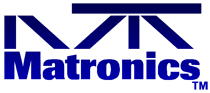 |
Matronics Email Lists Web Forum Interface to the Matronics Email Lists
|
View previous topic :: View next topic |
Author |
Message |
John Bickham
Joined: 10 Jan 2006 Posts: 170 Location: St. Francisville, LA
|
Posted: Wed May 24, 2006 1:01 pm Post subject: How I spent my MV vacation - worked on fuel tank |
|
|
Hello list,
Instead of driving to MV as I hoped, I stayed closer to home. Visited my daughter at Eglin AFB and worked my fuel tank.
Special thanks to John & Brother Jim Hauck. This is pretty much their proven design and my attempt to benefit from their experience. Steven Green also had some great suggestions and was helpful.
The tank is made from 5052 - h32 .063" (1/16")Aluminum. Couldn't get any .050 around here without paying some really high freight charges. More than the cost of the sheet. Anyway, my chances of successful welds increase with the slightly thicker material.
I had a close friend that deals daily with an excellent fab shop brake the metal for me. He won't tell me how much it cost to cut and brake. He wanted to do this for me for the few favors and projects I helped him on. Kindness returned is a good feeling.
If you notice, there are only vertical seams and seams on the top. I haven't decided on the extent I will rivet. Each vertical seam can be welded on the inside and outside. May only use rivets to the attach the top to the long baffle down the center and then weld over them.
Thought some may find pictures useful - always a lot of discussion on tanks. There are easier ways to do this. I struggled to make the baffles fit with a hand made brake. After I bent the last one, the light went off! If the baffles were made in three pieces - 1) baffle wall, 2) bottom angle, 3) top angle - the pieces could be clamped in place and then riveted together to get the perfect fit. ARGHHH!
Next, run some practice beads to get my rythym going good. Then clean and weld. Install filler neck, high vent and low outlet fittings.
Hope to be running with the big dogs soon. Just a lot of little steps to go.
Please be safe. Make good decisions early. Keep the dominoes far apart. Voice of experience. It can cost so much when they start to fall.
If you want to view my web page for some of my other challenges:
http://home.bellsouth.net/p/s/community.dll?ep=16&ext=1&groupid=291568&ck=
Hope this comes out OK. Not much experience with new format.
| - The Matronics Kolb-List Email Forum - | | Use the List Feature Navigator to browse the many List utilities available such as the Email Subscriptions page, Archive Search & Download, 7-Day Browse, Chat, FAQ, Photoshare, and much more:
http://www.matronics.com/Navigator?Kolb-List |
|
Description: |
|
Filesize: |
1008.33 KB |
Viewed: |
315 Time(s) |
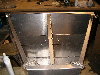
|
Description: |
|
Filesize: |
946.41 KB |
Viewed: |
275 Time(s) |
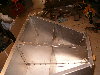
|
Description: |
This is how came from fab shop. Had to make last bend by hand. |
|
Filesize: |
902.51 KB |
Viewed: |
298 Time(s) |
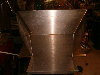
|
Description: |
Drawing with dimensions (inches) |
|
 Download |
Filename: |
fuel tank drawing.pdf |
Filesize: |
84.1 KB |
Downloaded: |
234 Time(s) |
_________________ Thanks too much,
John Bickham
Mark III-C w/ 912UL
St. Francisville, LA
I know many pilots and a few true aviators. There is a distinct difference that I have the greatest respect for. |
|
Back to top |
|
 |
DAquaNut(at)aol.com Guest
|
Posted: Thu May 25, 2006 3:36 pm Post subject: How I spent my MV vacation - worked on fuel tank |
|
|
In a message dated 5/24/2006 4:04:47 P.M. Central Standard Time,
gearbender(at)bellsouth.net writes:
If you notice, there are only vertical seams and seams on the top. I
haven't decided on the extent I will rivet. Each vertical seam can be welded on
the inside and outside. May only use rivets to the attach the top to the long
baffle down the center and then weld over them.
