Posted: Mon Aug 29, 2011 7:37 am Post subject: RV-6A load analysis/architecture |
|
|
At 12:03 AM 8/28/2011, you wrote:
Vern & Ken, thanks for the input. I figured 10A or so ought to cover
charging, but after a cold day start that battery might be pretty
taxed. I did forget to consider the lower RPM during taxi and such.
Most belt driven alternators on a Lyc are running
pretty fast . . . even at idle/taxi speeds. They'll
produce a considerable percentage of rated output.
Legacy alternator/generator sizing in TC aircraft
calls for retaining 25% of rated output for battery
charging. There's no particular driver for having
recharge take place before takeoff . . . only that
the battery be topped off in the first hour to 90
minutes of operation.
Alternator: here's where I don't understand the present installation.
The present installation has an "Overhauled lightweight 35 Amp
alternator" from Mark Landoll's Electrical Service. It includes a
Transpo F7078 external regulator. The sales documentation (attached)
shows the regulator installed as attached to the alternator. But,
the as-built has the regulator installed behind the instrument panel,
separated from the alternator. The field line appears to be directly
switched. The regulation signal, as stated by the Landoll data sheet
as "the wye junction of the Ford stator is the source of the signal
for the F7078 regulator. At 1200 RPM, the stator magnitude is only 35
mV." I'm not up to snuff on my motor/generator theory, so I can't
visualize what is happening with this setup. This setup doesn't seem
to match what I see in the Aeroelectric Connection. Is this an
optimal way of doing things, or are there advantages to the ways that
Bob describes vs. this Transpo setup? Will the split between
alternator and regulator create unforeseen issues?
This is a pretty 'old' example of alternator design
and implementation. The first alternators we installed
on Cessna aircraft had an "S" or stator terminal which
was a tap on the center of a 'wye wound' stator. This
was used to sense whether or not the engine was running
and operate a field disconnect relay.
http://aeroelectric.com/Pictures/Regulators/Legacy_EM_Regulator_(Ford).pdf
In automobiles, this feature disconnected the alternator
field supply when the engine wasn't running thus preventing
battery depletion in a parked car. Since airplanes had alternator
and battery switches, this feature was not needed. The field
relay was controlled directly through the battery/master switch.
Later, the solid state ov module was added in series
with the relay coil lead
http://aeroelectric.com/Pictures/Schematics/Cessna_OVModule.jpg
Even if we kept the alternator, I would change the panel mounted
B-lead breaker protection to ANL style near the battery.
That works.
We might up the size of the alternator a bit and go with simple
external regulation (generic Ford regulator or such). So, my
questions about operation and potential for problems is mostly to
satisfy my desire to learn.
That would be okay too. The Transpo regulator
is probably adequate to the task too but without
knowing more details on how it uses/needs the
'stator' connection, I can advise that going to
a generic 'Ford' regulator is a sure bed.
Second question: We will have a crowbar circuit for OVP, but does
anyone see a problem with relying on the GRT EIS4000 to supply the
"low voltage" warning? The EIS has a low-RPM maskable low voltage alert.
Yes, you want ov protection to be automatic and
FAST . . . MILLISECOND fast.
Bob . . .
| - The Matronics AeroElectric-List Email Forum - | | Use the List Feature Navigator to browse the many List utilities available such as the Email Subscriptions page, Archive Search & Download, 7-Day Browse, Chat, FAQ, Photoshare, and much more:
http://www.matronics.com/Navigator?AeroElectric-List |
|
|
|
Back to top |
|
 |
nuckolls.bob(at)aeroelect Guest
|
Posted: Mon Aug 29, 2011 7:46 am Post subject: RV-6A load analysis/architecture |
|
|
At 12:38 PM 8/28/2011, you wrote:
There is nothing fundamentally wrong with any of
this. The recommendation to switch the output of
the voltage regulator eliminates a lot of
problems with switching the input/sense side of
some regulators (Bob has a lot of documentation on this problem).
The Wye center point is just like the neutral in
your house wiring... it should always be close to
ground potential except when something bad
happens. My guess is the regulator can sense
this (similar to a ground fault detector). Not
sure what it does when something goes wrong.
Not exactly. The 'wye-center-tap' on an alternator
will output considerable current . . . at about
1/2 system voltage. It's used for (1) controlling
field supply disconnect relays in some designs
and/or (2) producing a residual output for getting
an alternator to self-excite. This terminal was often
labeled "N" on some alternators which led individuals to
believe that it was some sort of ground or low-side
supply.
As for the crowbar... yes! It’s very simple
and cheap insurance. Don’t depend on an
audible warning. The OVP protection is much faster.
