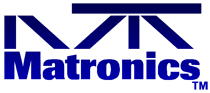 |
Matronics Email Lists Web Forum Interface to the Matronics Email Lists
|
View previous topic :: View next topic |
Author |
Message |
jamesgrieco(at)yahoo.com Guest
|
Posted: Sat Jan 28, 2012 5:53 am Post subject: Aileron mass balance |
|
|
I think there is a misconception about the weight. Its specific job is as a mass balance about the hinge line. If you draw a free body diagram of the aileron with the weight and a chord wise cut of the aileron, the two masses balance around the hinge bracket. When you apply a vertical gust, the inertia load on both sides of the hinge is the same, and in the same direction, so the hinge bracket gets wacked with combined load of the aileron mass + the counter weight mass X the vertical gust factor. This means the aileron wouldn't rotate, but there would be a large bending moment at the junction of the weight to tube welded joint. With rust and continuous fatigue loading it could break. Since no aileron rotation occurs, the rod would not hit the stop.
An estimate of the Max load and rod stress seen can be found by determining the ultimate capability of the hinge bracket. Since I gather it did not fail, the bending moment applied to the rod would be 1/2 the bracket ultimate load capability X the length of the rod to the CG of the mass. The gust factor would be 1/2 the bracket ultimate load divided by the weight of the counter weight up to the weld.
| - The Matronics TeamGrumman-List Email Forum - | | Use the List Feature Navigator to browse the many List utilities available such as the Email Subscriptions page, Archive Search & Download, 7-Day Browse, Chat, FAQ, Photoshare, and much more:
http://www.matronics.com/Navigator?TeamGrumman-List |
|
|
|
Back to top |
|
 |
Discover
Joined: 26 Feb 2007 Posts: 429
|
Posted: Sat Jan 28, 2012 7:09 am Post subject: Aileron mass balance |
|
|
Very good engineering analysis. Reminds me of the core classes back in college days. It is consistent with what the pilot reported as well. Didn't the report also say that BOTH counterweights departed the aircraft?
Ned
Sent from my iPad
On Jan 28, 2012, at 7:50 AM, James Grieco <jamesgrieco(at)yahoo.com> wrote:
Quote: |
I think there is a misconception about the weight. Its specific job is as a mass balance about the hinge line. If you draw a free body diagram of the aileron with the weight and a chord wise cut of the aileron, the two masses balance around the hinge bracket. When you apply a vertical gust, the inertia load on both sides of the hinge is the same, and in the same direction, so the hinge bracket gets wacked with combined load of the aileron mass + the counter weight mass X the vertical gust factor. This means the aileron wouldn't rotate, but there would be a large bending moment at the junction of the weight to tube welded joint. With rust and continuous fatigue loading it could break. Since no aileron rotation occurs, the rod would not hit the stop.
An estimate of the Max load and rod stress seen can be found by determining the ultimate capability of the hinge bracket. Since I gather it did not fail, the bending moment applied to the rod would be 1/2 the bracket ultimate load capability X the length of the rod to the CG of the mass. The gust factor would be 1/2 the bracket ultimate load divided by the weight of the counter weight up to the weld.
|
| - The Matronics TeamGrumman-List Email Forum - | | Use the List Feature Navigator to browse the many List utilities available such as the Email Subscriptions page, Archive Search & Download, 7-Day Browse, Chat, FAQ, Photoshare, and much more:
http://www.matronics.com/Navigator?TeamGrumman-List |
|
|
|
Back to top |
|
 |
teamgrumman(at)yahoo.com Guest
|
Posted: Sat Jan 28, 2012 7:11 pm Post subject: Aileron mass balance |
|
|
OK, but, to get the weight into the slipstream far enough to get dragged on, it has to move past the stop. Otherwise, there would be a lot of torn off weights.
From: James Grieco <jamesgrieco(at)yahoo.com>
To: TeamGrumman <teamgrumman-list(at)matronics.com>
Sent: Saturday, January 28, 2012 5:50 AM
Subject: Aileron mass balance
--> TeamGrumman-List message posted by: James Grieco <jamesgrieco(at)yahoo.com (jamesgrieco(at)yahoo.com)>
I think there is a misconception about the weight. Its specific job is as a mass balance about the hinge line. If you draw a free body diagram of the aileron with the weight and a chord wise cut of the aileron, the two masses balance around the hinge bracket. When you apply a vertical gust, the inertia load on both sides of the hinge is the same, and in the same direction, so the hinge bracket gets wacked with combined load of the aileron mass + the counter weight mass X the vertical gust factor. This means the aileron wouldn't rotate, but there would be a large bending moment at the junction of the weight to tube welded joint. With rust and continuous fatigue loading it could break. Since no aileron rotation occurs, the rod would not hit the stop.
