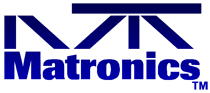 |
Matronics Email Lists Web Forum Interface to the Matronics Email Lists
|
View previous topic :: View next topic |
Author |
Message |
jonlaury
Joined: 06 Nov 2006 Posts: 336
|
Posted: Tue Jul 06, 2010 10:07 am Post subject: Heat Sink necessary? |
|
|
Using a 25a bridge rectifier for dual power sources for EFI. The injectors might pull 10a, worst case. For normal ops, 6a.
Is heat sinking necessary for the rectifer?
Thanks,
J
| - The Matronics AeroElectric-List Email Forum - | | Use the List Feature Navigator to browse the many List utilities available such as the Email Subscriptions page, Archive Search & Download, 7-Day Browse, Chat, FAQ, Photoshare, and much more:
http://www.matronics.com/Navigator?AeroElectric-List |
|
|
|
Back to top |
|
 |
longg(at)pjm.com Guest
|
Posted: Tue Jul 06, 2010 11:14 am Post subject: Heat Sink necessary? |
|
|
Jon,
You are mixing supply and demand (but that's ok). Normally it is
suggested a heat sink be used for a sink load of 20A or more. Since your
hardware is bigger than your load you could try it without. If it is
continuous load you may want to monitor the rectifier temperature to be
sure you're in limits. The manufacturer should publish that.
If you're at all concerned about temperature, just add a heat sink. If
the heat sink sets you back wait till you see the price at the gas pump.
Wow! The poor man's option is to mount it on a piece phenolic block
which you'll find does little for heat dissipation but is virtually
indestructible should your diode take to glowing in flight. You can cut
some grooves in the top of the block to allow air to travel underneath
the rectifier. You can also buy one of those computer fans and a frame
for about a $1.00 to point in the general direction. I have a variety
pack of those stick on thermometers that lets one visualize surface
temps. Could be handy for something like this. Most of this is much more
fuss than just installing the heat sink.
Hey, what kind of injectors pull 10A? I suppose you mean the ignition
module.
Enjoy,
Glenn E. Long
--
| - The Matronics AeroElectric-List Email Forum - | | Use the List Feature Navigator to browse the many List utilities available such as the Email Subscriptions page, Archive Search & Download, 7-Day Browse, Chat, FAQ, Photoshare, and much more:
http://www.matronics.com/Navigator?AeroElectric-List |
|
|
|
Back to top |
|
 |
nuckolls.bob(at)aeroelect Guest
|
Posted: Tue Jul 06, 2010 12:08 pm Post subject: Heat Sink necessary? |
|
|
At 01:07 PM 7/6/2010, you wrote:
Quote: |
Using a 25a bridge rectifier for dual power sources for EFI. The
injectors might pull 10a, worst case. For normal ops, 6a.
Is heat sinking necessary for the rectifer?
|
yes . . . but simply mounting it to a metallic
surface on the airplane will be sufficient.
10A on any one leg of the device will dissipate
about 7 watts of heat that is easily managed by
most metal surface mounting situations.
Doing in-situ temperature measurements on the
molded bridge rectifier is VERY difficult. There's
no thermally integral metal surface available for
sampling. You'd need to bury a tiny-wire thermocouple
in the mounting under the rectifier assembly.
You can measure the temperature of the sheet metal
directly opposite the rectifier and make some
assumptions about thermal resistance of the
mounting . . . but it's more fuss than you'd
probably want to experience. 10A doesn't present
much of a challenge to a device with a metal
heat-sink interface. Use a little 'heat sink'
grease under it when mounting.
http://www.radioshack.com/product/index.jsp?productId=2102858
Bob . . .
| - The Matronics AeroElectric-List Email Forum - | | Use the List Feature Navigator to browse the many List utilities available such as the Email Subscriptions page, Archive Search & Download, 7-Day Browse, Chat, FAQ, Photoshare, and much more:
http://www.matronics.com/Navigator?AeroElectric-List |
|
|
|
Back to top |
|
 |
jonlaury
Joined: 06 Nov 2006 Posts: 336
|
Posted: Wed Jul 07, 2010 8:29 am Post subject: Re: Heat Sink necessary? |
|
|
Glen and Bob, Thanks.
