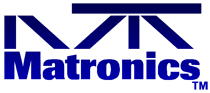 |
Matronics Email Lists Web Forum Interface to the Matronics Email Lists
|
View previous topic :: View next topic |
Author |
Message |
info(at)mtfind.com Guest
|
Posted: Sat Jul 05, 2008 8:58 am Post subject: Bridge diodes VS Schottky |
|
|
I have seen the debate over the low cost Bridge diode VS the Schottky diode
come up year after year mostly based on the opinion the bridge is good
enough and easy to get at RS, mount it anywhere to a bracket (implying no
significant heat sinking is needed etc). Perhaps I have missed it but I do
not recall a single technical analysis based on engineering evaluation of
the specified values based on data sheet analysis. Further many suggested
uses show two diodes of the bridge in parallel. This does not increase the
current capacity much as diodes do not share current well as one will get
hotter and hog the current making it hotter etc. Its not clear the
reliability is increased as internal bridge package connections are not
known and vary with the manufacturer. Diodes typically fail short and only
open if the current is high enough.
Over this nearly 15 year period the bridge diode has been used for several
applications but most often as I recall is to isolate the emergency (now
endurance) bus. This bus originally was apparently designed for 2-3 amp max.
Today many users have a 8 amp load and still use the bridge diode. Notably,
Eric has promoted the Schottky diode and been shouted down over and over
with no real data to support the opposing positions.
15 years ago I selected the Schottky diode as I had dual batteries and
wanted to use the diode to provide battery isolation and and also single
source battery charging. The bridge diode simply would not charge the
battery to full charge while the Schottky did.
Data sheet worst case design analysis can be difficult as the typical data
sheet is intended to make the part look good and typically shows information
that is at least misleading with the real worst case information hard to
find.
Today the bridge diode part is very old and many manufacturers have
shortened the data sheet to the extent its not possible to determine the
worst case parameters. Some data sheets are simply scans from another
Manufacturer's old data sheet.
I evaluated both types of bridge diodes available today. The GBPC series and
the older MB series. The MB series has a metal base with metal sides. The
GBPC series has a smaller metal base and no metal sides. The electrical
parameters are essentially the same and both are available with faston type
connections. Remember some data is shown as nominal, not max ratings.
Remember that bridge diodes are rated as a full wave rectifier which means
some data must be converted to DC.
Here are the worst case values for Vf at 1 and 10 amps and at 25C and 150C.
This is for a single diode.
Note the data is basically a straight line from 1A to 10A which allows for
simple intermediate current calculations
Vf 1A 25C Vf 10A 25C Vf 1A 150C Vf 10A 150C
0.83V 1.05V 0.63V 0.85V
Power dissipation as follows at 25C
1A 2.5A 5.0A 7.5A 10A
0.83W 2.23W 4.7W 7.5W 10.5W
To figure case temp consider 1.9deg/c per watt from die temp. For example
case temp max at 10 amps is 10.5 times 1.9 approx 20C or 130C max. If
ambient temp is 40C near the mount then the heat sink must dissipate 10.5W
with a temp drop of 90C across the heatsink.
The above does not allow for the case to heat sink temp resistance depending
on heat sinking surface material IE grease. The above does not allow for
service derating. The aerospace industry recommends no more that 100C case
temp which increases the heat sink size for a temp gradient of from 90 to 60
c max
Its clear that above a current of 1A, some (or a lot of) heat sink is
required. I do not recall any specified requirement other than to simply
mount it on a small bracket. No mention of the surface smoothness of the
bracket nor what it's thickness or size is. No mention of the required heat
sink grease etc. At 10 amps a couple of manufacturers require a heat sink
size of 6" x 2.2" x 2.2" finned plate plus additional requirements to keep
the junction temperature below 150C (the max rated temperature). To
calculate case temp use 1.9deg/c per watt from die temp. For example case
temp max at 10 amps is 10.5 times 1.9 approx 20C or 130C max.
Thus its not wrong to state a 10W heat sink is needed but there is a string
of calculations required to determine the physical heat sink needed.
Now lets look at the current Schottky diode available. In this case the
diode selected is the DSS2x121-0045B made by IXYS. Two independent 120 amp
diodes. In the case of Schottky diodes the higher the current rating the
lower the Vf at low currents as seen in this application. IR used to be the
low Vf leader but this IXYS is slightly better and lower cost and easy to
get. ( www.findchips.com )
Vf 1A 25C Vf 10A 25C Vf 1A 150C Vf 10A 150C
0.29V 0.34A 0.15V 0.24V
Power dissipation as follows at 25C
1A 2.5A 5.0A 7.5A 10A
0.29W 0.78W 1.58W 2.48W 3.40W
Clearly a far better part to use. Just as easy to mount and wiring support
is easier.
If battery charging is intended thru this diode, not only is a full charge
possible but there is no current overload as is likely to occur with the
bridge if the battery being charged is significantly discharged and where
the charging current can be well above 10 amps.
Why worst case analysis? Because its not possible to know the actual
parameters of the parts used by the various builders. Manufacturers do
produce worst case parts and are often sold to resellers like RS with the
higher quality parts are distributed to the industry market.
Why not just do a test and use that as proof of the design? A test only
proves the worst case analysis is valid and is only good for the exact parts
used and does not indicate what results will be with similar parts from the
identical manufacturers production batch. Proper engineering design always
starts with a worst case analysis of the design followed with a test to show
the results are inside the worst case analysis. Only then is the design
released for production or in this case released for the general builder to
build and be sure it will perform to expectations.
Availability? Its strange to me that the availability of the bridge at RS is
promoted but many of the recommended switches are only available thru B&C.
Modern electronics use switching supplies which use more or less power not
amps as input baded on input voltage. Thus the higher the Vf the more amps
required and thus shorter battery life as the battery life in amp hours goes
down as the amp drain goes up.
The cost of the superior Schottky part is very small compared to the cost of
the electrical wiring/terminal etc system and insignificant to the total
cost of the aircraft.
Paul
| - The Matronics AeroElectric-List Email Forum - | | Use the List Feature Navigator to browse the many List utilities available such as the Email Subscriptions page, Archive Search & Download, 7-Day Browse, Chat, FAQ, Photoshare, and much more:
http://www.matronics.com/Navigator?AeroElectric-List |
|
|
|
Back to top |
|
 |
nuckolls.bob(at)cox.net Guest
|
Posted: Sat Jul 05, 2008 2:10 pm Post subject: Bridge diodes VS Schottky |
|
|
At 09:53 AM 7/5/2008 -0700, you wrote:
Quote: |
I have seen the debate over the low cost Bridge diode VS the Schottky
diode come up year after year mostly based on the opinion the bridge is
good enough and easy to get at RS, mount it anywhere to a bracket
(implying no significant heat sinking is needed etc). Perhaps I have
missed it but I do not recall a single technical analysis based on
engineering evaluation of the specified values based on data sheet
analysis. Further many suggested uses show two diodes of the bridge in
parallel. This does not increase the current capacity much as diodes do
not share current well as one will get hotter and hog the current making
it hotter etc. Its not clear the reliability is increased as internal
bridge package connections are not known and vary with the manufacturer.
Diodes typically fail short and only open if the current is high enough.