An estimate of the Max load and rod stress seen can be found by determining the ultimate capability of the hinge bracket. Since I gather it did not fail, the bending moment applied to the rod would be 1/2 the bracket ultimate load capability X the length of the rod to the CG of the mass. The gust factor would be 1/2 the bracket ultimate load divided by the weight of the counter weight upamGrumman-List" target="_blank">http://www.matronics.com/Navigator?TeamGrumman-List<========================
| - The Matronics TeamGrumman-List Email Forum - | | Use the List Feature Navigator to browse the many List utilities available such as the Email Subscriptions page, Archive Search & Download, 7-Day Browse, Chat, FAQ, Photoshare, and much more:
http://www.matronics.com/Navigator?TeamGrumman-List |
|
|
|
Back to top |
|
 |
teamgrumman(at)yahoo.com Guest
|
Posted: Sat Jan 28, 2012 10:57 pm Post subject: Aileron mass balance |
|
|
I appreciate the lessons in strength of materials and statics, but it's more than just a missing counterweight. I wish I'd taken pics. The end of the torque tube was sheared at the aileron bearing bracket. That degree of force has to be transferred to the aileron stop, if and only if, the bolt that does the stopping is still there.
Gary
Sent from my iPad
On Jan 28, 2012, at 7:08 PM, Gary Vogt <teamgrumman(at)yahoo.com (teamgrumman(at)yahoo.com)> wrote:
[quote]OK, but, to get the weight into the slipstream far enough to get dragged on, it has to move past the stop. Otherwise, there would be a lot of torn off weights.
From: James Grieco <jamesgrieco(at)yahoo.com (jamesgrieco(at)yahoo.com)>
To: TeamGrumman <teamgrumman-list(at)matronics.com (teamgrumman-list(at)matronics.com)>
Sent: Saturday, January 28, 2012 5:50 AM
Subject: TeamGrumman-List: Aileron mass balance
--> TeamGrumman-List message posted by: James Grieco <jamesgrieco(at)yahoo.com (jamesgrieco(at)yahoo.com)>
I think there is a misconception about the weight. Its specific job is as a mass balance about the hinge line. If you draw a free body diagram of the aileron with the weight and a chord wise cut of the aileron, the two masses balance around the hinge bracket. When you apply a vertical gust, the inertia load on both sides of the hinge is the same, and in the same direction, so the hinge bracket gets wacked with combined load of the aileron mass + the counter weight mass X the vertical gust factor. This means the aileron wouldn't rotate, but there would be a large bending moment at the junction of the weight to tube welded joint. With rust and continuous fatigue loading it could break. Since no aileron rotation occurs, the rod would not hit the stop.
An estimate of the Max load and rod stress seen can be found by determining the ultimate capability of the hinge bracket. Since I gather it did not fail, the bending moment applied to the rod would be 1/2 the bracket ultimate load capability X the length of the rod to the CG of the mass. The gust factor would be 1/2 the bracket ultimate load divided by the weight of the counter weight upamGrumman-List" target="_blank">http://www.matronics.com/Navigator?TeamGrumman-List<========================
Quote: |
===================================
t">http://www.matronics.com/Navigator?TeamGrumman-List
===================================
cs.com
===================================
matronics.com/contribution
===================================
|
[b]
| - The Matronics TeamGrumman-List Email Forum - | | Use the List Feature Navigator to browse the many List utilities available such as the Email Subscriptions page, Archive Search & Download, 7-Day Browse, Chat, FAQ, Photoshare, and much more:
http://www.matronics.com/Navigator?TeamGrumman-List |
|
|
|
Back to top |
|
 |
jamesgrieco(at)yahoo.com Guest
|
Posted: Sun Jan 29, 2012 7:29 am Post subject: Aileron mass balance |
|
|
I would like to have seen those pics. I did not catch the beginning of the story. Did this AC crash? As I envision what you describe, it sounds like the aluminum torque tube failed, not the welded steel? The moments would still balance around the hinge line, so I don't think it would necessarily hit the stop.
| - The Matronics TeamGrumman-List Email Forum - | | Use the List Feature Navigator to browse the many List utilities available such as the Email Subscriptions page, Archive Search & Download, 7-Day Browse, Chat, FAQ, Photoshare, and much more:
http://www.matronics.com/Navigator?TeamGrumman-List |
|
|
|
Back to top |
|
 |
BARRY CHECK 6
Joined: 15 Mar 2011 Posts: 738
|
Posted: Sun Jan 29, 2012 8:46 am Post subject: Aileron mass balance |
|
|
Gary:
Pictures would have added a lot to the FMA.