The only issue is keeping the alternator cool
when loaded to full capacity at low airspeeds and
taxiing. You should be fine if you pay attention
to cooling, but there’s not a lot of
margin. If you can, my suggestion of attaching a
temperature probe to the alternator may
help—program thhe GRT EIS to provide a warning
when exceeding about 150C on the diodes so you
can do some load shedding. This applies to any rating of alternator.
The only alternators that get into cooling trouble
in flight are those not properly integrated into
the system on day-one. New installations on TC
aircraft are tested at max running load during
best angle of climb with data corrected for hot-
day conditions. This is how some alternators get
blast tubes and others do not. Alternator failure
due to overheating on an alternator bolted to the
front of a Lycoming is very rare and is traceable
to some poor choices.
If in doubt, do put a thermocouple on the diode
heat sink and slip another into the stator winding
for exploring the operation during the 40 hr flyoff.
But that's a lot of effort that's more likely to
be intellectually satisfying than practical.
Bob . . .
| - The Matronics AeroElectric-List Email Forum - | | Use the List Feature Navigator to browse the many List utilities available such as the Email Subscriptions page, Archive Search & Download, 7-Day Browse, Chat, FAQ, Photoshare, and much more:
http://www.matronics.com/Navigator?AeroElectric-List |
|
|
|
Back to top |
|
 |
loboflyer(at)gmail.com Guest
|
Posted: Tue Aug 30, 2011 8:14 pm Post subject: RV-6A load analysis/architecture |
|
|
On Mon, Aug 29, 2011 at 9:33 AM, Robert L. Nuckolls, III <nuckolls.bob(at)aeroelectric.com (nuckolls.bob(at)aeroelectric.com)> wrote:
Quote: | --> AeroElectric-List message posted by: "Robert L. Nuckolls, III" <nuckolls.bob(at)aeroelectric.com (nuckolls.bob(at)aeroelectric.com)>
Second question: We will have a crowbar circuit for OVP, but does anyone see a problem with relying on the GRT EIS4000 to supply the "low voltage" warning? The EIS has a low-RPM maskable low voltage alert.
Yes, you want ov protection to be automatic and
FAST . . . MILLISECOND fast.
|
Thank you, Bob, I am glad this list exists so that we can learn, craft fundamentally sound designs, and improve the status quo in aircraft electrical design!
Just a clarification: the OVP will be a standard crowbar circuit such as the OVM-14 or 9024. I was merely asking about the pilot indication of low voltage ("idiot light"), instead of using a canned module like the 9005 (or combination like the LR3C), if we chose to use the EIS4000 and its annunciator system, would there be any undesirable effects?
Regarding the Transpo F7078, were you suggesting it was a mechanical regulator, or did I read too much into the explanation?
-Jeff-
[quote][b]
| - The Matronics AeroElectric-List Email Forum - | | Use the List Feature Navigator to browse the many List utilities available such as the Email Subscriptions page, Archive Search & Download, 7-Day Browse, Chat, FAQ, Photoshare, and much more:
http://www.matronics.com/Navigator?AeroElectric-List |
|
|
|
Back to top |
|
 |
nuckolls.bob(at)aeroelect Guest
|
Posted: Wed Aug 31, 2011 5:42 am Post subject: RV-6A load analysis/architecture |
|
|
Quote: | Just a clarification: the OVP will be a standard crowbar circuit
such as the OVM-14 or 9024. I was merely asking about the pilot
indication of low voltage ("idiot light"), instead of using a canned
module like the 9005 (or combination like the LR3C), if we chose to
use the EIS4000 and its annunciator system, would there be any
undesirable effects?
|
Oh, I mis-uderstood. I've often been asked about
using a panel indication of overvoltage as incentive
for a pilot to turn the alternator off.
My preference for low voltage indication is a
sun-light viewable flashing light unique to that
task. If the EIS system has warning tones or
a particularly annoying display of an out-of-
bounds parameter, that would be a practical
alternative.
Quote: | Regarding the Transpo F7078, were you suggesting it was a mechanical
regulator, or did I read too much into the explanation?
|
No, it's a solid state device but that's all
I know about it. Transpo has been around for
a long time. They're now part of WAI Global.
http://www.wai-wetherill.com/
There's no reason to swap out the regulator
if you have sufficient information on how
to hook it up.
Bob . . .
| - The Matronics AeroElectric-List Email Forum - | | Use the List Feature Navigator to browse the many List utilities available such as the Email Subscriptions page, Archive Search & Download, 7-Day Browse, Chat, FAQ, Photoshare, and much more:
http://www.matronics.com/Navigator?AeroElectric-List |
|
|
|
Back to top |
|
 |
|
|
You cannot post new topics in this forum You cannot reply to topics in this forum You cannot edit your posts in this forum You cannot delete your posts in this forum You cannot vote in polls in this forum You cannot attach files in this forum You can download files in this forum
|
Powered by phpBB © 2001, 2005 phpBB Group
|