Over this nearly 15 year period the bridge diode has been used for several
applications but most often as I recall is to isolate the emergency (now
endurance) bus. This bus originally was apparently designed for 2-3 amp
max. Today many users have a 8 amp load and still use the bridge diode.
Notably, Eric has promoted the Schottky diode and been shouted down
|
. . . you've mis-interpreted the discussions. Nobody from
this side of the list-server has ever shouted at anyone . . .
Quote: | over and over with no real data to support the opposing positions.
|
Exactly! The superior performance of the Schottky diode is
not and never has been in question. What WAS in question was
the offering of an alternative to the lowly silicon rectifier
with equal dearth of data to support the promotion of a part
that was more expensive, had to be acquired from a source perhaps
less convenient than Radio Shack and was no easier to install.
Further, this had nothing to do with me, B&C or even Radio Shack
making a buck on the occasional sale of a bridge rectifier. When
the "new and improved" product came to the market, the lack of
data left many folks who already had bridge rectifiers installed
wondering if they'd done a bad thing . . . "Gee, should I rip it
out and put in the really good part?"
While I was consistently suggesting that meeting design goals
with a minimum cost of ownership opens a lot of alternative
doors, the proponents of
Quote: | 15 years ago I selected the Schottky diode as I had dual batteries and
wanted to use the diode to provide battery isolation and and also single
source battery charging. The bridge diode simply would not charge the
battery to full charge while the Schottky did.
|
One COULD quibble over what the design goals for achieving "full charge".
Clearly, if you have say 24 hours to wait, 13.8 volts will top off a room
temperature lead-acid battery of any pedigree . . . but as a practical
matter, we'd like to get our ship's battery topped off in the first few
minutes of flight and under variety of temperatures. So we force the
battery to suffer acceptable indignities by boosting the bus voltage
under a perfectly rational idea that the goal is to store energy to
meet design goals . . . not squeeze a few extra flights of service
life out of a battery that is difficult to qualify. But yes, if one
chooses to go the diode isolator route for batteries, the Schottky
device offers a demonstrable advantage over silicon junction
rectifiers. I'll point out further that your design goals for
incorporation of a diode were decidedly different than for normal
feed path steering of the e-bus power.
Quote: | Data sheet worst case design analysis can be difficult as the typical data
sheet is intended to make the part look good and typically shows
information that is at least misleading with the real worst case
information hard to find.
|
Shucks . . . you're not suppose to say that in front of
everybody!!! Yes, unless one makes a living at the
interpretation, validation and application of manufacture's
data sheets, it CAN be a daunting and sometimes frustrating
task. We had some pretty good discussions here on the List
a few years back when curves for guaranteed performance
on breakers was misinterpreted as LIMITS to performance.
As a designer with decades of experience of working with
those breakers (knowing about their demonstrated capabilities
outside the guaranteed performance), I was able to
exploit their capabilities in ways that got some folks
really excited . . . for no good reason based on the physics.
Quote: | Today the bridge diode part is very old and many manufacturers have
shortened the data sheet to the extent its not possible to determine the
worst case parameters. Some data sheets are simply scans from another
Manufacturer's old data sheet.
I evaluated both types of bridge diodes available today. The GBPC series
and the older MB series. The MB series has a metal base with metal sides.
The GBPC series has a smaller metal base and no metal sides. The
electrical parameters are essentially the same and both are available with
faston type connections. Remember some data is shown as nominal, not max
ratings. Remember that bridge diodes are rated as a full wave rectifier
which means some data must be converted to DC.
Here are the worst case values for Vf at 1 and 10 amps and at 25C and
150C. This is for a single diode.
Note the data is basically a straight line from 1A to 10A which allows for
simple intermediate current calculations
Vf 1A 25C Vf 10A 25C Vf 1A 150C Vf 10A 150C
0.83V 1.05V 0.63V 0.85V
Power dissipation as follows at 25C
1A 2.5A 5.0A 7.5A 10A
0.83W 2.23W 4.7W 7.5W 10.5W
To figure case temp consider 1.9deg/c per watt from die temp. For example
case temp max at 10 amps is 10.5 times 1.9 approx 20C or 130C max. If
ambient temp is 40C near the mount then the heat sink must dissipate 10.5W
with a temp drop of 90C across the heatsink.
|
Exactly. And that works out to a heatsink with about 8.5C/Watt
thermal resistance which is NOT a very big heatsink.
Quote: | The above does not allow for the case to heat sink temp resistance
depending on heat sinking surface material IE grease. The above does not
allow for service derating. The aerospace industry recommends no more that
100C case temp which increases the heat sink size for a temp gradient of
from 90 to 60 c max
Its clear that above a current of 1A, some (or a lot of) heat sink is
required. I do not recall any specified requirement other than to simply
mount it on a small bracket.
|
Hmmmm . . . don't know about "small bracket" . . . . I've
suggested any flat surface of aircraft sheet metal which is
generally a firewall, shelf or perhaps skin.
Quote: | No mention of the surface smoothness of the bracket nor what it's
thickness or size is. No mention of the required heat sink grease etc. At
10 amps a couple of manufacturers require a heat sink size of 6" x 2.2" x
2.2" finned plate plus additional requirements to keep the junction
temperature below 150C (the max rated temperature). To calculate case
temp use 1.9deg/c per watt from die temp. For example case temp max at 10
amps is 10.5 times 1.9 approx 20C or 130C max.
Thus its not wrong to state a 10W heat sink is needed but there is a
string of calculations required to determine the physical heat sink needed.
|
You stole my thunder sir! I'm preparing a Shop Notes document
that speaks to power and temperature ratings as is applies to
combinations of devices that dissipate energy and products that
are intended to keep those devices from self-destruction from
self-heating. The REAL specification of heat-sink performance
is stated in temperature rise per watt of heat dissipated.
A heat sink of ANY physical size can dissipate 10 watts. Depending
on how big it is, the temperature may go up 2 degrees or 200
degrees. Further, the slightest breeze will have a profound
effect on heat sink performance. Needless to say, there are
few places in our airplanes that are NOT breezy! But the
short story is that suggesting a builder use a heatsink rated
for 10W is not the whole story.
Quote: | Now lets look at the current Schottky diode available. In this case the
diode selected is the DSS2x121-0045B made by IXYS. Two independent 120 amp
diodes. In the case of Schottky diodes the higher the current rating the
lower the Vf at low currents as seen in this application. IR used to be
the low Vf leader but this IXYS is slightly better and lower cost and easy
to get. ( www.findchips.com )
Vf 1A 25C Vf 10A 25C Vf 1A 150C Vf 10A 150C
0.29V 0.34A 0.15V 0.24V
Power dissipation as follows at 25C
1A 2.5A 5.0A 7.5A 10A
0.29W 0.78W 1.58W 2.48W 3.40W
Clearly a far better part to use. Just as easy to mount and wiring support
is easier.
If battery charging is intended thru this diode, not only is a full charge
possible but there is no current overload as is likely to occur with the
bridge if the battery being charged is significantly discharged and where
the charging current can be well above 10 amps.
|
Absolutely. I've seen several battery powered systems
fall short of design goals because the folks forgot that
a battery intended to supply perhaps 5-10 amps in use
can DRAW several times that current while being recharged.
