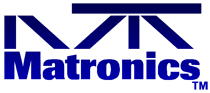 |
Matronics Email Lists Web Forum Interface to the Matronics Email Lists
|
View previous topic :: View next topic |
Author |
Message |
jkreidler
Joined: 13 Feb 2008 Posts: 151 Location: Sheboygan Falls WI
|
Posted: Sat Aug 25, 2012 7:58 am Post subject: Differential Pressure Test - Results Question |
|
|
We have been flying with the James cowl and plenum for a few years now. As some know we went through an extensive exercise in order to run the airplane near lean which was solved by adding the turbo injectors.
We really never had much of a cooling issue, but lately I think due to higher ambient temperatures we have had to limit extended climbs. So it is time to make some modifications to provide more margin. I found that there was a change to the inlet diameter of the James cowl. A quick e-mail to Will and he sent out larger inlet rings at no charge with apologies for having to install them.
So now what - we didn't want to install the rings without a good baseline of our current condition so we started on a path to gather data. I am disappointed in myself that I didn't collect this data during the whole turbo injector experiment.
We got a manometer that measured from -10" to +10" of water. We started by plumbing in four lines, first to the plenum chamber above the engine, second to the cowl chamber below the engine (near the sump), third to the pressurized injector manifold (which is air plumbed from the intake air box), fourth to the static pressure system.
Last night we gathered some readings during climb at 105kts then in cruise at 8000 PA and 4000 PA.
The values listed respectively were:
Plenum to Cowl: 2.5", 4", 4"
Injectors to Cowl: 7", 9.5", 10"
Plenum to Static: 4.5", 6.5", 7.5"
Injectors to Static: 9", >10", >10"
Cowl to Static: 2", 3", 3"
I know taking the values to the cowl and to static might have been redundant, but it is an experiment after all.
So now for my question, I am not sure what to make of the "Cowl to Static" reading. There was an article in the September 96 issue of Sport Aviation by Jimmy Tubs titled "Engine Cooling Problems" where he says "A significant pressure drop indicates that the bottom cowling is damming up the air causing lazy flow over the cylinders and oil cooler". So what does a significant pressure drop mean? We obviously do not have enough differential pressure over the cylinders, I have found numbers for the 320 and 360 and was told at one time that over 6" differential pressure is needed, but I want to attack the right end of the system. No point in opening up the inlet if the outlet may be to blame. The good news is I have the data, the bad news is I am struggling with the end interpretation of where to go.
By the way, the data gather absolutely proves that the turbo injector setup is more than doing its job! In fact I think it is safe to say the we're exceeding the pressure on the nozzles of the standard setup.
Thanks in advance - Jason
| - The Matronics RV10-List Email Forum - | | Use the List Feature Navigator to browse the many List utilities available such as the Email Subscriptions page, Archive Search & Download, 7-Day Browse, Chat, FAQ, Photoshare, and much more:
http://www.matronics.com/Navigator?RV10-List |
|
_________________ Jason Kreidler
4 Partner Build - Sheboygan Falls, WI
Tony Kolar, Kyle Hokel, Wayne Elser, Jason Kreidler
N44YH - Flying - #40617 |
|
Back to top |
|
 |
speckter(at)comcast.net Guest
|
Posted: Sat Aug 25, 2012 9:25 am Post subject: Differential Pressure Test - Results Question |
|
|
Now I am no expert on this stuff but this is how I read it. You have 2-3" of back pressure on the lower cowl. You need more exit area. This should increase the differential between the plenum and the lower cowl but I don't think it will quite be enough to solve all the problems. So I would increase the exit first and be prepared to also change out the inlet rings after you get more data.
Gary Specketer
From: "jkreidler" <jason.kreidler(at)regalbeloit.com>
To: rv10-list(at)matronics.com
Sent: Saturday, August 25, 2012 10:58:50 AM
Subject: Differential Pressure Test - Results Question
--> RV10-List message posted by: "jkreidler" <jason.kreidler(at)regalbeloit.com>
We have been flying with the James cowl and plenum for a few years now. Â As some know we went through an extensive exercise in order to run the airplane near lean which was solved by adding the turbo injectors.
We really never had much of a cooling issue, but lately I think due to higher ambient temperatures we have had to limit extended climbs. Â So it is time to make some modifications to provide more margin. Â I found that there was a change to the inlet diameter of the James cowl. Â A quick e-mail to Will and he sent out larger inlet rings at no charge with apologies for having to install them.
So now what - we didn't want to install the rings without a good baseline of our current condition so we started on a path to gather data. Â I am disappointed in myself that I didn't collect this data during the whole turbo injector experiment.
We got a manometer that measured from -10" to +10" of water. Â We started by plumbing in four lines, first to the plenum chamber above the engine, second to the cowl chamber below the engine (near the sump), third to the pressurized injector manifold (which is air plumbed from the intake air box), fourth to the static pressure system.
Last night we gathered some readings during climb at 105kts then in cruise at 8000 PA Â and 4000 PA.Â
The data listed respectively were:
Plenum to Cowl: 2.5", 4", 4"
Injectors to Cowl: 7", 9.5", 10"
Plenum to Static: 4.5", 6.5", 7.5"
Injectors to Static: 9", >10", >10"
Cowl to Static: 2", 3", 3"
I know taking the values to the cowl and to static might have been redundant, but it is an experiment after all.
So now for my question, I am not sure what to make of the "Cowl to Static" reading. Â There was an article in the September 96 issue of Sport Aviation by Jimmy Tubs titled "Engine Cooling Problems" where he says "A significant pressure drop indicates that the bottom cowling is damming up the air causing lazy flow over the cylinders and oil cooler". Â So what does a significant pressure drop mean? Â We obviously do not have enough differential pressure over the cylinders, I have found numbers for the 320 and 360 and was told at one time that over 6" differential pressure is needed, but I want to attack the right end of the system. Â No point in opening up the inlet if the outlet may be to blame. Â The good news is I have the data, the bad news is I am struggling with the end interpretation of where to go.
By the way, the data gather absolutely proves that the turbo injector setup is more than doing its job! �In fact I think it is safe to say the we're exceeding the pressure on the nozzles of the standard setup.
Thanks in advance - Jason
--------
Jason Kreidler
4 Partner Build - Sheboygan Falls, WI
Tony Kolar, Kyle Hokel, Wayne Elser, Jason Kreidler
N44YH - Flying - #40617
Read this topic online here:
http://forums.matronicsbsp; -Matt Dralle, List Adm=========
[quote][b]
| - The Matronics RV10-List Email Forum - | | Use the List Feature Navigator to browse the many List utilities available such as the Email Subscriptions page, Archive Search & Download, 7-Day Browse, Chat, FAQ, Photoshare, and much more:
http://www.matronics.com/Navigator?RV10-List |
|
|
|
Back to top |
|
 |
speckter(at)comcast.net Guest
|
Posted: Sat Aug 25, 2012 12:35 pm Post subject: Differential Pressure Test - Results Question |
|
|
I am convinced that those folks with piston cooling jets have higher oil temps than those without.
Deems, I think that your approach would work. You might have to play with the intake duct routing if you plan on staying with the standard Van's mounting for the cooler. Keep us posted.
Good luck on your recovery. The lesson here is fly more walk less!