John,
If you drill some 3/8" -- 1/2 ' holes in the top skin you can plug weld
them to the center baffle. This would be stronger than trying to rivet the top
to the baffle. Also if you dont get the steel mandrel out of the pop rivet
you will introduce steel into your aluminum weld ,when you try to weld over it
,which is not a good thing. The industry standard for fitting up an aluminum
gas tank is a corner to corner weld, which, when welded with the proper
heat,using the tig method will leave a uniform penetration which will look like
it has a bead on the inside. Good luck.
Ed Diebel
Do Not Archieve
| - The Matronics Kolb-List Email Forum - | | Use the List Feature Navigator to browse the many List utilities available such as the Email Subscriptions page, Archive Search & Download, 7-Day Browse, Chat, FAQ, Photoshare, and much more:
http://www.matronics.com/Navigator?Kolb-List |
|
|
|
Back to top |
|
 |
John Bickham
Joined: 10 Jan 2006 Posts: 170 Location: St. Francisville, LA
|
Posted: Thu May 25, 2006 4:20 pm Post subject: Re: How I spent my MV vacation - worked on fuel tank |
|
|
Hey Ed,
I was going to use aluminum rivets with aluminum mandrels (5052) and weld over these. I could see your suggestion working also. Do you think the hole has to be 3/8" - 1/2". Seems like a 1/4" would work. I know several people have had success with weld over aluminum rivets method. I can see that if the rivet fails or pulls through the two pieces would seperate. The head of the rivet is only fused to the top plate.
More to ponder.
| - The Matronics Kolb-List Email Forum - | | Use the List Feature Navigator to browse the many List utilities available such as the Email Subscriptions page, Archive Search & Download, 7-Day Browse, Chat, FAQ, Photoshare, and much more:
http://www.matronics.com/Navigator?Kolb-List |
|
_________________ Thanks too much,
John Bickham
Mark III-C w/ 912UL
St. Francisville, LA
I know many pilots and a few true aviators. There is a distinct difference that I have the greatest respect for. |
|
Back to top |
|
 |
DAquaNut(at)aol.com Guest
|
Posted: Thu May 25, 2006 6:57 pm Post subject: How I spent my MV vacation - worked on fuel tank |
|
|
In a message dated 5/25/2006 7:22:26 P.M. Central Standard Time,
gearbender(at)bellsouth.net writes:
Hey Ed,
I was going to use aluminum rivets with aluminum mandrels (5052) and weld
over these. I could see your suggestion working also. Do you think the hole
has to be 3/8" - 1/2". Seems like a 1/4" would work. I know several people
have had success with weld over aluminum rivets method. I can see that if
the rivet fails or pulls through the two pieces would seperate. The head of
the rivet is only fused to the top plate.
More to ponder.
John,
You might be able to get by with a 1/4 " hole, but I think it is easier
if you have the hole big enough that you can get your tungsten in close enough
to the baffle ,that you can concentrate the heat on it so it burns into it
before the upper skin starts to melt, and you fill op the hole before you burn
into the baffle. I suggest a mock up trial run . Be sure you have a
method to clamp the upper skin down in the vicinity of the hole you are welding.
Chances are the upper skin will want to pull away from the baffle. If you do
not burn into the baffle when you fill the hole, the tank will not leak, but
the baffle will not be secure.
I dont know if you remember me but I met you at the Allen Parrish
Fly-in about 3 years ago. Good luck! Let me know how it goes.
Ed Diebel ( Houston) Do Not Archieve
| - The Matronics Kolb-List Email Forum - | | Use the List Feature Navigator to browse the many List utilities available such as the Email Subscriptions page, Archive Search & Download, 7-Day Browse, Chat, FAQ, Photoshare, and much more:
http://www.matronics.com/Navigator?Kolb-List |
|
|
|
Back to top |
|
 |
|
|
You cannot post new topics in this forum You cannot reply to topics in this forum You cannot edit your posts in this forum You cannot delete your posts in this forum You cannot vote in polls in this forum You cannot attach files in this forum You can download files in this forum
|
Powered by phpBB © 2001, 2005 phpBB Group
|