Quote: | Why worst case analysis? Because its not possible to know the actual
parameters of the parts used by the various builders. Manufacturers do
produce worst case parts and are often sold to resellers like RS with the
higher quality parts are distributed to the industry market.
|
Do you have some reference to support this? In years gone
by there have been countless suppliers of parts to the
hobby electronics market that indeed offered "floor sweepings"
in bags. I discovered the photo-sensitivity of junction
transistors when devices I'd purchased as "2N3904" transistors
had a terrible amount of hum that disappeared when the florescent
light over the bench was shut off. The plastic was not quite
as opaque as one might wish for a "real" 2N3904.
However, the real cost of good parts has become so small
compared to all the other costs of distributing and marketing
that there is little value in spending labor to create a
separate product stream for sub-standard parts. Further, the
idea that sub-standard parts is even exist is suspect. Modern
semiconductor houses have so many process checks in place along
the assembly line that sub-standard parts are going to be
pitched long before they're put into final packages and marked
with the manufacturer's brand and part-number. My sense
is that the days of Poly-Pak's and Olson Radio Warehouse's
"bargain bags" are long behind us.
Quote: | Why not just do a test and use that as proof of the design? A test only
proves the worst case analysis is valid and is only good for the exact
parts used and does not indicate what results will be with similar parts
from the identical manufacturers production batch. Proper engineering
design always starts with a worst case analysis of the design followed
with a test to show the results are inside the worst case analysis. Only
then is the design released for production or in this case released for
the general builder to build and be sure it will perform to expectations.
Availability? Its strange to me that the availability of the bridge at RS
is promoted but many of the recommended switches are only available thru B&C.
|
I "promote" selection of parts adequate to the task
with some notion of $time$ expended to acquire those
parts. A $1.50 switch from the store is no bargain
if you hop in the car and drive 7 miles to buy it . . .
while saving your $5.00 switch in the drawer for a
"more demanding" task.
The part numbers cited in my drawings are artifacts
of the catalog numbers I assigned to those parts
while I was supplying them to the OBAM aviation
industry. When I decided to move that activity to
B&C . . . many of those numbers were retained and
are most often cited in my work much of which dates
back 20 years.
However, I've never attempted to hide the fact that
there are MANY alternate sources for equal or even
better parts if the builder has the willingness, $time$
and skill to acquire them. I had a builder drop by the
booth at OSH several times during the week with small
scraps of wire in hand. He was scouring the Fly-Market
for "wire bargains". I don't know how his project
was ultimately wired. Given that I saw a lot of
him during the week suggests he would have been
WAAAYyyy better off buying new, M22759 wire at Aircraft
Spruce prices than to spend the $time$ necessary to
insure that his "bargains" were appropriate to the
task.
I submit that the parts I've oft suggested are an
aid for those who believe their time is better spent
bucking in a few more perfect rivets and bending
one more ideal stiffener. This is opposed to combing
the 'Net' in some attempt to save a few dollars on parts
selection when their personal expertise is orthodontics
or managing a grocery store.
Quote: | Modern electronics use switching supplies which use more or less power not
amps as input baded on input voltage. Thus the higher the Vf the more amps
required and thus shorter battery life as the battery life in amp hours
goes down as the amp drain goes up.
The cost of the superior Schottky part is very small compared to the cost
of the electrical wiring/terminal etc system and insignificant to the
total cost of the aircraft.
|
This discussion has never been about cost of parts.
It has always been about selection of parts adequate
to the design goals with the minimum total expenditure
of $time$ to select, acquire, install, and maintain
those parts.
In situations where the design goals were changed
(like battery isolation, and boss-hog e-bus loads)
then some re-evaluation of suggested parts is in
order. I've take data in the chamber on a variety
of diodes, done the stress tests to ascertain thermal
resistance of the parts and done all the photographs.
Measured the practical thermal resistance of small
sheets of aluminum.
Just need some time to put it all together into a
set of Shop Notes that speaks to the BIG PICTURE
when it comes to making any heat generating part
perform to design goals. Just understand that the
simple-ideas that support these discussions have
almost nothing to do with the additional cost
of a Schottky versus silicon-junction rectifiers.
Bob . . .
| - The Matronics AeroElectric-List Email Forum - | | Use the List Feature Navigator to browse the many List utilities available such as the Email Subscriptions page, Archive Search & Download, 7-Day Browse, Chat, FAQ, Photoshare, and much more:
http://www.matronics.com/Navigator?AeroElectric-List |
|
|
|
Back to top |
|
 |
info(at)mtfind.com Guest
|
Posted: Sat Jul 05, 2008 7:08 pm Post subject: Bridge diodes VS Schottky |
|
|
WOW Bob, Its my turn to point out you have misunderstood my points in a few
cases
For example
sniped to shorten the post
Quote: | . . . you've mis-interpreted the discussions. Nobody from
this side of the list-server has ever shouted at anyone . . .
|
Not you, but others have suggested there is no point to Eric's
recommendation, Shout is my opinion perhaps not yours. Shouting down is in
my opinion a series of comments indicating that Eric's suggestion was not
needed along with suggested Bridge diode Vf well below worst case values
which may not be repeatable by other builders. Its important to go much
farther in parts selection, even suggestions years old. Bridge diodes were
useful back in the days of single battery and e bus loads of 2-3 amps. Its
important to update and or put real limits on the use of Bridge diodes. Most
thought the Bridge diode was a 25 amp diode until Eric pointed out it was
really a 12.5 amp diode. Further showing two in parallel is understood to
non electrical engineers as splitting the current which is better? right
Quote: | Exactly! The superior performance of the Schottky diode is
not and never has been in question. What WAS in question was
the offering of an alternative to the lowly silicon rectifier
with equal dearth of data to support the promotion of a part
that was more expensive, had to be acquired from a source perhaps
less convenient than Radio Shack and was no easier to install.
|
Quote: | Further, this had nothing to do with me, B&C or even Radio Shack
making a buck on the occasional sale of a bridge rectifier. When
the "new and improved" product came to the market, the lack of
data left many folks who already had bridge rectifiers installed
wondering if they'd done a bad thing . . . "Gee, should I rip it
out and put in the really good part?"
|
The Schottky diode has decades of industry wide documentation in support of
its superior performance and the diode bridge is simply not used in any
recent design application for DC circuit controlling as we use it in your
excellent application suggestions. Further I never suggested or implied
anyone was making a buck on any part ever! Where did that comment come
from??? As for should I rip it out? Without more information such as heat
loss, battery charging etc the answer is maybe it depends. PS the new and
improved product existed in the 1980's Also my local RS store does not carry
these parts.
Today's circuits include battery charging as several posters have mentioned,
another had stated his bus load was 8 amps and the bridge recommended
attached to a simple bracket is not a good solution at higher currents. As
many have clearly interpreted the recommended bridge it will not meet these
design goals.
Quote: | >15 years ago I selected the Schottky diode as I had dual batteries and
>wanted to use the diode to provide battery isolation and and also single
>source battery charging. The bridge diode simply would not charge the
>battery to full charge while the Schottky did.
|
Quote: | One COULD quibble over what the design goals for achieving "full
charge".