You mentioned that the torque tube was sheared? Not crushed or deformed.
Two thoughts come to mind:
1 - Where was the shear, was it inline with the torque tube bracket? As if the bushing was cut through by friction and the friction was all around the torque tube diameter?
2 - Was the bushing still there and if so, in what condition?
It is extremely difficult to shear a tubular object. I have never seen it done without deforming the tube shape. It would be very easy to consider the tube being worn through and the bushing missing. You can shear an 'I' beam but not a tube.
My money would be on a highly worn or missing bushing. And then the question becomes: Wasn't this ever checked during Annual?
Barry
On Sun, Jan 29, 2012 at 1:53 AM, Gary L Vogt <teamgrumman(at)yahoo.com (teamgrumman(at)yahoo.com)> wrote:
[quote]I appreciate the lessons in strength of materials and statics, but it's more than just a missing counterweight. I wish I'd taken pics. The end of the torque tube was sheared at the aileron bearing bracket. That degree of force has to be transferred to the aileron stop, if and only if, the bolt that does the stopping is still there.
Gary
Sent from my iPad
On Jan 28, 2012, at 7:08 PM, Gary Vogt <teamgrumman(at)yahoo.com (teamgrumman(at)yahoo.com)> wrote:
Quote: | OK, but, to get the weight into the slipstream far enough to get dragged on, it has to move past the stop. Otherwise, there would be a lot of torn off weights.
From: James Grieco <jamesgrieco(at)yahoo.com (jamesgrieco(at)yahoo.com)>
To: TeamGrumman <teamgrumman-list(at)matronics.com (teamgrumman-list(at)matronics.com)>
Sent: Saturday, January 28, 2012 5:50 AM
Subject: TeamGrumman-List: Aileron mass balance
--> TeamGrumman-List message posted by: James Grieco <jamesgrieco(at)yahoo.com (jamesgrieco(at)yahoo.com)>
I think there is a misconception about the weight. Its specific job is as a mass balance about the hinge line. If you draw a free body diagram of the aileron with the weight and a chord wise cut of the aileron, the two masses balance around the hinge bracket. When you apply a vertical gust, the inertia load on both sides of the hinge is the same, and in the same direction, so the hinge bracket gets wacked with combined load of the aileron mass + the counter weight mass X the vertical gust factor. This means the aileron wouldn't rotate, but there would be a large bending moment at the junction of the weight to tube welded joint. With rust and continuous fatigue loading it could break. Since no aileron rotation occurs, the rod would not hit the stop.
An estimate of the Max load and rod stress seen can be found by determining the ultimate capability of the hinge bracket. Since I gather it did not fail, the bending moment applied to the rod would be 1/2 the bracket ultimate load capability X the length of the rod to the CG of the mass. The gust factor would be 1/2 the bracket ultimate load divided by the weight of the counter weight upamGrumman-List" target="_blank">http://www.matronics.com/Navigator?TeamGrumman-List<========================
|
[b]
| - The Matronics TeamGrumman-List Email Forum - | | Use the List Feature Navigator to browse the many List utilities available such as the Email Subscriptions page, Archive Search & Download, 7-Day Browse, Chat, FAQ, Photoshare, and much more:
http://www.matronics.com/Navigator?TeamGrumman-List |
|
|
|
Back to top |
|
 |
teamgrumman(at)yahoo.com Guest
|
Posted: Sun Jan 29, 2012 10:57 am Post subject: Aileron mass balance |
|
|
Go out to your plane and move the aileron up and down. The odds of anything tearing the counter weight off without touching the aileron stop would be near infinity. Had the bolt been there to hit the stop, when the pilot snapped the yoke back over to correct for the turbulence, he's have run out of aileron authority.
I got into some severe turbulence over Bakersfield . The plane was instantly snapped to 90 bank. It was all I could do to keep from going over. Correcting the bank with aileron was all I had.
I've done my share of inspections to say I've seen a far number of bent aileron stops. The bolts are there to stop the aileron from exceeding its designed limit.
From: James Grieco <jamesgrieco(at)yahoo.com>
To: teamgrumman-list(at)matronics.com
Sent: Sunday, January 29, 2012 7:27 AM
Subject: Aileron mass balance
--> TeamGrumman-List message posted by: James Grieco <jamesgrieco(at)yahoo.com (jamesgrieco(at)yahoo.com)>
I would like to have seen those pics. I did not catch the beginning of the story. Did this AC crash? As I envision what you describe, it sounds like the aluminum torque tube failed, not the welded steel? The moments would still balance around the hinge line, so I don't think it would necessarily hit the stop.