Gary
From: "Deems Davis" <deemsdavis(at)cox.net>
To: rv10-list(at)matronics.com
Sent: Saturday, August 25, 2012 2:05:39 PM
Subject: Re: Differential Pressure Test - Results Question
Jason, I have the same configuration as you do and living in AZ each summer I go through the same drama of heat issues. For me it is manifest in oil temp and cyl tem of #6. I don't have the engineering bent that your team does. but after talking to and seeing Alan Bickle's beautiful plane and his data I'm convinced the root of the problem is that the intake rings are undersized for the -540. I've done everything I could think of to increase the exit area w/ louvers and trimming the aft portion of the lower cowl, with no improvement. If the problem is that not enough air is coming in no amount of increasing the outlet will happen. With all of that said I've been playing with an idea in my head that I want o experiment with, the basics of it is to take ram air into the oil cooler directly from an inlet on the underside of the cowl. block off the oil cooler air feed (at) #6, which should increase the pressure for the upper cowl with positive impact on #6 cyl temps). Duct the oil cooler exit air so that it transitions smoothly aft without adding to the the lower cowl pressure. I'm laid up following knee surgery for the next few weeks so I can't work on it. I was going to fashion the intake from fiberglass and use the gear leg slot cover/louver as the attachment, then attach the the hose feeding the oil cooler, and again some fiberglass for the oil cooler exit duct. The nice thing about this approach is that you don't have to hack up the cowl/plenum to do it, and it DOES increase the intake.
Deems
On Sat, Aug 25, 2012 at 8:58 AM, jkreidler <jason.kreidler(at)regalbeloit.com (jason.kreidler(at)regalbeloit.com)> wrote:
[quote]--> RV10-List message posted by: "jkreidler" <jason.kreidler(at)regalbeloit.com (jason.kreidler(at)regalbeloit.com)>
We have been flying with the James cowl and plenum for a few years now. Â As some know we went through an extensive exercise in order to run the airplane near lean which was solved by adding the turbo injectors.
We really never had much of a cooling issue, but lately I think due to higher ambient temperatures we have had to limit extended climbs. Â So it is time to make some modifications to provide more margin. Â I found that there was a change to the inlet diameter of the James cowl. Â A quick e-mail to Will and he sent out larger inlet rings at no charge with apologies for having to install them.
So now what - we didn't want to install the rings without a good baseline of our current condition so we started on a path to gather data. Â I am disappointed in myself that I didn't collect this data during the whole turbo injector experiment.
We got a manometer that measured from -10" to +10" of water. �We started by plumbing in four lines, first to the plenum chamber above the engine, second to the cowl chamber below the engine (near the sump), third to the pressurized injector manifold (which is air plumbed from the intake air box), fourth to the static pressure system.
Last night we gathered some readings during climb at 105kts then in cruise at 8000 PA Â and 4000 PA.Â
The data listed respectively were:
Plenum to Cowl: 2.5", 4", 4"
Injectors to Cowl: 7", 9.5", 10"
Plenum to Static: 4.5", 6.5", 7.5"
Injectors to Static: 9", >10", >10"
Cowl to Static: 2", 3", 3"
I know taking the values to the cowl and to static might have been redundant, but it is an experiment after all.
So now for my question, I am not sure what to make of the "Cowl to Static" reading.  There was an article in the September 96 issue of Sport Aviation by Jimmy Tubs titled "Engine Cooling Problems" where he says "A significant pressure drop indicates that the bottom cowling is damming up the air causing lazy flow over the cylinders and oil cooler". �So what does a significant pressure drop mean?  We obviously do not have enough differential pressure over the cylinders, I have found numbers for the 320 and 360 and was told at one time that over 6" differential pressure is needed, but I want to attack the right end of the system.  No point in opening up the inlet if the outlet may be to blame.  The good news is I have the data, the bad news is I am struggling with the end interpretation of where to go.
By the way, the data gather absolutely proves that the turbo injector setup is more than doing its job! Â In fact I think it is safe to say the we're exceeding the pressure on the nozzles of the standard setup.
Thanks in advance - Jason
--------
Jason Kreidler
4 Partner Build - Sheboygan Falls, WI
Tony Kolar, Kyle Hokel, Wayne Elser, Jason Kreidler
N44YH - Flying - #40617
Read this topic online here:
http://forums.matronics.com/viewtopic.php?p=381787#381787
===========
arget="_blank">http://www.matronics.com/Navigator?RV10-List
===========
http://forums.matronics.com
===========
le, List Admin.
="_blank">http://www.matronics.com/contribution
===========
get=_blank>http://www.matronics.com/Navigator?RV10-List
p://forums.matronics.com
blank>http://www.matronics.com/contribution
[b]
| - The Matronics RV10-List Email Forum - | | Use the List Feature Navigator to browse the many List utilities available such as the Email Subscriptions page, Archive Search & Download, 7-Day Browse, Chat, FAQ, Photoshare, and much more:
http://www.matronics.com/Navigator?RV10-List |
|
|
|
Back to top |
|
 |
jkreidler
Joined: 13 Feb 2008 Posts: 151 Location: Sheboygan Falls WI
|
Posted: Sat Aug 25, 2012 12:49 pm Post subject: Re: Differential Pressure Test - Results Question |
|
|
Deems, I wonder if just going to a larger air intake and splitting it so that part of it goes to the air box and the other to the oil cooler. Not sure if that is practical with you Rod Bower ram air or not. Just a quick thought... Good feedback on the lower cowl mods not helping, thanks.
Jason
| - The Matronics RV10-List Email Forum - | | Use the List Feature Navigator to browse the many List utilities available such as the Email Subscriptions page, Archive Search & Download, 7-Day Browse, Chat, FAQ, Photoshare, and much more:
http://www.matronics.com/Navigator?RV10-List |
|
_________________ Jason Kreidler
4 Partner Build - Sheboygan Falls, WI
Tony Kolar, Kyle Hokel, Wayne Elser, Jason Kreidler
N44YH - Flying - #40617 |
|
Back to top |
|
 |
Kellym
Joined: 10 Jan 2006 Posts: 1705 Location: Sun Lakes AZ
|
Posted: Sat Aug 25, 2012 1:02 pm Post subject: Differential Pressure Test - Results Question |
|
|
Well Deems, a friend had oil temp problems with his RV-7A. He built a
large NACA duct on the side of the cowling to feed the oil cooler. Doing
that made his oil temp more speed dependent...fine in cruise but too
high in climb and in the pattern. He went back to mounting it on the
baffling behind #4 of his IO-360, but putting it as high as he could get
it, and that seems to have mostly fixed the problem. External inlets
are trickey, because many have low pressure. Mooney had oil coolers on
lower face of their planes up until 1976, when they switched to putting
it behind left rear cylinder. The older planes with it on the cowl
suffer reverse flow in the climb and poor flow even in cruise because it
is a low pressure area. Those with cooler behind the engine do fine.
Getting bigger inlet will both raise pressure over the engine, it will
get more flow over the cooler.
On 8/25/2012 12:05 PM, Deems Davis wrote:
Quote: | Jason, I have the same configuration as you do and living in AZ each
summer I go through the same drama of heat issues. For me it is
manifest in oil temp and cyl tem of #6. I don't have the engineering
bent that your team does. but after talking to and seeing Alan
Bickle's beautiful plane and his data I'm convinced the root of the
problem is that the intake rings are undersized for the -540. I've
done everything I could think of to increase the exit area w/ louvers
and trimming the aft portion of the lower cowl, with no improvement.
If the problem is that not enough air is coming in no amount of
increasing the outlet will happen. With all of that said I've been
playing with an idea in my head that I want o experiment with, the
basics of it is to take ram air into the oil cooler directly from an
inlet on the underside of the cowl. block off the oil cooler air feed
(at) #6, which should increase the pressure for the upper cowl with
positive impact on #6 cyl temps). Duct the oil cooler exit air so that
it transitions smoothly aft without adding to the the lower cowl
pressure. I'm laid up following knee surgery for the next few weeks so
I can't work on it. I was going to fashion the intake from fiberglass
and use the gear leg slot cover/louver as the attachment, then attach
the the hose feeding the oil cooler, and again some fiberglass for the
oil cooler exit duct. The nice thing about this approach is that you
don't have to hack up the cowl/plenum to do it, and it DOES increase
the intake.