Clearly, if you have say 24 hours to wait, 13.8 volts will top off a
room
temperature lead-acid battery of any pedigree . . . but as a practical
matter, we'd like to get our ship's battery topped off in the first few
minutes of flight and under variety of temperatures. So we force the
battery to suffer acceptable indignities by boosting the bus voltage
under a perfectly rational idea that the goal is to store energy to
meet design goals . . . not squeeze a few extra flights of service
life out of a battery that is difficult to qualify. But yes, if one
chooses to go the diode isolator route for batteries, the Schottky
device offers a demonstrable advantage over silicon junction
rectifiers. I'll point out further that your design goals for
incorporation of a diode were decidedly different than for normal
feed path steering of the e-bus power.
|
True but as above many current list builders use the diode to charge the
battery. Setting the alternator to 14.3V will not, in a reasonable time,
charge a backup battery as the bridge Vf can reach nearly 1 volt leaving the
battery terminal voltage around 13.3 V which is below a reasonable voltage
for charging. Further if the battery is really discharged the charging
current is likely to exceed the allowable bridge maximum current.
I recall the delta V to charge a battery is 0.2V per cell at room temp. This
amounts to 1.2V for a 12V battery. Thus 13.3V charging V will eventually
charge the battery to 12.1V hardly adequate!
Quote: | >Data sheet worst case design analysis can be difficult as the typical data
>sheet is intended to make the part look good and typically shows
>information that is at least misleading with the real worst case
>information hard to find.
Shucks . . . you're not suppose to say that in front of
everybody!!! Yes, unless one makes a living at the
interpretation, validation and application of manufacture's
data sheets, it CAN be a daunting and sometimes frustrating
task. We had some pretty good discussions here on the List
a few years back when curves for guaranteed performance
on breakers was misinterpreted as LIMITS to performance.
|
Only by exceeding the specified data sheet parameters. The data sheet
specifications are safe guaranteed LIMITS used in proper and safe design.
Yes in some cases the actual part as being made at the time can exceed these
limits safely but as that discussion went, there are many different mfgrs
making equivalent CB and now many are made overseas to questionable
standards. The extrapolation of data sheet parameters or using data sheet
parameters from one mfgr and assume other mfgrs parts will meet these
parameters is not permitted in aerospace industry. Further there is no
reason to exceed data sheet parameters in a good design. As I recall your
example was assumed by many to simply justify an omission of a simple
current limiting resistor that would have safely limited the current in the
CB and not detracted in anyway the overall CB function but that is a
distraction to today's topic.
Yes data sheets tend to mislead to get a slaes advantage. One part is stated
to have a max current of 200 amps while there is a not to a n app sheey that
limits that same part to 75 amos due to the die to case bond wires. Most
specify parameters at 25C where in any real world the temp is much higher
with any reasonable heat sink.
Quote: | As a designer with decades of experience of working with
those breakers (knowing about their demonstrated capabilities
outside the guaranteed performance), I was able to
exploit their capabilities in ways that got some folks
really excited . . . for no good reason based on the physics.
|
I understand the widespread of use of parts outside their design because one
can usually get away with it. This is a poor excuse for proper design and
again simply not allowed in aerospace where it must work with any part from
any approved mfgr. In the above example there is no need to extrapolate as
the addition of a simple series resistor will limit the current to
specification values and not detract with the designs purpose or function.
Quote: | >Today the bridge diode part is very old and many manufacturers have
>shortened the data sheet to the extent its not possible to determine the
>worst case parameters. Some data sheets are simply scans from another
>Manufacturer's old data sheet.
>
>I evaluated both types of bridge diodes available today. The GBPC series
>and the older MB series. The MB series has a metal base with metal sides.
>The GBPC series has a smaller metal base and no metal sides. The
>electrical parameters are essentially the same and both are available with
>faston type connections. Remember some data is shown as nominal, not max
>ratings. Remember that bridge diodes are rated as a full wave rectifier
>which means some data must be converted to DC.
>
>Here are the worst case values for Vf at 1 and 10 amps and at 25C and
>150C. This is for a single diode.
>Note the data is basically a straight line from 1A to 10A which allows for
>simple intermediate current calculations
>
>Vf 1A 25C Vf 10A 25C Vf 1A 150C Vf 10A 150C
>0.83V 1.05V 0.63V 0.85V
>
>Power dissipation as follows at 25C
>1A 2.5A 5.0A 7.5A 10A
>0.83W 2.23W 4.7W 7.5W 10.5W
>
>To figure case temp consider 1.9deg/c per watt from die temp. For example
>case temp max at 10 amps is 10.5 times 1.9 approx 20C or 130C max. If
>ambient temp is 40C near the mount then the heat sink must dissipate 10.5W
>with a temp drop of 90C across the heatsink.
|
Quote: | Exactly. And that works out to a heatsink with about 8.5C/Watt
thermal resistance which is NOT a very big heatsink.
|
Not sure I agree and clearly at least a couple of bridge mfgrs disagree as
they specify (to me) a large heatsink as noted elsewhere. However each case
of mounting location etc is different and one needs to make a worst case
heat sink or do the design specific analysis. Thermal resistance is
different mounted behind the engine vs. mounted behind the panel vs. mounted
behind the baggage. Also today some aircr4qaft fly well above 20,000 where
convection transfer is much lower.
Quote: | >The above does not allow for the case to heat sink temp resistance
>depending on heat sinking surface material IE grease. The above does not
>allow for service derating. The aerospace industry recommends no more that
>100C case temp which increases the heat sink size for a temp gradient of
>from 90 to 60 c max
>
>Its clear that above a current of 1A, some (or a lot of) heat sink is
>required. I do not recall any specified requirement other than to simply
>mount it on a small bracket.
|
Quote: | Hmmmm . . . don't know about "small bracket" . . . . I've
suggested any flat surface of aircraft sheet metal which is
generally a firewall, shelf or perhaps skin.
|
Most firewalls are or should be SS and that is a very poor heatsink The skin
is better but no mention of the need for heat sink grease used on the
bracket to bridge and bracket to skin etc. Many skins are also very thin
relative to normal heat sinks leading to high thermal resistance.
Quote: | > No mention of the surface smoothness of the bracket nor what it's
> thickness or size is. No mention of the required heat sink grease etc. At
> 10 amps a couple of manufacturers require a heat sink size of 6" x 2.2" x
> 2.2" finned plate plus additional requirements to keep the junction
> temperature below 150C (the max rated temperature). To calculate case
> temp use 1.9deg/c per watt from die temp. For example case temp max at 10
> amps is 10.5 times 1.9 approx 20C or 130C max.
>
>Thus its not wrong to state a 10W heat sink is needed but there is a
>string of calculations required to determine the physical heat sink
>needed.
But the
short story is that suggesting a builder use a heatsink rated
for 10W is not the whole story.
|
I agree but my point is that is the start of the analysis along with the
delta T across the heat sink
Quote: | >Now lets look at the current Schottky diode available. In this case the
>diode selected is the DSS2x121-0045B made by IXYS. Two independent 120 amp
>diodes. In the case of Schottky diodes the higher the current rating the
>lower the Vf at low currents as seen in this application. IR used to be
>the low Vf leader but this IXYS is slightly better and lower cost and easy
>to get. ( www.findchips.com )
>
>Vf 1A 25C Vf 10A 25C Vf 1A 150C Vf 10A 150C
>0.29V 0.34A 0.15V 0.24V
>
>Power dissipation as follows at 25C
>1A 2.5A 5.0A 7.5A 10A
>0.29W 0.78W 1.58W 2.48W 3.40W
>
>Clearly a far better part to use. Just as easy to mount and wiring support
>is easier.
