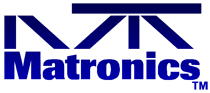 |
Matronics Email Lists Web Forum Interface to the Matronics Email Lists
|
View previous topic :: View next topic |
Author |
Message |
Louie928
Joined: 15 Nov 2009 Posts: 32 Location: Mosier, OR USA
|
Posted: Sun Nov 28, 2010 8:13 pm Post subject: Ford EDIS-6 current requirement |
|
|
I'm working up the wiring scheme for my Corvair aero engine for my Zenith 601XLB. I've studied The AeroElectric Connection book and am incorporating all the great ideas. I think I'll have a good and reliable system. I decided to use electronic ignition based on the Ford EDIS-6 system. I'll have an always on (critical) buss that will power the ignition and fuel pumps. The Facet fuel pumps take about 1 amp. I have two pumps, but one on at a time. I don't know what current the EDIS-6 system will take. I need to know what total current draw the critical buss will require to determine the feed wire size and fuse link size.
I'll have a switch to switch between two EDIS ignition systems, but haven't yet figured a way to reliably use either of two EDIS units to drive a single 6 pak coil with three primaries. A triple pole double throw relay should do it, but I'm reluctant to add in a failure point.
Thanks for any help.
| - The Matronics AeroElectric-List Email Forum - | | Use the List Feature Navigator to browse the many List utilities available such as the Email Subscriptions page, Archive Search & Download, 7-Day Browse, Chat, FAQ, Photoshare, and much more:
http://www.matronics.com/Navigator?AeroElectric-List |
|
_________________ Louis W. Ott
601XL-B Corvair |
|
Back to top |
|
 |
nuckolls.bob(at)aeroelect Guest
|
Posted: Mon Nov 29, 2010 5:27 am Post subject: Ford EDIS-6 current requirement |
|
|
At 10:13 PM 11/28/2010, you wrote:
Quote: |
I'm working up the wiring scheme for my Corvair aero engine for my
Zenith 601XLB. I've studied The AeroElectric Connection book and am
incorporating all the great ideas. I think I'll have a good and
reliable system. I decided to use electronic ignition based on the
Ford EDIS-6 system. I'll have an always on (critical) buss that will
power the ignition and fuel pumps. The Facet fuel pumps take about 1
amp. I have two pumps, but one on at a time. I don't know what
current the EDIS-6 system will take. I need to know what total
current draw the critical buss will require to determine the feed
wire size and fuse link size.
|
Electrically dependent engines should run
from a battery bus which is short-coupled
to the battery and gets no upstream 'protection'
See z-figures.
Quote: | I'll have a switch to switch between two EDIS ignition systems, but
haven't yet figured a way to reliably use either of two EDIS units
to drive a single 6 pak coil with three primaries. A triple pole
double throw relay should do it, but I'm reluctant to add in a failure point.
|
Have you looked into pairs of steering diodes
where either ignition module can drive a
single coil? Much more reliable than any
switch or relay. Do you know anyone who
is running the EDIS system that can conduct
an experiment with the diodes to see if it
affects operations?
Bob . . .
| - The Matronics AeroElectric-List Email Forum - | | Use the List Feature Navigator to browse the many List utilities available such as the Email Subscriptions page, Archive Search & Download, 7-Day Browse, Chat, FAQ, Photoshare, and much more:
http://www.matronics.com/Navigator?AeroElectric-List |
|
|
|
Back to top |
|
 |
klehman(at)albedo.net Guest
|
Posted: Mon Nov 29, 2010 6:11 am Post subject: Ford EDIS-6 current requirement |
|
|
For fuse size I look at the resistance of the coils. If one coil driver
fails and is continuously ON, then that coil will draw continuous
current. Measure the resistance or put a coil primary across a 14 volt
source and measure that current. You don't want one failed coil circuit
to bring down the system. So I'd use a 15 amp circuit regardless of the
normal lower current draw of an EDIS unit.