Deems
On Sat, Aug 25, 2012 at 8:58 AM, jkreidler
<jason.kreidler(at)regalbeloit.com
<mailto:jason.kreidler(at)regalbeloit.com>> wrote:
<jason.kreidler(at)regalbeloit.com
<mailto:jason.kreidler(at)regalbeloit.com>>
We have been flying with the James cowl and plenum for a few years
now. � As some know we went through an extensive exercise in order
to run the airplane near lean which was solved by adding the turbo
injectors.
We really never had much of a cooling issue, but lately I think
due to higher ambient temperatures we have had to limit extended
climbs. � So it is time to make some modifications to provide more
margin. � I found that there was a change to the inlet diameter of
the James cowl. � A quick e-mail to Will and he sent out larger
inlet rings at no charge with apologies for having to install them.
So now what - we didn't want to install the rings without a good
baseline of our current condition so we started on a path to
gather data. � I am disappointed in myself that I didn't collect
this data during the whole turbo injector experiment.
We got a manometer that measured from -10" to +10" of water. � We
started by plumbing in four lines, first to the plenum chamber
above the engine, second to the cowl chamber below the engine
(near the sump), third to the pressurized injector manifold (which
is air plumbed from the intake air box), fourth to the static
pressure system.
Last night we gathered some readings during climb at 105kts then
in cruise at 8000 PA � and 4000 PA.�
The data listed respectively were:
Plenum to Cowl: 2.5", 4", 4"
Injectors to Cowl: 7", 9.5", 10"
Plenum to Static: 4.5", 6.5", 7.5"
Injectors to Static: 9", >10", >10"
Cowl to Static: 2", 3", 3"
I know taking the values to the cowl and to static might have been
redundant, but it is an experiment after all.
So now for my question, I am not sure what to make of the "Cowl to
Static" reading. � There was an article in the September 96 issue
of Sport Aviation by Jimmy Tubs titled "Engine Cooling Problems"
where he says "A significant pressure drop indicates that the
bottom cowling is damming up the air causing lazy flow over the
cylinders and oil cooler". � So what does a significant pressure
drop mean? � We obviously do not have enough differential pressure
over the cylinders, I have found numbers for the 320 and 360 and
was told at one time that over 6" differential pressure is needed,
but I want to attack the right end of the system. � No point in
opening up the inlet if the outlet may be to blame. � The good
news is I have the data, the bad news is I am struggling with the
end interpretation of where to go.
By the way, the data gather absolutely proves that the turbo
injector setup is more than doing its job! � In fact I think it is
safe to say the we're exceeding the pressure on the nozzles of the
standard setup.
Thanks in advance - Jason
--------
Jason Kreidler
4 Partner Build - Sheboygan Falls, WI
Tony Kolar, Kyle Hokel, Wayne Elser, Jason Kreidler
N44YH - Flying - #40617
Read this topic online here:
http://forums.matronics.com/viewtopic.php?p=381787#381787
===========
arget="_blank">http://www.matronics.com/Navigator?RV10-List
===========
http://forums.matronics.com
===========
le, List Admin.
="_blank">http://www.matronics.com/contribution
===========
*
*
|
-----
No virus found in this message.
Checked by AVG - www.avg.com
| - The Matronics RV10-List Email Forum - | | Use the List Feature Navigator to browse the many List utilities available such as the Email Subscriptions page, Archive Search & Download, 7-Day Browse, Chat, FAQ, Photoshare, and much more:
http://www.matronics.com/Navigator?RV10-List |
|
_________________ Kelly McMullen
A&P/IA, EAA Tech Counselor # 5286
KCHD |
|
Back to top |
|
 |
robin(at)PaintTheWeb.com Guest
|
Posted: Sat Aug 25, 2012 1:49 pm Post subject: Differential Pressure Test - Results Question |
|
|
Gentleman,
As you know I have a similar set up James cowl / Plenum / 2008 Oil Cooler / Turbo Nozzles / Barrett FFCI. The difference is we have a dedicated opening on the lower cowl that feeds the 2008 oil cooler directly and gives me something like a DP of 14" across the oil cooler at speed. adding this was the single most beneficial item that helped my overall cooling situation. No amount of outlet opening came close to the dedicated oil cooler line. That being said getting the cooler to work at near max efficiency is nice but it's like getting a slightly larger bucket to put out a fire. You are better off trying to start with a smaller fire. You really need to address the cylinder temps and that will assist with the oil temps NOT the other way around.
One more thing about adding more high velocity air through the oil cooler is that tends to pressurize the lower cowl which I think is really working against your goal of having pressure move from High (upper cowl) to Low (lower cowl). I am afraid that you will go to all that work and see little benefit until you deal with the inlet opening.
After nearly 350 hours and lots of nursing ROP flights in So. Cal summers I have decided to "shitcan" the whole set up and start over. I have HATED the plenum for many reasons and found when I converted my 8A from Plenum to Baffle system I lost nothing in terms of performance and gained simplicity and easy access to the top deck of the engine which to me is added safety. The smart thing to do is revert to the Vans standard cowl since we have a fleet that has no issues (thanks Van!). But since it's me…. I have decided to be one of the first to install the Showplanes cowl and start a whole new experiment. The difference is the Showplanes cowl has a great deal of research & development behind it vs. the James Cowl which does not even mate up to the James Plenum. My bad for ever making that choice. This is a slightly easier choice since their test bed aircraft is a Barrett FF Cold Induction just like mine. I will be going from 4 holes in the front of my cowl to two holes which should be a huge improvement aerodynamically. I plan to start this project as soon as the 8A is out of paint around Mid-September. Hopefully I can report back before the new year. I am so familiar with my temp/performance numbers it will be simple to notice a difference.
Swapping out the cowl may seem extreme but the cost associated with all the R&D, fuel burn ROP especially during engine break in etc… I am sure is well over $10K to date and probably closer to $15K. Throw in the potential for reduced TBO and who knows… I am looking for a permenate solution once and for all. Unfortunately I know retrofitting the Vans cowl is the smartest option but I have never been accused of taking the easy road so why should today be any different.
For what it's worth I personally think the replacement inlet rings from James are still too small especially for pilots in generally warmer climates.
Robin
From: owner-rv10-list-server(at)matronics.com [mailto:owner-rv10-list-server(at)matronics.com] On Behalf Of Deems Davis
Sent: Saturday, August 25, 2012 12:06 PM
To: rv10-list(at)matronics.com
Subject: Re: Differential Pressure Test - Results Question
Jason, I have the same configuration as you do and living in AZ each summer I go through the same drama of heat issues. For me it is manifest in oil temp and cyl tem of #6. I don't have the engineering bent that your team does. but after talking to and seeing Alan Bickle's beautiful plane and his data I'm convinced the root of the problem is that the intake rings are undersized for the -540. I've done everything I could think of to increase the exit area w/ louvers and trimming the aft portion of the lower cowl, with no improvement. If the problem is that not enough air is coming in no amount of increasing the outlet will happen. With all of that said I've been playing with an idea in my head that I want o experiment with, the basics of it is to take ram air into the oil cooler directly from an inlet on the underside of the cowl. block off the oil cooler air feed (at) #6, which should increase the pressure for the upper cowl with positive impact on #6 cyl temps). Duct the oil cooler exit air so that it transitions smoothly aft without adding to the the lower cowl pressure. I'm laid up following knee surgery for the next few weeks so I can't work on it. I was going to fashion the intake from fiberglass and use the gear leg slot cover/louver as the attachment, then attach the the hose feeding the oil cooler, and again some fiberglass for the oil cooler exit duct. The nice thing about this approach is that you don't have to hack up the cowl/plenum to do it, and it DOES increase the intake.