>
>If battery charging is intended thru this diode, not only is a full charge
>possible but there is no current overload as is likely to occur with the
>bridge if the battery being charged is significantly discharged and where
>the charging current can be well above 10 amps.
Absolutely. I've seen several battery powered systems
fall short of design goals because the folks forgot that
a battery intended to supply perhaps 5-10 amps in use
can DRAW several times that current while being recharged.
|
Yes but posts stating the use of the bridge as a trickle charger were not
challenged as not safe with the bridge diode.
Quote: | >Why worst case analysis? Because its not possible to know the actual
>parameters of the parts used by the various builders. Manufacturers do
>produce worst case parts and are often sold to resellers like RS with the
>higher quality parts are distributed to the industry market.
Do you have some reference to support this? In years gone
by there have been countless suppliers of parts to the
hobby electronics market that indeed offered "floor sweepings"
in bags. I discovered the photo-sensitivity of junction
transistors when devices I'd purchased as "2N3904" transistors
had a terrible amount of hum that disappeared when the florescent
light over the bench was shut off. The plastic was not quite
as opaque as one might wish for a "real" 2N3904.
|
I am not talking about out of spec parts. Worst case but meeting
specification. Today parts are generally automatically tested and binned
based on performance and selected and sold at a higher price to
manufacturers.
Quote: | However, the real cost of good parts has become so small
compared to all the other costs of distributing and marketing
that there is little value in spending labor to create a
separate product stream for sub-standard parts. Further, the
idea that sub-standard parts is even exist is suspect. Modern
semiconductor houses have so many process checks in place along
the assembly line that sub-standard parts are going to be
pitched long before they're put into final packages and marked
with the manufacturer's brand and part-number.
|
I never stated sub standard parts I did say parts that were worst case which
in this discussion had the max Vf for example. See comment just above your
reply There is no special labor today, its 99% automated today. A given
production run generally has a very tight distribution. Thus one run may
produce 99% parts that are within 1% of max and another run may produce most
parts that are 25% better than max. The better parts are often selected for
higher performance requirements.
There is a HUGE problem with remarked and parts made with different Die
current plaguing the industry. Its bit even major manufacturers. This is a
wide spread discussion in industry pubs this year and its apparently getting
to be a larger issue as more and more parts are sub standard or not even the
correct die inside.
Quote: | >Why not just do a test and use that as proof of the design? A test only
>proves the worst case analysis is valid and is only good for the exact
>parts used and does not indicate what results will be with similar parts
>from the identical manufacturers production batch. Proper engineering
>design always starts with a worst case analysis of the design followed
>with a test to show the results are inside the worst case analysis. Only
>then is the design released for production or in this case released for
>the general builder to build and be sure it will perform to expectations.
>
>Availability? Its strange to me that the availability of the bridge at RS
>is promoted but many of the recommended switches are only available thru
>B&C.
I "promote" selection of parts adequate to the task
with some notion of $time$ expended to acquire those
parts. A $1.50 switch from the store is no bargain
if you hop in the car and drive 7 miles to buy it . . .
while saving your $5.00 switch in the drawer for a
"more demanding" task.
|
My point is there are special contact/switching configurations not normally
available anywhere to the normal builder other than you then, and now B&C. I
would suggest you consider electrical redesign and restrict the switches to
the commonly available contact configurations. Not all builders want to use
large bat handle toggles but other style switches are not available in the
special contact configurations..
Quote: | The part numbers cited in my drawings are artifacts
of the catalog numbers I assigned to those parts
while I was supplying them to the OBAM aviation
industry. When I decided to move that activity to
B&C . . . many of those numbers were retained and
are most often cited in my work much of which dates
back 20 years.
However, I've never attempted to hide the fact that
there are MANY alternate sources for equal or even
better parts if the builder has the willingness,
I submit that the parts I've oft suggested are an
aid for those who believe their time is better spent
bucking in a few more perfect rivets and bending
one more ideal stiffener. This is opposed to combing
the 'Net' in some attempt to save a few dollars on parts
selection when their personal expertise is orthodontics
or managing a grocery store.
|
My point was specific towards some of you specified switches that simply are
not stocked or made in other mechanical configurations. I know as I have
looked for myself and others who wanted to use that specification switching
function but not the large bat handle actuator.
Quote: | >Modern electronics use switching supplies which use more or less power not
>amps as input baded on input voltage. Thus the higher the Vf the more amps
>required and thus shorter battery life as the battery life in amp hours
>goes down as the amp drain goes up.
>
>The cost of the superior Schottky part is very small compared to the cost
>of the electrical wiring/terminal etc system and insignificant to the
>total cost of the aircraft.
This discussion has never been about cost of parts.
It has always been about selection of parts adequate
to the design goals with the minimum total expenditure
of $time$ to select, acquire, install, and maintain
those parts.
|
I only pointed out there is no significant cost difference in the big
picture and there is significant performance improvements to many builders.
Today the cost of part acquation using the internet is lower cost that a
auto trip to RS. Mouser is a good source for example and they will special
order if the mfgr makes it. Shipping now is lower cost than auto gas and in
many cases the internet delivers a no sales tax order.
Quote: | In situations where the design goals were changed
(like battery isolation, and boss-hog e-bus loads)
then some re-evaluation of suggested parts is in
order. I've take data in the chamber on a variety
of diodes, done the stress tests to ascertain thermal
resistance of the parts and done all the photographs.
Measured the practical thermal resistance of small
sheets of aluminum.
|
The problem with testing parts is the testing does not prove equivalent
parts will perform the same way. Testing in the aerospace industry is only
done as a proof of concept and only after a detailed design. Then the design
analysis NOT the test results are used for production. Repeatable testing is
only a valid statement using the exact same parts over and over.
The design requirements have changed and its been several years since I
noticed battery charging and higher e bus currents on your group or in the
"book". It would have been helpful had there been some original limits
defined in the "Book" regarding the use of bridge diodes as one example
Quote: | Just need some time to put it all together into a
set of Shop Notes that speaks to the BIG PICTURE
when it comes to making any heat generating part
perform to design goals. Just understand that the
simple-ideas that support these discussions have
almost nothing to do with the additional cost
of a Schottky versus silicon-junction rectifiers.
|
I agree and that is why I never have considered bridge diodes since years
ago far better Schottky diodes were available. In my example I illustrated
the best currently available schottky, much lower cost schottky diodes are
also available if one only wants double the performance. Today and 15 years
power Schottky diodes were available that were insulated bolt down.