I used high voltage diodes (coil joiners) on the secondaries with a 4
cylinder DIS system. The spark plugs fire with opposite polarity on each
side of the coils which complicates this method. 6 cylinders makes it
even messier. Frankly I'd recommend a distributor and feed it through
two coils via one MSD high voltage coil joiner for your engine. Race
cars have done that for years. Run either or both systems
simultaneously. You need a feed diode on each system only if they have
different power sources. That recommendation is based on my
understanding of likely failure modes and dramatic simplification for
achieving meaningful redundancy. Most dual ignition systems are far from
redundant and complicated schemes have their own risks of physical
failure as well as system mis-management. If you don't want a
distributor then even better is to look at a separate coil for each
spark plug either fed by EDIS or something else.
I think you are proposing to run two EDIS electronics and sensors but
one coil pack of 3 DIS coils. If that is the intention and the coils are
separate from the electronics then I will address some of those issues.
This method can quickly turn into a can of worms and you will have to
decide what failure modes you wish to cater to. (solid state electronic
failure, coil failure, power source failure, wiring failure, all of these)
Assume coils mounted separate from the EDIS driver circuitry. I would
isolate the EDIS electronics such that a failure of one can't take out
the second unit otherwise what's the point of having two units? That
implies feeding the switched side of the coils through diodes to each
EDIS (6 diodes there). If you do that it suddenly becomes OK to run both
systems simultaneously. One single pole power switch for each EDIS unit.
This approach should make it just fine to run both simultaneously for
takeoff and landing if desired. If you have two power sources then yes
feed each EDIS unit through it's own switch from its own power source.
This assumes you can power up and run an EDIS system while the engine is
already running.
The above effectively makes the EDIS electronics (but not the coils)
redundant. Next issue is whether you want two sources of power to the
+12 volt side of the coils. If so then you can also feed them through
diodes from the separately switched and fused circuits feeding the EDIS
electronics. But what is the risk that a shorted coil might blow both
fuses? Most folks would ignore that I think but if you can maintain
flight on two of the three coils, you could feed each coil through a
separate fuse. That complicates running separate 12volt sources of power
of course. I'm not familiar with the EDIS coil packs. I'd guess that
they rarely blow a fuse and it may be reasonable to simply feed all 3
coils from a common 15 amp circuit.
If you are new to electronics, note that I would consider properly sized
diodes to be as least as reliable as fuses if you can mount them without
stressing the leads and allow for a little bit of cooling.
And don't neglect ergonomics. On my panel the emergency engine procedure
is to put all switches in the UP position period. That feeds the engine
with the second set of electronics (EFI and Ignition) fed from a second
power source.
If I didn't already say it, I run two DIS systems (GM and Subaru) not
EDIS. For a new installation I would do a separate coil per spark plug.
Ken
Louie928 wrote:
Quote: |
<louieo(at)gorge.net>
I'm working up the wiring scheme for my Corvair aero engine for my
Zenith 601XLB. I've studied The AeroElectric Connection book and am
incorporating all the great ideas. I think I'll have a good and
reliable system. I decided to use electronic ignition based on the
Ford EDIS-6 system. I'll have an always on (critical) buss that will
power the ignition and fuel pumps. The Facet fuel pumps take about 1
amp. I have two pumps, but one on at a time. I don't know what
current the EDIS-6 system will take. I need to know what total
current draw the critical buss will require to determine the feed
wire size and fuse link size.
I'll have a switch to switch between two EDIS ignition systems, but
haven't yet figured a way to reliably use either of two EDIS units to
drive a single 6 pak coil with three primaries. A triple pole double
throw relay should do it, but I'm reluctant to add in a failure
point.
Thanks for any help.