; --> http://www.matronics.com/Navigator?TeamGrumman-List<========================
| - The Matronics TeamGrumman-List Email Forum - | | Use the List Feature Navigator to browse the many List utilities available such as the Email Subscriptions page, Archive Search & Download, 7-Day Browse, Chat, FAQ, Photoshare, and much more:
http://www.matronics.com/Navigator?TeamGrumman-List |
|
|
|
Back to top |
|
 |
teamgrumman(at)yahoo.com Guest
|
Posted: Sun Jan 29, 2012 11:04 am Post subject: Aileron mass balance |
|
|
to be honest, I don't recall. All I know is that when I looked at the plane, the damage was like the NTSB says with the exception of the entire end of the torque tube gone. I was only there for about 20 minutes before there were FAA and NTSB people all over. No cell phone cameras then.
From: FLYaDIVE <flyadive(at)gmail.com>
To: teamgrumman-list(at)matronics.com
Sent: Sunday, January 29, 2012 8:43 AM
Subject: Re: Aileron mass balance
Gary:
Pictures would have added a lot to the FMA.
You mentioned that the torque tube was sheared? Not crushed or deformed.
Two thoughts come to mind:
1 - Where was the shear, was it inline with the torque tube bracket? As if the bushing was cut through by friction and the friction was all around the torque tube diameter?
2 - Was the bushing still there and if so, in what condition?
It is extremely difficult to shear a tubular object. I have never seen it done without deforming the tube shape. It would be very easy to consider the tube being worn through and the bushing missing. You can shear an 'I' beam but not a tube.
My money would be on a highly worn or missing bushing. And then the question becomes: Wasn't this ever checked during Annual?
Barry
On Sun, Jan 29, 2012 at 1:53 AM, Gary L Vogt <teamgrumman(at)yahoo.com (teamgrumman(at)yahoo.com)> wrote:
Quote: | I appreciate the lessons in strength of materials and statics, but it's more than just a missing counterweight. I wish I'd taken pics. The end of the torque tube was sheared at the aileron bearing bracket. That degree of force has to be transferred to the aileron stop, if and only if, the bolt that does the stopping is still there.
Gary
Sent from my iPad
On Jan 28, 2012, at 7:08 PM, Gary Vogt <teamgrumman(at)yahoo.com (teamgrumman(at)yahoo.com)> wrote:
Quote: | OK, but, to get the weight into the slipstream far enough to get dragged on, it has to move past the stop. Otherwise, there would be a lot of torn off weights.
From: James Grieco <jamesgrieco(at)yahoo.com (jamesgrieco(at)yahoo.com)>
To: TeamGrumman <teamgrumman-list(at)matronics.com (teamgrumman-list(at)matronics.com)>
Sent: Saturday, January 28, 2012 5:50 AM
Subject: Aileron mass balance
--> TeamGrumman-List message posted by: James Grieco <jamesgrieco(at)yahoo.com (jamesgrieco(at)yahoo.com)>
I think there is a misconception about the weight. Its specific job is as a mass balance about the hinge line. If you draw a free body diagram of the aileron with the weight and a chord wise cut of the aileron, the two masses balance around the hinge bracket. When you apply a vertical gust, the inertia load on both sides of the hinge is the same, and in the same direction, so the hinge bracket gets wacked with combined load of the aileron mass + the counter weight mass X the vertical gust factor. This means the aileron wouldn't rotate, but there would be a large bending moment at the junction of the weight to tube welded joint. With rust and continuous fatigue loading it could break. Since no aileron rotation occurs, the rod would not hit the stop.
An estimate of the Max load and rod stress seen can be found by determining the ultimate capability of the hinge bracket. Since I gather it did not fail, the bending moment applied to the rod would be 1/2 the bracket ultimate load capability X the length of the rod to the CG of the mass. The gust factor would be 1/2 the bracket ultimate load divided by the weight of the counter weight upamGrumman-List" target="_blank">http://www.matronics.com/Navigator?TeamGrumman-List<========================
|
-===================================
|
[quote][b]
| - The Matronics TeamGrumman-List Email Forum - | | Use the List Feature Navigator to browse the many List utilities available such as the Email Subscriptions page, Archive Search & Download, 7-Day Browse, Chat, FAQ, Photoshare, and much more:
http://www.matronics.com/Navigator?TeamGrumman-List |
|
|
|
Back to top |
|
 |
|
|
You cannot post new topics in this forum You cannot reply to topics in this forum You cannot edit your posts in this forum You cannot delete your posts in this forum You cannot vote in polls in this forum You cannot attach files in this forum You can download files in this forum
|
Powered by phpBB © 2001, 2005 phpBB Group
|