You are doing an incredible job helping the masses, but you seem to over
react to comments that intend to improve and or update the design. There are
many of us with knowledge of more modern parts that in our opinion a large
improvement to your evolving designs
Paul
| - The Matronics AeroElectric-List Email Forum - | | Use the List Feature Navigator to browse the many List utilities available such as the Email Subscriptions page, Archive Search & Download, 7-Day Browse, Chat, FAQ, Photoshare, and much more:
http://www.matronics.com/Navigator?AeroElectric-List |
|
|
|
Back to top |
|
 |
nuckolls.bob(at)cox.net Guest
|
Posted: Sun Jul 06, 2008 8:24 am Post subject: Bridge diodes VS Schottky |
|
|
At 08:03 PM 7/5/2008 -0700, you wrote:
Quote: |
WOW Bob, Its my turn to point out you have misunderstood my points in a few
cases
For example
sniped to shorten the post
> . . . you've mis-interpreted the discussions. Nobody from
> this side of the list-server has ever shouted at anyone . . .
Not you, but others have suggested there is no point to Eric's
recommendation, Shout is my opinion perhaps not yours. Shouting down is in
my opinion a series of comments indicating that Eric's suggestion was not
needed along with suggested Bridge diode Vf well below worst case values
which may not be repeatable by other builders. Its important to go much
farther in parts selection, even suggestions years old. Bridge diodes were
useful back in the days of single battery and e bus loads of 2-3 amps. Its
important to update and or put real limits on the use of Bridge diodes. Most
thought the Bridge diode was a 25 amp diode until Eric pointed out it was
really a 12.5 amp diode. Further showing two in parallel is understood to
non electrical engineers as splitting the current which is better? right
|
'Better' needs to be quantified under the design goals. My
studies to be published soon show that the lowly bridge is
just fine as an e-bus feeder up to and including Z-13/8 with
an 8A continuous e-bus load and is not at risk of failure
for transient loads of 2x that amount.
Quote: | > Exactly! The superior performance of the Schottky diode is
> not and never has been in question. What WAS in question was
> the offering of an alternative to the lowly silicon rectifier
> with equal dearth of data to support the promotion of a part
> that was more expensive, had to be acquired from a source perhaps
> less convenient than Radio Shack and was no easier to install.
> Further, this had nothing to do with me, B&C or even Radio Shack
> making a buck on the occasional sale of a bridge rectifier. When
> the "new and improved" product came to the market, the lack of
> data left many folks who already had bridge rectifiers installed
> wondering if they'd done a bad thing . . . "Gee, should I rip it
> out and put in the really good part?"
The Schottky diode has decades of industry wide documentation in support of
its superior performance and the diode bridge is simply not used in any
recent design application for DC circuit controlling as we use it in your
excellent application suggestions. Further I never suggested or implied
anyone was making a buck on any part ever! Where did that comment come
from???
|
Forgive me. There seemed to be a question about the 'narrowness
of suggested parts' when only AEC/B&C catalog numbers were cited
in the documentation and writings on the website.
Quote: | As for should I rip it out? Without more information such as heat
loss, battery charging etc the answer is maybe it depends. PS the new and
improved product existed in the 1980's Also my local RS store does not carry
these parts.
Today's circuits include battery charging as several posters have mentioned,
another had stated his bus load was 8 amps and the bridge recommended
attached to a simple bracket is not a good solution at higher currents. As
many have clearly interpreted the recommended bridge it will not meet these
design goals.
|
The data will tell . . .
<snip>
Quote: | > One COULD quibble over what the design goals for achieving "full charge".
> Clearly, if you have say 24 hours to wait, 13.8 volts will top off a room
> temperature lead-acid battery of any pedigree . . . but as a practical
> matter, we'd like to get our ship's battery topped off in the first few
> minutes of flight and under variety of temperatures. So we force the
> battery to suffer acceptable indignities by boosting the bus voltage
> under a perfectly rational idea that the goal is to store energy to
> meet design goals . . . not squeeze a few extra flights of service
> life out of a battery that is difficult to qualify. But yes, if one
> chooses to go the diode isolator route for batteries, the Schottky
> device offers a demonstrable advantage over silicon junction
> rectifiers. I'll point out further that your design goals for
> incorporation of a diode were decidedly different than for normal
> feed path steering of the e-bus power.
True but as above many current list builders use the diode to charge the
battery. Setting the alternator to 14.3V will not, in a reasonable time,
charge a backup battery as the bridge Vf can reach nearly 1 volt leaving the
battery terminal voltage around 13.3 V which is below a reasonable voltage
for charging. Further if the battery is really discharged the charging
current is likely to exceed the allowable bridge maximum current.
I recall the delta V to charge a battery is 0.2V per cell at room temp. This
amounts to 1.2V for a 12V battery. Thus 13.3V charging V will eventually
charge the battery to 12.1V hardly adequate!
|
No argument. This is why I've never recommended diodes for
battery isolation in favor of the lowly relay or switch
that eliminates this design issue.
<snip>
Quote: | > As a designer with decades of experience of working with
> those breakers (knowing about their demonstrated capabilities
> outside the guaranteed performance), I was able to
> exploit their capabilities in ways that got some folks
> really excited . . . for no good reason based on the physics.
I understand the widespread of use of parts outside their design because one
can usually get away with it. This is a poor excuse for proper design and
again simply not allowed in aerospace where it must work with any part from
any approved mfgr. In the above example there is no need to extrapolate as
the addition of a simple series resistor will limit the current to
specification values and not detract with the designs purpose or function.
|
No, I was "getting away" with nothing. I pointed out that
the parts in question were specified and tested to military
qualification standards that included test point that
lay far outside the bounds of the envelopes published in
the catalog data. Adding the resistor was only not
necessary, it degraded performance of the design in allowing
the ov condition to achieve higher magnitude for longer
periods of time. This WAS cleared by the manufacturers
of said devices and qualified under the watchful eyes of
my DERs and has been flying successfully on thousands of
TC and OBAM aircraft for over 20 years
<snip>
Quote: | > Exactly. And that works out to a heatsink with about 8.5C/Watt
> thermal resistance which is NOT a very big heatsink.
Not sure I agree and clearly at least a couple of bridge mfgrs disagree as
they specify (to me) a large heatsink as noted elsewhere. However each case
of mounting location etc is different and one needs to make a worst case
heat sink or do the design specific analysis. Thermal resistance is
different mounted behind the engine vs. mounted behind the panel vs. mounted
behind the baggage. Also today some aircr4qaft fly well above 20,000 where
convection transfer is much lower.
|
Don't know of many OBAM aircraft that fly at these heights . . . and
those folks are not interested in Z-13/8. As my Shop Notes will
show, there is plenty of headroom for cooling for 1/4 of the
common bridge rectifier by simply mounting it to an existing
surface of the airplane's structure. Certainly not a "small
bracket".
Quote: | > Hmmmm . . . don't know about "small bracket" . . . . I've
> suggested any flat surface of aircraft sheet metal which is
> generally a firewall, shelf or perhaps skin.
Most firewalls are or should be SS and that is a very poor heatsink The skin
is better but no mention of the need for heat sink grease used on the
bracket to bridge and bracket to skin etc. Many skins are also very thin
relative to normal heat sinks leading to high thermal resistance.
|
True. We'll down to the simple ideas and how they fit
together shortly.
<snip>
Quote: | > Absolutely. I've seen several battery powered systems
> fall short of design goals because the folks forgot that
> a battery intended to supply perhaps 5-10 amps in use
> can DRAW several times that current while being recharged.