Deems
On Sat, Aug 25, 2012 at 8:58 AM, jkreidler <jason.kreidler(at)regalbeloit.com (jason.kreidler(at)regalbeloit.com)> wrote:
--> RV10-List message posted by: "jkreidler" <jason.kreidler(at)regalbeloit.com (jason.kreidler(at)regalbeloit.com)>
We have been flying with the James cowl and plenum for a few years now. � As some know we went through an extensive exercise in order to run the airplane near lean which was solved by adding the turbo injectors.
We really never had much of a cooling issue, but lately I think due to higher ambient temperatures we have had to limit extended climbs. � So it is time to make some modifications to provide more margin. � I found that there was a change to the inlet diameter of the James cowl. � A quick e-mail to Will and he sent out larger inlet rings at no charge with apologies for having to install them.
So now what - we didn't want to install the rings without a good baseline of our current condition so we started on a path to gather data. � I am disappointed in myself that I didn't collect this data during the whole turbo injector experiment.
We got a manometer that measured from -10" to +10" of water. � We started by plumbing in four lines, first to the plenum chamber above the engine, second to the cowl chamber below the engine (near the sump), third to the pressurized injector manifold (which is air plumbed from the intake air box), fourth to the static pressure system.
Last night we gathered some readings during climb at 105kts then in cruise at 8000 PA � and 4000 PA.�
The data listed respectively were:
Plenum to Cowl: 2.5", 4", 4"
Injectors to Cowl: 7", 9.5", 10"
Plenum to Static: 4.5", 6.5", 7.5"
Injectors to Static: 9", >10", >10"
Cowl to Static: 2", 3", 3"
I know taking the values to the cowl and to static might have been redundant, but it is an experiment after all.
So now for my question, I am not sure what to make of the "Cowl to Static" reading. � There was an article in the September 96 issue of Sport Aviation by Jimmy Tubs titled "Engine Cooling Problems" where he says "A significant pressure drop indicates that the bottom cowling is damming up the air causing lazy flow over the cylinders and oil cooler". � So what does a significant pressure drop mean? � We obviously do not have enough differential pressure over the cylinders, I have found numbers for the 320 and 360 and was told at one time that over 6" differential pressure is needed, but I want to attack the right end of the system. � No point in opening up the inlet if the outlet may be to blame. � The good news is I have the data, the bad news is I am struggling with the end interpretation of where to go.
By the way, the data gather absolutely proves that the turbo injector setup is more than doing its job! � In fact I think it is safe to say the we're exceeding the pressure on the nozzles of the standard setup.
Thanks in advance - Jason
--------
Jason Kreidler
4 Partner Build - Sheboygan Falls, WI
Tony Kolar, Kyle Hokel, Wayne Elser, Jason Kreidler
N44YH - Flying - #40617
Read this topic online here:
http://forums.matronics.com/viewtopic.php?p=381787#381787
===========
arget="_blank">http://www.matronics.com/Navigator?RV10-List
===========
http://forums.matronics.com
===========
le, List Admin.
="_blank">http://www.matronics.com/contribution
===========
==============[/b][/quote] V10-List Email Forum -[/b][/quote] >[/b][/quote] :p>[/b][/quote] /o:p>[/b][/quote] tor?RV10-List">http://www.matronics.com/Navigator?RV10-List[/b][/quote] ==============[/b][/quote] bsp; - MATRONICS WEB FORUMS -[/b][/quote] :p>[/b][/quote] tp://forums.matronics.com[/b][/quote] ==============[/b][/quote] bsp; - List Contribution Web Site -[/b][/quote] e> bsp; � -Matt Dralle, List Admin.[/b][/quote] bution">http://www.matronics.com/contribution[/b][/quote] ==============[/b] [b]
| - The Matronics RV10-List Email Forum - | | Use the List Feature Navigator to browse the many List utilities available such as the Email Subscriptions page, Archive Search & Download, 7-Day Browse, Chat, FAQ, Photoshare, and much more:
http://www.matronics.com/Navigator?RV10-List |
|
|
|
Back to top |
|
 |
carl.froehlich(at)verizon Guest
|
Posted: Sat Aug 25, 2012 2:23 pm Post subject: Differential Pressure Test - Results Question |
|
|
I too have the James Cowl and plenum (stock Van’s IO-360 and Hartzell prop).� At 39 hours now I'm satisfied with the engine temps.� Here are the modifications I made:
<![if !supportLists]>� <![endif]>I was not thrilled with the Van’s lower cowl louvers.� I instead added a set of cowl louvers to the bottom of the cowl.� Photo attached.� While I was able to have acceptable (but on the high side) CHTs with the cowl without the louvers, I had to keep the speed up in the climb (~140 knots).� A hot day run with the louvers (85 degrees ground air temp) have CHTs noticeably cooler – peak temp on an aggressive 120 knot climb to 8500’ was 426 degrees (dropping rapidly once passed 4000’).� In high speed cruise CHTs were between 365 and 390.� I got these louvers from Avery Tools.� I trimmed each side 1/8” and cut off the top two slots.� This is a simple mod, and I will replace the louvers with blank plates for winter time.� Flight data is scattered, but if anything the louvers may have a 1 knot or so speed penalty.
<![if !supportLists]>� <![endif]>I did not use the weird Van’s angled oil cooler mount and my oil temps have been cooler than what I hear on RV-10s using the stock Van’s cowl.� I find it necessary to partially shut the oil cooler air butterfly valve to get the temps up to 190 or so. �Photos attached on how I mounded my cooler.
<![if !supportLists]>� <![endif]>I used the Airflow 2006X oil cooler – and recommend it.
<![if !supportLists]>� <![endif]>I really did not like the heat muffs blasting hot air at the engine mechanical fuel pump (i.e. cabin heat valves are shut).� I mounted the cabin heat control valves on a piece of KoolMat http://www.aircraftspruce.com/catalog/appages/koolmat.php such that the KoolMat folded over the tops of the cabin heat valves and then tucked in between the valves and the forward gear mount (sorry, I could not find of photo but this is very simple).� The result was on a hot day (no cabin heat) the heat muff discharge is directed down toward the cowl exit, not back at the engine.
Still doing speed runs but I’m measurably faster than Van’s numbers.� The James Cowl is not magical, it is simply an adjustment to the tradeoff between drag and cooling.� I’m happy on how it worked out for me.