I used a .063 alum washer for a stand-off from my composite structure which allows air to the metal backside of the rectifier. I will add a larger surface area piece of alum w/recommended grease.
The injectors are 55#/hr and my 6 cyl engine, with a bsfc of .55 lbs./hr/hp, will have a max fuel consumption of 132 lbs/hr so these injectors will only see a 40% duty cycle. At 75% they draw 9W each or 54 W, so my normal ops should draw about 2.5 amps. So my initial guess of 6a is too high. The 10 amp circuit recommended by the EFI mfgr is to cover all the bases including low voltage and higher power than my engine makes.
| - The Matronics AeroElectric-List Email Forum - | | Use the List Feature Navigator to browse the many List utilities available such as the Email Subscriptions page, Archive Search & Download, 7-Day Browse, Chat, FAQ, Photoshare, and much more:
http://www.matronics.com/Navigator?AeroElectric-List |
|
|
|
Back to top |
|
 |
nuckolls.bob(at)aeroelect Guest
|
Posted: Wed Jul 07, 2010 8:49 am Post subject: Heat Sink necessary? |
|
|
At 11:29 AM 7/7/2010, you wrote:
Quote: |
Glen and Bob, Thanks.
I used a .063 alum washer for a stand-off from my composite
structure which allows air to the metal backside of the rectifier. I
will add a larger surface area piece of alum w/recommended grease.
|
Okay, recommend something on the order of 10 square inches
of .062 aluminum. If you wanted to make it "tighter" on
real-estate, you could bend the edges up so that the
diode still sits on a flat spot, but the overall width
is reduced.
Quote: | The injectors are 55#/hr and my 6 cyl engine, with a bsfc of .55
lbs./hr/hp, will have a max fuel consumption of 132 lbs/hr so these
injectors will only see a 40% duty cycle. At 75% they draw 9W each
or 54 W, so my normal ops should draw about 2.5 amps. So my initial
guess of 6a is too high. The 10 amp circuit recommended by the EFI
mfgr is to cover all the bases including low voltage and higher
power than my engine makes.
|
Hmmmm . . . maybe you don't need to do anything with
the diode. Wait until you're able to run the engine
and take some measurements of your own. It sounds
like it might be just fine with zero-heat sink.
Bob . . .
| - The Matronics AeroElectric-List Email Forum - | | Use the List Feature Navigator to browse the many List utilities available such as the Email Subscriptions page, Archive Search & Download, 7-Day Browse, Chat, FAQ, Photoshare, and much more:
http://www.matronics.com/Navigator?AeroElectric-List |
|
|
|
Back to top |
|
 |
klehman(at)albedo.net Guest
|
Posted: Wed Jul 07, 2010 2:48 pm Post subject: Heat Sink necessary? |
|
|
It is sometimes good to imagine what can go wrong. Generally high
impedance injectors run around 12 ohms resistance. If one or more
injector driver fails on, the engine will likely keep running unless
subsequently a fuse pops or a diode fails due to the extra current. I'd
consider making sure the diode had some heat sinking and was capable of
feeding all six injectors at 100% duty cycle which is likely 7+ amps at
14+ volts.
Ken
Robert L. Nuckolls, III wrote:
Quote: |
<nuckolls.bob(at)aeroelectric.com>
At 11:29 AM 7/7/2010, you wrote:
>
> <jonlaury(at)impulse.net>
>
> Glen and Bob, Thanks.
>
> I used a .063 alum washer for a stand-off from my composite structure
> which allows air to the metal backside of the rectifier. I will add a
> larger surface area piece of alum w/recommended grease.
Okay, recommend something on the order of 10 square inches
of .062 aluminum. If you wanted to make it "tighter" on
real-estate, you could bend the edges up so that the
diode still sits on a flat spot, but the overall width
is reduced.