Yes but posts stating the use of the bridge as a trickle charger were not
challenged as not safe with the bridge diode.
|
Don't know about "trickle charging" . . . that's a exceedingly
vaporous term. Battery isolation for the purpose of preventing
reverse flow of battery energy into the charging source is
not a "trickle charge" and as you've noted, requires further
attention to details.
Quote: | >>Why worst case analysis? Because its not possible to know the actual
>>parameters of the parts used by the various builders. Manufacturers do
>>produce worst case parts and are often sold to resellers like RS with
>>the higher quality parts are distributed to the industry market.
>
> Do you have some reference to support this? In years gone
> by there have been countless suppliers of parts to the
> hobby electronics market that indeed offered "floor sweepings"
> in bags. I discovered the photo-sensitivity of junction
> transistors when devices I'd purchased as "2N3904" transistors
> had a terrible amount of hum that disappeared when the florescent
> light over the bench was shut off. The plastic was not quite
> as opaque as one might wish for a "real" 2N3904.
I am not talking about out of spec parts. Worst case but meeting
specification. Today parts are generally automatically tested and binned
based on performance and selected and sold at a higher price to
manufacturers.
|
???? Okay. So when I purchased a device from Radio Shack with
Fairchild's brand and part number on it, what concerns needed
to be assuaged?
Quote: | > However, the real cost of good parts has become so small
> compared to all the other costs of distributing and marketing
> that there is little value in spending labor to create a
> separate product stream for sub-standard parts. Further, the
> idea that sub-standard parts is even exist is suspect. Modern
> semiconductor houses have so many process checks in place along
> the assembly line that sub-standard parts are going to be
> pitched long before they're put into final packages and marked
> with the manufacturer's brand and part-number.
I never stated sub standard parts I did say parts that were worst case which
in this discussion had the max Vf for example. See comment just above your
reply There is no special labor today, its 99% automated today. A given
production run generally has a very tight distribution. Thus one run may
produce 99% parts that are within 1% of max and another run may produce most
parts that are 25% better than max. The better parts are often selected for
higher performance requirements.
|
But once branded, date coded and identified as to part number,
of what value is any discussion on production line yields?
Quote: | There is a HUGE problem with remarked and parts made with different Die
current plaguing the industry. Its bit even major manufacturers. This is a
wide spread discussion in industry pubs this year and its apparently getting
to be a larger issue as more and more parts are sub standard or not even the
correct die inside.
|
But you can buy a bogus part from anybody, why pick on Radio Shack?
<snip>
Quote: | >>Availability? Its strange to me that the availability of the bridge at
>>RS is promoted but many of the recommended switches are only available
>>thru B&C.
>
> I "promote" selection of parts adequate to the task
> with some notion of $time$ expended to acquire those
> parts. A $1.50 switch from the store is no bargain
> if you hop in the car and drive 7 miles to buy it . . .
> while saving your $5.00 switch in the drawer for a
> "more demanding" task.
My point is there are special contact/switching configurations not normally
available anywhere to the normal builder other than you then, and now B&C. I
would suggest you consider electrical redesign and restrict the switches to
the commonly available contact configurations. Not all builders want to use
large bat handle toggles but other style switches are not available in the
special contact configurations..
|
Whoa! I am not in the business of specifying any parts
to anybody. This is the OBAM aircraft community we're
writing for here. Our mission as teachers and mentors
is to GUIDE the neophyte builder in crafting a failure
tolerant system with the lowest cost of ownership. If
we do our jobs well, it matters not if the switches
are Honeywell or O'Rilley autoparts.
<snip>
Quote: | My point was specific towards some of you specified switches that simply are
not stocked or made in other mechanical configurations. I know as I have
looked for myself and others who wanted to use that specification switching
function but not the large bat handle actuator.
|
Cite examples. I believe all the parts called out on my drawings
and in my writings are offered by B&C in Carling toggles at attractive
prices. It is beyond the scope of my mission to throw a wide net
into the switch marketplace with some idea that I'll cover the
design goals of all builders.
<snip>
Quote: | > This discussion has never been about cost of parts.
> It has always been about selection of parts adequate
> to the design goals with the minimum total expenditure
> of $time$ to select, acquire, install, and maintain
> those parts.
I only pointed out there is no significant cost difference in the big
picture and there is significant performance improvements to many builders.
Today the cost of part acquation using the internet is lower cost that a
auto trip to RS. Mouser is a good source for example and they will special
order if the mfgr makes it. Shipping now is lower cost than auto gas and in
many cases the internet delivers a no sales tax order.
|
No argument. And if you have specific recommendations to
make to any builder with respect to the selection and
procurement of any part, this List-Server is the place
to make that knowledge known. But please be specific
and support it with your deductions based on the simple-
ideas (physics, style, cost-of-ownership, preferences,
etc.) But to get out a broad brush and painting this
Shottkey vs. Silcon discussion with yet another color
is not productive.
Quote: | > In situations where the design goals were changed
> (like battery isolation, and boss-hog e-bus loads)
> then some re-evaluation of suggested parts is in
> order. I've take data in the chamber on a variety
> of diodes, done the stress tests to ascertain thermal
> resistance of the parts and done all the photographs.
> Measured the practical thermal resistance of small
> sheets of aluminum.
The problem with testing parts is the testing does not prove equivalent
parts will perform the same way. Testing in the aerospace industry is only
done as a proof of concept and only after a detailed design. Then the design
analysis NOT the test results are used for production. Repeatable testing is
only a valid statement using the exact same parts over and over.
The design requirements have changed and its been several years since I
noticed battery charging and higher e bus currents on your group or in the
"book". It would have been helpful had there been some original limits
defined in the "Book" regarding the use of bridge diodes as one example
|
You're making this MUCH more complicated than it needs
to be. This "worst case" canard has been tossed into
the List discussions many times over the years. I object
to and will vigorously resist the notion that we should
take cues from Boeing or NASA in the studies surrounding
the selection and application of parts.
We are not building revenue generating machines or spacecraft.
FAILURE TOLERANCE is the design goal. Our demands on
part reliability is in a totally different world from
the "big guys". We can and should ASSUME that every
part we install is going to fail at some point in time.
For folks who are following this thread, I'll refer them
to a series of 7 articles on the website that pop up under
a search for "failure tolerance". We can write volumes
of esoteric discussion on worst case, fault trees,
and 10 to the minus bizillion failure rates. This is
the mind-set that has driven the cost of a C-172 totally
out of reach for most folks who would like to own
an airplane . . . In the OBAM aircraft community
we can toss all that bilge in favor of building
systems that are not unsafe in spite of failures.
Failures that are easy to upgrade as needed so
that they don't repeat.
<snip>
Quote: | > Just need some time to put it all together into a
> set of Shop Notes that speaks to the BIG PICTURE
> when it comes to making any heat generating part
> perform to design goals. Just understand that the
> simple-ideas that support these discussions have
> almost nothing to do with the additional cost
> of a Schottky versus silicon-junction rectifiers.
I agree and that is why I never have considered bridge diodes since years
ago far better Schottky diodes were available. In my example I illustrated
the best currently available schottky, much lower cost schottky diodes are
also available if one only wants double the performance. Today and 15 years
power Schottky diodes were available that were insulated bolt down.
|
. . . that was your well considered choice. I believe we've
done the best we know how to do in framing the discussion
so that it benefits our readers more than it confuses them.