Carl
--
| - The Matronics RV10-List Email Forum - | | Use the List Feature Navigator to browse the many List utilities available such as the Email Subscriptions page, Archive Search & Download, 7-Day Browse, Chat, FAQ, Photoshare, and much more:
http://www.matronics.com/Navigator?RV10-List |
|
Description: |
|
Filesize: |
62.48 KB |
Viewed: |
13267 Time(s) |
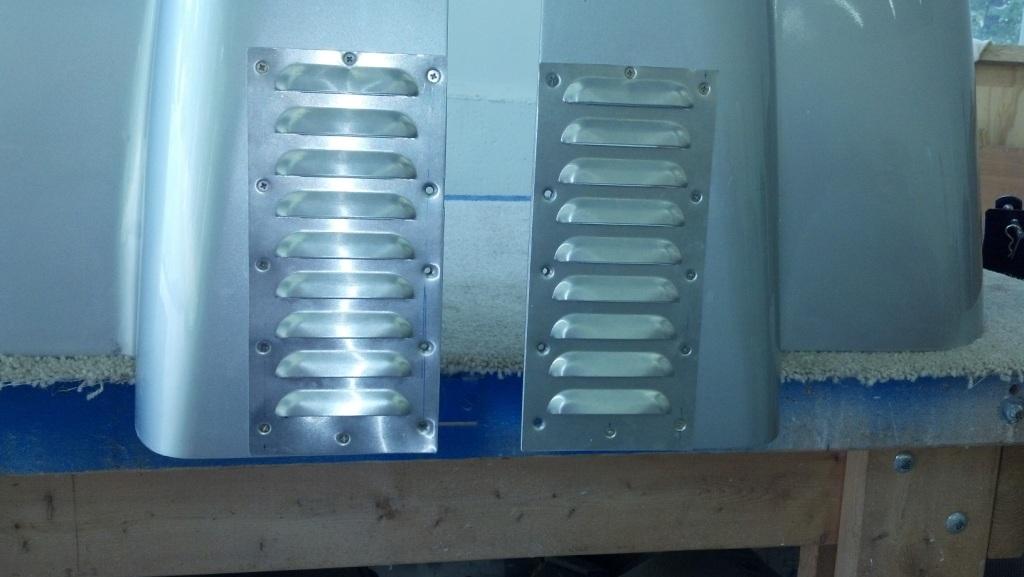
|
Description: |
|
Filesize: |
137.88 KB |
Viewed: |
13267 Time(s) |
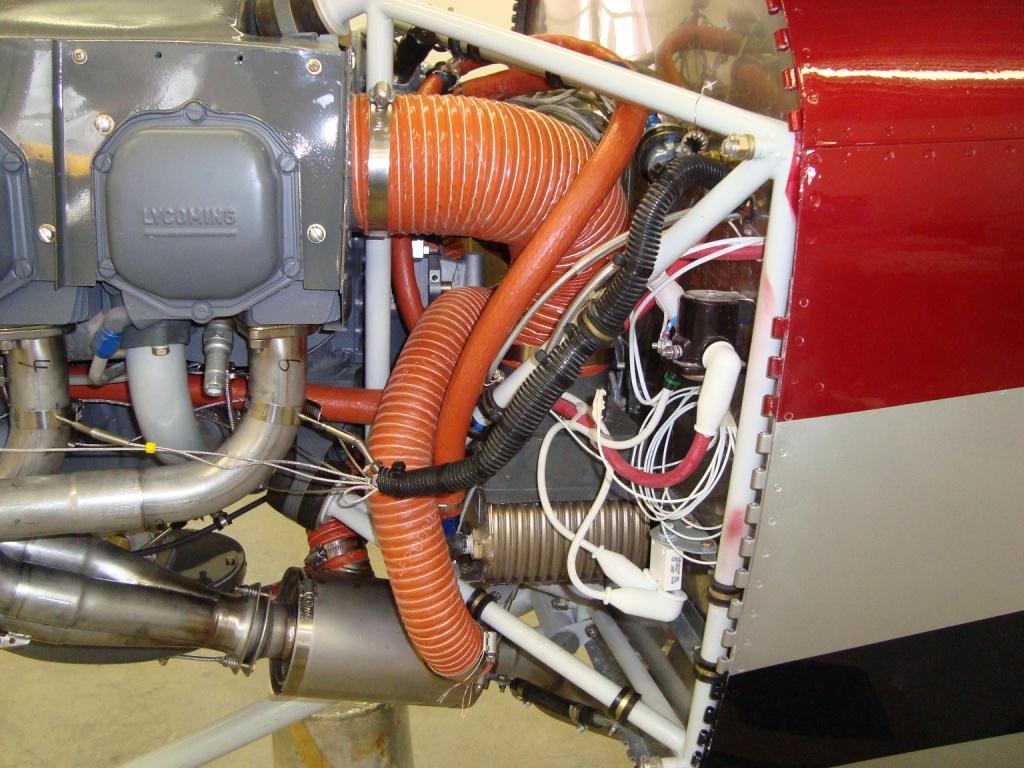
|
Description: |
|
Filesize: |
42.51 KB |
Viewed: |
13267 Time(s) |
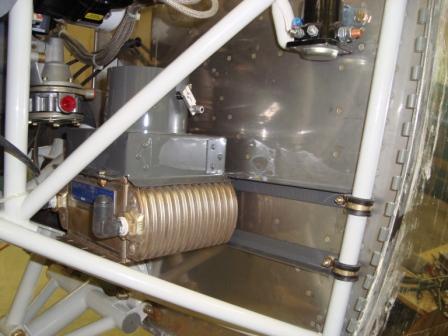
|
|
|
Back to top |
|
 |
robin(at)PaintTheWeb.com Guest
|
Posted: Sat Aug 25, 2012 2:35 pm Post subject: Differential Pressure Test - Results Question |
|
|
IO-360 or IO-540?
Robin
Do Not Archive
From: owner-rv10-list-server(at)matronics.com [mailto:owner-rv10-list-server(at)matronics.com] On Behalf Of Carl Froehlich
Sent: Saturday, August 25, 2012 3:23 PM
To: rv10-list(at)matronics.com
Subject: RE: Differential Pressure Test - Results Question
I too have the James Cowl and plenum (stock Van’s IO-360 and Hartzell prop). At 39 hours now I'm satisfied with the engine temps. Here are the modifications I made:
<![if !supportLists]>� <![endif]>I was not thrilled with the Van’s lower cowl louvers. I instead added a set of cowl louvers to the bottom of the cowl. Photo attached. While I was able to have acceptable (but on the high side) CHTs with the cowl without the louvers, I had to keep the speed up in the climb (~140 knots). A hot day run with the louvers (85 degrees ground air temp) have CHTs noticeably cooler – peak temp on an aggressive 120 knot climb to 8500’ was 426 degrees (dropping rapidly once passed 4000’). In high speed cruise CHTs were between 365 and 390. I got these louvers from Avery Tools. I trimmed each side 1/8” and cut off the top two slots. This is a simple mod, and I will replace the louvers with blank plates for winter time. Flight data is scattered, but if anything the louvers may have a 1 knot or so speed penalty.
<![if !supportLists]>� <![endif]>I did not use the weird Van’s angled oil cooler mount and my oil temps have been cooler than what I hear on RV-10s using the stock Van’s cowl. I find it necessary to partially shut the oil cooler air butterfly valve to get the temps up to 190 or so. Photos attached on how I mounded my cooler.
<![if !supportLists]>� <![endif]>I used the Airflow 2006X oil cooler – and recommend it.
<![if !supportLists]>� <![endif]>I really did not like the heat muffs blasting hot air at the engine mechanical fuel pump (i.e. cabin heat valves are shut). I mounted the cabin heat control valves on a piece of KoolMat http://www.aircraftspruce.com/catalog/appages/koolmat.php such that the KoolMat folded over the tops of the cabin heat valves and then tucked in between the valves and the forward gear mount (sorry, I could not find of photo but this is very simple). The result was on a hot day (no cabin heat) the heat muff discharge is directed down toward the cowl exit, not back at the engine.
Still doing speed runs but I’m measurably faster than Van’s numbers. The James Cowl is not magical, it is simply an adjustment to the tradeoff between drag and cooling. I’m happy on how it worked out for me.