-------- Louis W. Ott
601XL beginner Quick Build
|
| - The Matronics AeroElectric-List Email Forum - | | Use the List Feature Navigator to browse the many List utilities available such as the Email Subscriptions page, Archive Search & Download, 7-Day Browse, Chat, FAQ, Photoshare, and much more:
http://www.matronics.com/Navigator?AeroElectric-List |
|
|
|
Back to top |
|
 |
Louie928
Joined: 15 Nov 2009 Posts: 32 Location: Mosier, OR USA
|
Posted: Mon Nov 29, 2010 11:50 am Post subject: Re: Ford EDIS-6 current requirement |
|
|
nuckolls.bob(at)aeroelect wrote: |
Electrically dependent engines should run
from a battery bus which is short-coupled
to the battery and gets no upstream 'protection'
See z-figures. |
I looked at and try to conform to the Z figures where applicable. The problem is that it'll be near impossible to keep the "always on" buss (shown as Main Battery buss on Z-13/8 ) as short as 6". I could put that buss fuse block on the firewall and run the fuse protected circuits through to the instrument panel and switches. I'd rather have the Main Battery buss in the cockpit where I can observe the fuses. Doing that means feeding the Main Battery buss through either a fuse or a fuse link so I don't have unlimited current source in the cockpit. If doing that is thought to be troublesome, I can mount the Main Battery buss distribution block on the engine side of the firewall and not have access to the fuses in flight.
Quote: |
Have you looked into pairs of steering diodes
where either ignition module can drive a
single coil? Much more reliable than any
switch or relay. Do you know anyone who
is running the EDIS system that can conduct
an experiment with the diodes to see if it
affects operations?
|
I think I can isolate one EDIS control unit from the other with diodes. I don't know of anyone who has done it. Looks like I'll need to experiment with the diodes and see what happens. I'll do this on the ground on a test stand.
| - The Matronics AeroElectric-List Email Forum - | | Use the List Feature Navigator to browse the many List utilities available such as the Email Subscriptions page, Archive Search & Download, 7-Day Browse, Chat, FAQ, Photoshare, and much more:
http://www.matronics.com/Navigator?AeroElectric-List |
|
_________________ Louis W. Ott
601XL-B Corvair |
|
Back to top |
|
 |
Louie928
Joined: 15 Nov 2009 Posts: 32 Location: Mosier, OR USA
|
Posted: Mon Nov 29, 2010 1:27 pm Post subject: Re: Ford EDIS-6 current requirement |
|
|
klehman(at)albedo.net wrote: | For fuse size I look at the resistance of the coils. If one coil driver
fails and is continuously ON, then that coil will draw continuous
current. Measure the resistance or put a coil primary across a 14 volt
source and measure that current. You don't want one failed coil circuit
to bring down the system. So I'd use a 15 amp circuit regardless of the
normal lower current draw of an EDIS unit.
<snip>
I think you are proposing to run two EDIS electronics and sensors but
one coil pack of 3 DIS coils. If that is the intention and the coils are
separate from the electronics then I will address some of those issues.
This method can quickly turn into a can of worms and you will have to
decide what failure modes you wish to cater to. (solid state electronic
failure, coil failure, power source failure, wiring failure, all of these)
Assume coils mounted separate from the EDIS driver circuitry. I would
isolate the EDIS electronics such that a failure of one can't take out
the second unit otherwise what's the point of having two units? That
implies feeding the switched side of the coils through diodes to each
EDIS (6 diodes there). If you do that it suddenly becomes OK to run both
systems simultaneously. One single pole power switch for each EDIS unit.
This approach should make it just fine to run both simultaneously for
takeoff and landing if desired. If you have two power sources then yes
feed each EDIS unit through it's own switch from its own power source.
This assumes you can power up and run an EDIS system while the engine is
already running.
The above effectively makes the EDIS electronics (but not the coils)
redundant. Next issue is whether you want two sources of power to the
+12 volt side of the coils. If so then you can also feed them through
diodes from the separately switched and fused circuits feeding the EDIS
electronics. But what is the risk that a shorted coil might blow both
fuses? Most folks would ignore that I think but if you can maintain
flight on two of the three coils, you could feed each coil through a
separate fuse. That complicates running separate 12volt sources of power
of course. I'm not familiar with the EDIS coil packs. I'd guess that
they rarely blow a fuse and it may be reasonable to simply feed all 3
coils from a common 15 amp circuit.