Quote: | You are doing an incredible job helping the masses, but you seem to over
react to comments that intend to improve and or update the design. There are
many of us with knowledge of more modern parts that in our opinion a large
improvement to your evolving designs
|
Thank you.
I don't think I over react . . . I'm always for value-added
"updates" and "improvements" but sometimes the best way
to drive a nail is with a hammer. Now, if you need to make
a living by the using thousands of nails per day,
a nail-gun or even an automatic machine is called for
as a means by which $time$ is better utilized. All
of our OBAM aircraft brothers have hammers.
My shop walls are covered in drawers and bins and
drawers . . .
http://aeroelectric.com/Pictures/Misc/Shop.jpg
http://aeroelectric.com/Pictures/Misc/Shop_1.jpg
http://aeroelectric.com/Pictures/Misc/Shop_2.jpg
in those drawers you'll find parts I've had for 40
years . . . and micro-processors and non-contact
magnetic rotary position sensors that are the latest that
the industry has to offer.
Any of those parts may find their way into a recipe for
success if found adequate to the task. Things are
not updated for the sake of being the "most improved"
especially if failure tolerant design makes the
investment of $time$ to improve problematic and
arbitrarily shuts out some economical sources of
supply.
Thank you for your $time$ and insight participating
in this discussion. It has been useful for me and
no doubt for some of our readers.
Bob . . .
| - The Matronics AeroElectric-List Email Forum - | | Use the List Feature Navigator to browse the many List utilities available such as the Email Subscriptions page, Archive Search & Download, 7-Day Browse, Chat, FAQ, Photoshare, and much more:
http://www.matronics.com/Navigator?AeroElectric-List |
|
|
|
Back to top |
|
 |
info(at)mtfind.com Guest
|
Posted: Sun Jul 06, 2008 10:01 am Post subject: Bridge diodes VS Schottky |
|
|
Thanks for your time. I think we must disagree and let it go at that.
Paul
---
| - The Matronics AeroElectric-List Email Forum - | | Use the List Feature Navigator to browse the many List utilities available such as the Email Subscriptions page, Archive Search & Download, 7-Day Browse, Chat, FAQ, Photoshare, and much more:
http://www.matronics.com/Navigator?AeroElectric-List |
|
|
|
Back to top |
|
 |
longg(at)pjm.com Guest
|
Posted: Mon Jul 14, 2008 5:21 am Post subject: Bridge diodes VS Schottky |
|
|
I have never understood all this squabble about the lowly bridge diode
except to provide more free advertising for the Schottky. I constantly
run 15-20 amps through my bridge diode and except for initial loading,
the temp on the diode isn't enough to warm the legs on a fly. Use the
heat sink and good 10 gauge wire for the short jumpers between the
buses. Since the max limit is 25 Amps (momentary), one may easily
control the load served. I have found not value in spending the big
bucks on the Schottky.
On the other hand my fancy Garmin stack puts out enough heat such to
warrant adding a fan and a plenum to one side with a scat tube to warm
the cabin on fall days.
--
| - The Matronics AeroElectric-List Email Forum - | | Use the List Feature Navigator to browse the many List utilities available such as the Email Subscriptions page, Archive Search & Download, 7-Day Browse, Chat, FAQ, Photoshare, and much more:
http://www.matronics.com/Navigator?AeroElectric-List |
|
|
|
Back to top |
|
 |
nuckolls.bob(at)cox.net Guest
|
Posted: Mon Jul 14, 2008 7:14 am Post subject: Bridge diodes VS Schottky |
|
|
At 09:18 AM 7/14/2008 -0400, you wrote:
Quote: |
I have never understood all this squabble about the lowly bridge diode
except to provide more free advertising for the Schottky. I constantly
run 15-20 amps through my bridge diode and except for initial loading,
the temp on the diode isn't enough to warm the legs on a fly. Use the
heat sink and good 10 gauge wire for the short jumpers between the
buses. Since the max limit is 25 Amps (momentary), one may easily
control the load served. I have found not value in spending the big
bucks on the Schottky.
On the other hand my fancy Garmin stack puts out enough heat such to
warrant adding a fan and a plenum to one side with a scat tube to warm
the cabin on fall days.
|
It's a subtle thing that touches on two issues. One is
voltage drop that goes to performance of downstream appliances.
The other is heat generated from the current voltage drop
product that must be considered with respect to ratings
of the diode in question. I'm working on a comic book that
speaks to the whole thermal management issue and heat sinks
in the electronics business.
For my own purposes, it wasn't an issue of dollars. I
was attracted to the PACKAGES for bridge rectifiers
that made it EASY for the neophyte builder to mount,
wire and heat-sink the device. There's a constellation
of diode products that would do the job electrically
assuming ratings limits are observed in each case.
I welcome any discussion that adds to the collective
knowledge of our readers . . . but object vigorously
when specific products are touted based on poor
to non-existent examination of the details.
I've got nothing against or for Schottky vs. Silicon
Junction devices. I stock and use both. But marketing
hype that exploits the ignorance/fears of potential
customers will continue to be identified for what it
is.
By the way, it's a really good idea to trim the previous
postings from your reply unless you're referencing
specific portions in your response. Helps keep the
archives from being stuffed with repeat data.
Bob . . .
| - The Matronics AeroElectric-List Email Forum - | | Use the List Feature Navigator to browse the many List utilities available such as the Email Subscriptions page, Archive Search & Download, 7-Day Browse, Chat, FAQ, Photoshare, and much more:
http://www.matronics.com/Navigator?AeroElectric-List |
|
|
|
Back to top |
|
 |
henryroden
Joined: 09 Jan 2006 Posts: 13 Location: Albuquerque
|
Posted: Tue Jul 15, 2008 7:55 am Post subject: Bridge Diodes Vs Schottky |
|
|
Thanks Bob, sometimes it is hard to remember where the post started.
Henry
From: "Robert L. Nuckolls, III" <[url=http://webmaila.juno.com/webmail/new/8?folder=Inbox&msgNum=0000GWW0:0018V4zq00001^uH&block=1&msgNature=all&msgStatus=all&count=1216136892&content=central#]nuckolls.bob(at)cox.net[/url]>
Subject: RE: Bridge diodes VS Schottky
At 09:18 AM 7/14/2008 -0400, you wrote:
By the way, it's a really good idea to trim the previous
postings from your reply unless you're referencing
specific portions in your response. Helps keep the
archives from being stuffed with repeat data.
Bob . . .
Do not archive
____________________________________________________________
[url=_blank]Is your computer secure? Get the best Internet Security. Click Here.[/url]
[quote][b]
| - The Matronics AeroElectric-List Email Forum - | | Use the List Feature Navigator to browse the many List utilities available such as the Email Subscriptions page, Archive Search & Download, 7-Day Browse, Chat, FAQ, Photoshare, and much more:
http://www.matronics.com/Navigator?AeroElectric-List |
|
|
|
Back to top |
|
 |
|
|
You cannot post new topics in this forum You cannot reply to topics in this forum You cannot edit your posts in this forum You cannot delete your posts in this forum You cannot vote in polls in this forum You cannot attach files in this forum You can download files in this forum
|
Powered by phpBB © 2001, 2005 phpBB Group
|