Carl
--
| - The Matronics RV10-List Email Forum - | | Use the List Feature Navigator to browse the many List utilities available such as the Email Subscriptions page, Archive Search & Download, 7-Day Browse, Chat, FAQ, Photoshare, and much more:
http://www.matronics.com/Navigator?RV10-List |
|
|
|
Back to top |
|
 |
jkreidler
Joined: 13 Feb 2008 Posts: 151 Location: Sheboygan Falls WI
|
Posted: Sat Aug 25, 2012 2:48 pm Post subject: Re: Differential Pressure Test - Results Question |
|
|
Gary, so that is the thing I am having trouble getting my head around. In theory we would like to get to a negative pressure in the lower cowl to pull the air through. At first I thought that the lower outlet of the cowl that exits into a void would cause a vacuum. But then again any restriction to flow of the air out of the lower cowl should cause a slight rise in pressure in the lower cowl. I think even getting to zero is a fairly lofty goal as the flow will likely never be perfect. Now as you said anything above zero is directly opposing the flow from the upper cowl. To me even if the flow were zero it would mean that the differential pressure at best would be 2" higher, still borderline short of the 6" goal.
All that said, I am still open since I am struggling to get my head around this. There is much published about what the differential pressure needs to be, there is very little I have found about what an acceptable value is for the pressure in the lower cowl.
Robin, as they say that is the way the pickle squirts. I know all too well the investment of time and money you have in the James Cowl. The question comes back often "Would you go with the James cowl again?", I have to say that I really love the way it looks. I am really disappointed that it does not add to the speed of the airplane and that it is marginal at best for cooling the standard 260 HP engine. Anxious to hear your results on the next project.
Just heard that Neil Armstrong has passed, I was not around in those days but still am touched by what was accomplished. I am saddened not only at his passing but also by the fact that we have pushed space exploration to the bottom of our list of priorities. At the same time other countries around the world are rallying around space like we did back then. Sorry for the off topic turn...
Jason
| - The Matronics RV10-List Email Forum - | | Use the List Feature Navigator to browse the many List utilities available such as the Email Subscriptions page, Archive Search & Download, 7-Day Browse, Chat, FAQ, Photoshare, and much more:
http://www.matronics.com/Navigator?RV10-List |
|
_________________ Jason Kreidler
4 Partner Build - Sheboygan Falls, WI
Tony Kolar, Kyle Hokel, Wayne Elser, Jason Kreidler
N44YH - Flying - #40617 |
|
Back to top |
|
 |
carl.froehlich(at)verizon Guest
|
Posted: Sat Aug 25, 2012 2:55 pm Post subject: Differential Pressure Test - Results Question |
|
|
Oops – I meant to say IO-540.
From: owner-rv10-list-server(at)matronics.com [mailto:owner-rv10-list-server(at)matronics.com] On Behalf Of Robin Marks
Sent: Saturday, August 25, 2012 6:35 PM
To: rv10-list(at)matronics.com
Subject: RE: Differential Pressure Test - Results Question
IO-360 or IO-540?
Robin
From: owner-rv10-list-server(at)matronics.com (owner-rv10-list-server(at)matronics.com) [mailto:owner-rv10-list-server(at)matronics.com (owner-rv10-list-server(at)matronics.com)] On Behalf Of Carl Froehlich
Sent: Saturday, August 25, 2012 3:23 PM
To: rv10-list(at)matronics.com (rv10-list(at)matronics.com)
Subject: RE: Differential Pressure Test - Results Question
I too have the James Cowl and plenum (stock Van’s IO-540 and Hartzell prop). At 39 hours now I'm satisfied with the engine temps. Here are the modifications I made:
<![if !supportLists]>� <![endif]>I was not thrilled with the Van’s lower cowl louvers. I instead added a set of cowl louvers to the bottom of the cowl. Photo attached. While I was able to have acceptable (but on the high side) CHTs with the cowl without the louvers, I had to keep the speed up in the climb (~140 knots). A hot day run with the louvers (85 degrees ground air temp) have CHTs noticeably cooler – peak temp on an aggressive 120 knot climb to 8500’ was 426 degrees (dropping rapidly once passed 4000’). In high speed cruise CHTs were between 365 and 390. I got these louvers from Avery Tools. I trimmed each side 1/8” and cut off the top two slots. This is a simple mod, and I will replace the louvers with blank plates for winter time. Flight data is scattered, but if anything the louvers may have a 1 knot or so speed penalty.
<![if !supportLists]>� <![endif]>I did not use the weird Van’s angled oil cooler mount and my oil temps have been cooler than what I hear on RV-10s using the stock Van’s cowl. I find it necessary to partially shut the oil cooler air butterfly valve to get the temps up to 190 or so. Photos attached on how I mounded my cooler.
<![if !supportLists]>� <![endif]>I used the Airflow 2006X oil cooler – and recommend it.
<![if !supportLists]>� <![endif]>I really did not like the heat muffs blasting hot air at the engine mechanical fuel pump (i.e. cabin heat valves are shut). I mounted the cabin heat control valves on a piece of KoolMat http://www.aircraftspruce.com/catalog/appages/koolmat.php such that the KoolMat folded over the tops of the cabin heat valves and then tucked in between the valves and the forward gear mount (sorry, I could not find of photo but this is very simple). The result was on a hot day (no cabin heat) the heat muff discharge is directed down toward the cowl exit, not back at the engine.
Still doing speed runs but I’m measurably faster than Van’s numbers. The James Cowl is not magical, it is simply an adjustment to the tradeoff between drag and cooling. I’m happy on how it worked out for me.
Carl
--
| - The Matronics RV10-List Email Forum - | | Use the List Feature Navigator to browse the many List utilities available such as the Email Subscriptions page, Archive Search & Download, 7-Day Browse, Chat, FAQ, Photoshare, and much more:
http://www.matronics.com/Navigator?RV10-List |
|
|
|
Back to top |
|
 |
thane
Joined: 27 Nov 2006 Posts: 56
|
Posted: Sat Aug 25, 2012 4:45 pm Post subject: Differential Pressure Test - Results Question |
|
|
One thing I found after awhile running the James cowl and plenum was that in flight the plenum would pressurize and rise up in the front, and was even rubbing on the cowl. Once I realized what was happening, I made a bracket on the front of the plenum, and then safety wired the bracket to the case half on the front of engine. That has definately helped. In the hot Season I also, this year, put a plug behind the #6 cylinder where the pulloff for cabin heat is. I live here in the South so I only have the one supply and tee off for the heat. Just never needed more heat, works almost too good in our mild Winters. I hate to hear about all the heat issues, but I truely have no hi oil or cylinder temps.
Coimming back today from KILM, 4500ft. 21" 2300 rpm, 10.5 gph LOP. Oil temp was 171, all CLY. barely over 315. OAT, of course was a cool 60F. Anyway good luck, I hope you find a solution.
Thane
RV-10
228Hrs.
[quote] ---
| - The Matronics RV10-List Email Forum - | | Use the List Feature Navigator to browse the many List utilities available such as the Email Subscriptions page, Archive Search & Download, 7-Day Browse, Chat, FAQ, Photoshare, and much more:
http://www.matronics.com/Navigator?RV10-List |
|
_________________ Working on finish kit: I hate fiberglass!! |
|
Back to top |
|
 |
Barry
Joined: 16 Sep 2008 Posts: 108
|
Posted: Mon Aug 27, 2012 6:39 am Post subject: Re: Differential Pressure Test - Results Question |
|
|
I too have the SJ cowl and pleneum, and have had the same cooling problems. I now can climb and keep oil temps +/- 210F and CHT's under 400F when it's hot OAT. In cruise I run LOP -50F or ROP 150F and the oil is 195-205F and CHT 385-395F on #5 or #6; the rest of the CHT's are lower. These are the mods I have done in order:
1. Installed 4 louvers, 2 on bottom, 2 on side of cowl like a C-182
2. Cut the exit area of the cowl so it opened it up at the rear about 1 1/2"
3. Installed a new pleneum from Sam that is more wedge shaped ( higher in the rear) which gives more volume for incoming air
4. Installed the larger rings
I have done speed checks with two other stock RV-10's at the same power settings and our speeds were pretty much the same.