> The injectors are 55#/hr and my 6 cyl engine, with a bsfc of .55
> lbs./hr/hp, will have a max fuel consumption of 132 lbs/hr so these
> injectors will only see a 40% duty cycle. At 75% they draw 9W each or
> 54 W, so my normal ops should draw about 2.5 amps. So my initial
> guess of 6a is too high. The 10 amp circuit recommended by the EFI
> mfgr is to cover all the bases including low voltage and higher power
> than my engine makes.
Hmmmm . . . maybe you don't need to do anything with
the diode. Wait until you're able to run the engine
and take some measurements of your own. It sounds
like it might be just fine with zero-heat sink.
Bob . . .
|
| - The Matronics AeroElectric-List Email Forum - | | Use the List Feature Navigator to browse the many List utilities available such as the Email Subscriptions page, Archive Search & Download, 7-Day Browse, Chat, FAQ, Photoshare, and much more:
http://www.matronics.com/Navigator?AeroElectric-List |
|
|
|
Back to top |
|
 |
nuckolls.bob(at)aeroelect Guest
|
Posted: Wed Jul 07, 2010 6:29 pm Post subject: Heat Sink necessary? |
|
|
At 05:47 PM 7/7/2010, you wrote:
Quote: |
It is sometimes good to imagine what can go wrong. Generally high
impedance injectors run around 12 ohms resistance. If one or more
injector driver fails on, the engine will likely keep running unless
subsequently a fuse pops or a diode fails due to the extra current.
I'd consider making sure the diode had some heat sinking and was
capable of feeding all six injectors at 100% duty cycle which is
likely 7+ amps at 14+ volts.
|
Would that not be a multiple failure scenario? . . .
and would the engine run with 5 of the 6 injectors
turned on hard?
Bob . . .
| - The Matronics AeroElectric-List Email Forum - | | Use the List Feature Navigator to browse the many List utilities available such as the Email Subscriptions page, Archive Search & Download, 7-Day Browse, Chat, FAQ, Photoshare, and much more:
http://www.matronics.com/Navigator?AeroElectric-List |
|
|
|
Back to top |
|
 |
klehman(at)albedo.net Guest
|
Posted: Thu Jul 08, 2010 3:37 am Post subject: Heat Sink necessary? |
|
|
Normally injectors are sized such that full on only represents about 30%
extra fuel over full power. (sized primarily to give better idle
control) So yes in most cases an engine will run at aircraft cruise
power or higher with all injectors locked full on. I would consider one
or more locked on injectors a single failure. Older ecu's batch fire
injectors and share drivers. But yes you'd need to go into ecu and
wiring specifics to determine whether a single failure could lock more
than one injector on. 100% extra fuel (twice normal flow) on my subaru
makes the exhaust system quite hot but does not stop the engine. Rare
but injectors do occasionally fail on. A minor concern admittedly.
Similarly for multiple coil ignitions. Rare but I've seen single coils
short out internally and draw continuous current. I'm just suggesting
that some headroom or safety margin in the sizing and fusing of such
circuits is a good idea and that would include any diodes.
Ken
Robert L. Nuckolls, III wrote:
Quote: |
<nuckolls.bob(at)aeroelectric.com>
At 05:47 PM 7/7/2010, you wrote:
>
>
> It is sometimes good to imagine what can go wrong. Generally high
> impedance injectors run around 12 ohms resistance. If one or more
> injector driver fails on, the engine will likely keep running unless
> subsequently a fuse pops or a diode fails due to the extra current.
> I'd consider making sure the diode had some heat sinking and was
> capable of feeding all six injectors at 100% duty cycle which is
> likely 7+ amps at 14+ volts.
Would that not be a multiple failure scenario? . . .
and would the engine run with 5 of the 6 injectors
turned on hard?
Bob . . .
|
| - The Matronics AeroElectric-List Email Forum - | | Use the List Feature Navigator to browse the many List utilities available such as the Email Subscriptions page, Archive Search & Download, 7-Day Browse, Chat, FAQ, Photoshare, and much more:
http://www.matronics.com/Navigator?AeroElectric-List |
|
|
|
Back to top |
|
 |
jonlaury
Joined: 06 Nov 2006 Posts: 336
|
Posted: Thu Jul 08, 2010 6:37 am Post subject: Re: Heat Sink necessary? |
|
|
Ken,
Thank you for your illumination of some issues surrounding EFI. The Simple Digital Systems EFI is the one I'm using. Your comments have explained why SDS said that I might want to consider using a 15 amp circuit. It never made sense to me until I read your comments about sizing for all 6 injectors locking on (100% duty cycle). The bridge diode that I'm using is rated for 25a (at) 200v so there seems to be sufficient headroom.
My injectors are low impedance type and SDS supplies a 3 x 4 x 1/8" aluminum piece with 3 gold anodized resistors??(I'm guessing) that have fins radiating around them. Installation instructions say this piece can get "quite hot at higher duty cycles".
It seems that the SDS EFI 'wants' to have high impedance injectors. Are there advantages to a high impedance architecture?
John
| - The Matronics AeroElectric-List Email Forum - | | Use the List Feature Navigator to browse the many List utilities available such as the Email Subscriptions page, Archive Search & Download, 7-Day Browse, Chat, FAQ, Photoshare, and much more:
http://www.matronics.com/Navigator?AeroElectric-List |
|
|
|
Back to top |
|
 |
klehman(at)albedo.net Guest
|
Posted: Thu Jul 08, 2010 12:46 pm Post subject: Heat Sink necessary? |
|
|
John
Port injectors are usually high impedance and they are by far the most
common injector. They simplify control issues and drive circuits and are
the only ones that I've played with. Suitable mosfet (transistor)
switches are very cheap and don't have large heat sinking requirements.
I allow just over 1 millisec opening delay for mine when calculating and
the 90 volt spike when I turn them off is not much of a problem.
Large injectors for throttle body injection or very high power engines
are more likely to be low impedance. Larger injectors need more energy
to activate them. I have not used them but they are not uncommon in the
aftermarket. Low impedance ones will open faster I believe but you
typically throttle back the current to a hold open value. That likely
extends life but it also lets them close faster. The higher current and
higher voltage spikes of low impedance injectors complicates things.
Your power resistors would be there to reduce the hold open current.
There are other methods like pulse width modulation, flyback circuits,
etc. There are hardware and software methods of accomplishing all this
but it is simpler with the high impedance (lower current) injectors.
I'm pleased if I helped a bit. SDS does good work and they likely have
better explanations of this on their extensive website so definitely
follow their recommendations.
Ken
jonlaury wrote:
Quote: |
<jonlaury(at)impulse.net>
Ken, Thank you for your illumination of some issues surrounding EFI.
The Simple Digital Systems EFI is the one I'm using. Your comments
have explained why SDS said that I might want to consider using a 15
amp circuit. It never made sense to me until I read your comments
about sizing for all 6 injectors locking on (100% duty cycle). The
bridge diode that I'm using is rated for 25a (at) 200v so there seems to
be sufficient headroom. My injectors are low impedance type and SDS
supplies a 3 x 4 x 1/8" aluminum piece with 3 gold anodized
resistors??(I'm guessing) that have fins radiating around them.
Installation instructions say this piece can get "quite hot at higher
duty cycles". It seems that the SDS EFI 'wants' to have high
impedance injectors. Are there advantages to a high impedance
architecture?
John
|
| - The Matronics AeroElectric-List Email Forum - | | Use the List Feature Navigator to browse the many List utilities available such as the Email Subscriptions page, Archive Search & Download, 7-Day Browse, Chat, FAQ, Photoshare, and much more:
http://www.matronics.com/Navigator?AeroElectric-List |
|
|
|
Back to top |
|
 |
|
|
You cannot post new topics in this forum You cannot reply to topics in this forum You cannot edit your posts in this forum You cannot delete your posts in this forum You cannot vote in polls in this forum You cannot attach files in this forum You can download files in this forum
|
Powered by phpBB © 2001, 2005 phpBB Group
|