I plan on putting some air dams in front of #1&2 cyl to see if I can get #5&6
CHT's down a little
My wife, Amy Laboda, did a write up in Kitplanes a while back on the process, so check those out. Give me a call if ya have any questions 239-567-2271. Blue Skys Barry
| - The Matronics RV10-List Email Forum - | | Use the List Feature Navigator to browse the many List utilities available such as the Email Subscriptions page, Archive Search & Download, 7-Day Browse, Chat, FAQ, Photoshare, and much more:
http://www.matronics.com/Navigator?RV10-List |
|
|
|
Back to top |
|
 |
jkreidler
Joined: 13 Feb 2008 Posts: 151 Location: Sheboygan Falls WI
|
Posted: Tue Aug 28, 2012 4:19 am Post subject: Re: Differential Pressure Test - Results Question |
|
|
Barry, thanks for the information. I have read your article, great write-up, thanks!
I was wondering if the volume of the plenum could ever get too large?
Thanks, Jason
| - The Matronics RV10-List Email Forum - | | Use the List Feature Navigator to browse the many List utilities available such as the Email Subscriptions page, Archive Search & Download, 7-Day Browse, Chat, FAQ, Photoshare, and much more:
http://www.matronics.com/Navigator?RV10-List |
|
_________________ Jason Kreidler
4 Partner Build - Sheboygan Falls, WI
Tony Kolar, Kyle Hokel, Wayne Elser, Jason Kreidler
N44YH - Flying - #40617 |
|
Back to top |
|
 |
Barry
Joined: 16 Sep 2008 Posts: 108
|
Posted: Tue Aug 28, 2012 3:19 pm Post subject: Re: Differential Pressure Test - Results Question |
|
|
Hi Jason; I think Sam's thinking for the larger volume plenum was to reduce the internal pressure and speed the air at the inlets to get good flow into the plenum. We were thinking with the lower volume plenum it could create back pressure and create a restriction for the inlet air and cause it to spill out around the rings. Sorry no real engineering data just trial and error. It has seemed to help and I'm sure there is a point where too much volume ie. lower pressure, is not optimal, but again no hard data. Good luck Barry
| - The Matronics RV10-List Email Forum - | | Use the List Feature Navigator to browse the many List utilities available such as the Email Subscriptions page, Archive Search & Download, 7-Day Browse, Chat, FAQ, Photoshare, and much more:
http://www.matronics.com/Navigator?RV10-List |
|
|
|
Back to top |
|
 |
robin(at)PaintTheWeb.com Guest
|
Posted: Tue Aug 28, 2012 5:13 pm Post subject: Differential Pressure Test - Results Question |
|
|
Based on research we did at the time our understanding of an "ideal" plenum shape would be an ever increasing volume as the air moves aft. To that effect we took the ill-performing James plenum and hacked the fiberglass off both upper sides above the cylinder heads. In place of the fiberglass we mated a metal plenum of ever increasing volume with the end result being a plenum with ~50% more volume (WAG). The net effect of this change was ZERO. Not really any discernible difference other than I now had a Franken-plenum. It was ugly but it was symmetrical and just about as clean to the airflow as the original plenum. I truly expected to see some difference good or bad. But no difference. This is the same plenum I fly today. Literally today.
I am willing to place a few dollars that an even tighter plenum in this situation will NOT aid in cooling.
In all cowl configurations some air to a significant amount of inlet air actually reverses itself and goes out the inlets. This is part of the dirtiness of the front end of your aircraft. Minimizing the amount backtracking out will help performance. The racers have extra small inlets for max speed but minimum engine lifespan. Striking a balance is the goal. Again the simplest answer is the standard vans cowl & baffle. My next attempt will be larger inlets (new cowl) and a baffle system.
Robin
--
| - The Matronics RV10-List Email Forum - | | Use the List Feature Navigator to browse the many List utilities available such as the Email Subscriptions page, Archive Search & Download, 7-Day Browse, Chat, FAQ, Photoshare, and much more:
http://www.matronics.com/Navigator?RV10-List |
|
|
|
Back to top |
|
 |
40950(at)rv10.net Guest
|
Posted: Thu Aug 30, 2012 6:09 pm Post subject: Differential Pressure Test - Results Question |
|
|
Robin,
I have a very old, unused aero degree from 1977 so don't consider myself an expert on the subject but have some thoughts regarding your below discussion.
I believe the larger volume plenum theory was to allow a reduction in air velocity due to larger cross section area inside the plenum thus increasing the static pressure as the flow decelerates. This should increase pressure across the cylinder cooling fins and help overall air flow through the cowl. However, the results would probably be no different if the air flow is choked at the cowl inlet (or outlet for that matter) due to too small of inlet area. This could account for your lack of change in results. So you might retry the larger plenum after you open the inlets and see what happens. No guarantees but worth a try since you already have the larger plenum built. The other area to check out would be exit area at the bottom cowl to ensure low exit pressure.
Let us know how it works out.
Tom
40950 wings slow build - seems like forever...
On Aug 28, 2012, at 8:13 PM, Robin Marks wrote:
[quote]
Based on research we did at the time our understanding of an "ideal" plenum shape would be an ever increasing volume as the air moves aft. To that effect we took the ill-performing James plenum and hacked the fiberglass off both upper sides above the cylinder heads. In place of the fiberglass we mated a metal plenum of ever increasing volume with the end result being a plenum with ~50% more volume (WAG). The net effect of this change was ZERO. Not really any discernible difference other than I now had a Franken-plenum. It was ugly but it was symmetrical and just about as clean to the airflow as the original plenum. I truly expected to see some difference good or bad. But no difference. This is the same plenum I fly today. Literally today.
I am willing to place a few dollars that an even tighter plenum in this situation will NOT aid in cooling.
In all cowl configurations some air to a significant amount of inlet air actually reverses itself and goes out the inlets. This is part of the dirtiness of the front end of your aircraft. Minimizing the amount backtracking out will help performance. The racers have extra small inlets for max speed but minimum engine lifespan. Striking a balance is the goal. Again the simplest answer is the standard vans cowl & baffle. My next attempt will be larger inlets (new cowl) and a baffle system.
Robin
--
| - The Matronics RV10-List Email Forum - | | Use the List Feature Navigator to browse the many List utilities available such as the Email Subscriptions page, Archive Search & Download, 7-Day Browse, Chat, FAQ, Photoshare, and much more:
http://www.matronics.com/Navigator?RV10-List |
|
|
|
Back to top |
|
 |
robin(at)PaintTheWeb.com Guest
|
Posted: Thu Aug 30, 2012 9:36 pm Post subject: Differential Pressure Test - Results Question |
|
|
Tom,
Your description is as I thought but I didn't want to get specific due to not owning an aero degree of any vintage. We also agree that the issue is and always was inlet area. I think I mentioned investigating exit area in my note. Still of minimal benefit w/o adequate inlet area.
As discussed no need for a larger plenum in my future. Baffles and a replacement cowl are already ordered and waiting.
Thanks,
Robin
--
| - The Matronics RV10-List Email Forum - | | Use the List Feature Navigator to browse the many List utilities available such as the Email Subscriptions page, Archive Search & Download, 7-Day Browse, Chat, FAQ, Photoshare, and much more:
http://www.matronics.com/Navigator?RV10-List |
|
|
|
Back to top |
|
 |
jkreidler
Joined: 13 Feb 2008 Posts: 151 Location: Sheboygan Falls WI
|
Posted: Fri Aug 31, 2012 4:44 am Post subject: Re: Differential Pressure Test - Results Question |
|
|
I have been researching this whole topic in depth over the last week or so. There is one site in particular with some really good information, check out www.n91cz.com specifically his articles on cooling and his link to interesting technical reports “NASA CR 3405”. I have also been getting some advice from the guys over on the other forum. www.vansairforce.com/community/showthread.php?t=79454
While we are in the process of gathering the necessary data through actual pressure measurements, I think it is premature to assume the cowl inlet is too small.
Here is what I have learned so far, this may be obvious to others but it took me time to pick it up (I may have eaten paint chips as a kid).
Dynamic pressure is generated as we push the airplane through the air, to the tune of around 6.5” H2O (at) 100 knots, 14.6” H2O (at) 150 knots, 25.9” H2O (at) 200 knots. We can covert airspeed to pressure and vice versa, think of it this way, the tank of your air compressor contains pressure, when you open a blow nozzle you convert that pressure into airspeed. So we have a fixed ‘pressure’ available depending on our airspeed, no more, no less. So depending on your speed we will need to convert some of that dynamic pressure into differential pressure between the upper and lower deck of the engine in order to keep things cool – duh that part is easy. So the other day we took some measurements and I had asked the group what it all means. In our example we were seeing pressure in our plenum of 6.5” at ~150 knots – wow that means we are only converting 6.5” of the available dynamic pressure of 14.6” into pressure in the upper cowl. Now given that our lower cowl pressure was 3” it means that we only have 3.5” of differential pressure available to cool the engine, about half of what we should have. It also means that if we get the lower cowl pressure all the way down to zero, by let’s say, I don’t know, completely removing it, we still would only have marginal differential pressure cooling air available.
So our top side is terrible at converting the 150 knot air stream into usable dynamic pressure, now let’s look at the lower cowl. Remember that we have low dynamic pressure in the lower cowl and we do not have very far to go in order to improve it, so adding cowl flaps and louvers will not get us where we need to be, no matter what until we fix the top side the changing the bottom will yield marginal results at best. One more key point to think about in the lower cowl, when that air exits the lower cowl we will need to get it back up to speed. If it is at zero dynamic pressure it means it is standing still, meaning we will have to accelerate it back up to 150 knots, and that is cooling drag. Look at it this way if the air came into the top cowl at 150 knots (14.6”) and left the cowl at 150 knots (14.6”) we would have zero cooling drag, but since it comes in at 150 knots and does some work in the middle and exits at a lower airspeed we have cooling drag. What we really want to have happen is for the air to come in and do the absolute bare minimum amount of work required to cool things down and then exit. Ideally we want the upper deck pressure to equal the dynamic pressure available due to airspeed, and the lower cowl pressure to equal that value minus the difference in pressure require to cool the engine for a given condition.
Great, so what the heck does all that really mean, where am I going to focus my effort? First things first, before doing anything drastic it is important to collect the pressure data. To install all of the instrumentation and do a test run took about three hours, that is nothing! Per the articles on the web site I referenced above I want to start by looking at the area just behind the cooling inlets (diffusers). Turns out if the shape directly behind the inlet rings is wrong the pressure generated will build a dam that prevents any more air from getting in, this is called external pressure recovery and requires a much larger inlet. What I want to happen is for the air to come into the inlet and the inlet to be shaped aerodynamically like a venturi so the air expands directly behind the inlet. This means a very smooth transition so the air doesn’t ‘stall’ create turbulence and dam up, which is called internal pressure recovery. Once we get beyond that point the shape doesn’t really matter. Don’t ask me what all of that looks like yet, I am still trying to figure that out and the guys took the airplane to Yellowstone over Labor Day. But for now I am putting on hold the idea of cutting in bigger inlet rings. When / if we get the upper plenum pressure to where it needs to be I may look at cowl flaps to throttle the exit depending on flight conditions like airspeed and power settings. The purpose of the cowl flaps at that point should be to close off the opening rather than enlarge it in order to reduce cooling drag.
On another note for those of you with baffles, the NASA article used a Piper Aztec (Lycoming 540’s) as a test bed. There data showed that in that installation the baffles leaked by 38% of the cooling air. That is a huge amount of cooling drag, so like Tim and others have said spend some time and seal up your baffles to the engine. Even if you don’t have cooling problems you are still giving away power and speed by having leaks.
I think there is hope…. I will let you know what comes of all of this but it will be a while.
Sorry for the long post - Jason
| - The Matronics RV10-List Email Forum - | | Use the List Feature Navigator to browse the many List utilities available such as the Email Subscriptions page, Archive Search & Download, 7-Day Browse, Chat, FAQ, Photoshare, and much more:
http://www.matronics.com/Navigator?RV10-List |
|
_________________ Jason Kreidler
4 Partner Build - Sheboygan Falls, WI
Tony Kolar, Kyle Hokel, Wayne Elser, Jason Kreidler
N44YH - Flying - #40617 |
|
Back to top |
|
 |
Mauledriver(at)nc.rr.com Guest
|
Posted: Fri Aug 31, 2012 6:49 am Post subject: Differential Pressure Test - Results Question |
|
|
I've been following this but may have missed it; did anyone supply
pressure numbers for the stock cowl setup to facilitate comparision?
Bill
On 8/31/2012 8:44 AM, jkreidler wrote:
Quote: | In our example we were seeing pressure in our plenum of 6.5” at ~150 knots – wow that means we are only converting 6.5” of the available dynamic pressure of 14.6” into pressure in the upper cowl. Now given that our lower cowl pr!
essure was 3” it means that we only have 3.5” of differential pressure available to cool the engine, about half of what we should have. It also means that if we get the lower cowl pressure all the way down to zero, by let’s say, I don’t know, completely removing it, we still would only have marginal differential pressure cooling air available.
|
| - The Matronics RV10-List Email Forum - | | Use the List Feature Navigator to browse the many List utilities available such as the Email Subscriptions page, Archive Search & Download, 7-Day Browse, Chat, FAQ, Photoshare, and much more:
http://www.matronics.com/Navigator?RV10-List |
|
|
|
Back to top |
|
 |
jkreidler
Joined: 13 Feb 2008 Posts: 151 Location: Sheboygan Falls WI
|
Posted: Fri Aug 31, 2012 6:54 am Post subject: Re: Differential Pressure Test - Results Question |
|
|
Not that I know of, if someone wants to do a run let me know and we can talk about the equipment.
Jason
| - The Matronics RV10-List Email Forum - | | Use the List Feature Navigator to browse the many List utilities available such as the Email Subscriptions page, Archive Search & Download, 7-Day Browse, Chat, FAQ, Photoshare, and much more:
http://www.matronics.com/Navigator?RV10-List |
|
_________________ Jason Kreidler
4 Partner Build - Sheboygan Falls, WI
Tony Kolar, Kyle Hokel, Wayne Elser, Jason Kreidler
N44YH - Flying - #40617 |
|
Back to top |
|
 |
|
|
You cannot post new topics in this forum You cannot reply to topics in this forum You cannot edit your posts in this forum You cannot delete your posts in this forum You cannot vote in polls in this forum You cannot attach files in this forum You can download files in this forum
|
Powered by phpBB © 2001, 2005 phpBB Group
|