If you are new to electronics, note that I would consider properly sized
diodes to be as least as reliable as fuses if you can mount them without
stressing the leads and allow for a little bit of cooling.
And don't neglect ergonomics. On my panel the emergency engine procedure
is to put all switches in the UP position period. That feeds the engine
with the second set of electronics (EFI and Ignition) fed from a second
power source.
If I didn't already say it, I run two DIS systems (GM and Subaru) not
EDIS. For a new installation I would do a separate coil per spark plug.
Ken |
Hi Ken,
Thanks for your thoughtful reply. I didn't want to use the Corvair distributor with 2 point sets and dual coils with coil combiners to try and save some weight. Also, I wanted to modernize the system and try something different. With the EDIS, I can set timing using a laptop. I have a dyno for tuning the engine, and I'm used to working with these things. I am not used to designing redundant electronic ignition systems and figuring that part out.
Here is a link to some EDIS information.
http://www.dainst.com/info/edis/edis.html
http://www.megamanual.com/ms2/EDIS.htm
I won't use the Megasquirt for timing control, but I'll use something similar for ignition timing only. The fuel will be by Rotec TBI-40 carb.
Sizing the fuse and buss feed wire size using the coil primary resistance is a good idea. The three coil primaries measure 1.2 ohms each so worst case would be about 10 amps draw. Your suggestion of a 15A fuse is right on. The coil pack is separate from the control unit although on the automotive wiring diagram the coil is powered in parallel with the EDIS control unit +12V feed. I will have a +12V source for the coil and separate switched +12V for each control unit. I do plan on a separate crank sensor and EDIS control unit operating a single coil pack. The coil packs are quite reliable and even if one coil failed and I lost two cylinders, the plane would still remain flyable depending on conditions.
The coil pack is really three separate double ended "dumb" coils in one potted enclosure. I could use six "coil near plug" units, but that would be heavier than the 6 pak. The plus side of CNP is that if one secondary failed, I'd only lose one cylinder rather than two. Coil on plug units don't lend themselves well to the Corvair engine due to the placement of the spark plugs. The COP would stick up too high and too far to the outside.
Using diodes to isolate the EDIS control unit outputs may work just fine and it would allow use of both units at the same time. Depending on the EDIS coil drivers, It may be possible to simply connect the coil driver outputs in parallel to the coils.
I had hoped someone may have been down this road before. I'm thinking I had better make a test setup using a 36-1 crank trigger wheel, 2 sensors, 2 EDIS units and a single coil pack. Set it up and run it steady for a few weeks and see what happens.
Two questions. Do you know of a CNP unit that is a simple "dumb" coil? The Chevy LS1 coils I've worked with are "smart" coils that trigger with a +5 volt pulse. These don't work with a control unit like the EDIS. Which GM DIS system do you use? Do you have redundant control systems, or single thread? I have all the parts for the EDIS, but it isn't too late to switch systems.
Thanks again.
| - The Matronics AeroElectric-List Email Forum - | | Use the List Feature Navigator to browse the many List utilities available such as the Email Subscriptions page, Archive Search & Download, 7-Day Browse, Chat, FAQ, Photoshare, and much more:
http://www.matronics.com/Navigator?AeroElectric-List |
|
_________________ Louis W. Ott
601XL-B Corvair |
|
Back to top |
|
 |
klehman(at)albedo.net Guest
|
Posted: Mon Nov 29, 2010 7:02 pm Post subject: Ford EDIS-6 current requirement |
|
|
Louie928 wrote:
Quote: |
<louieo(at)gorge.net>
klehman(at)albedo.net wrote:
> For fuse size I look at the resistance of the coils. If one coil
> driver fails and is continuously ON, then that coil will draw
> continuous current. Measure the resistance or put a coil primary
> across a 14 volt source and measure that current. You don't want
> one failed coil circuit to bring down the system. So I'd use a 15
> amp circuit regardless of the normal lower current draw of an EDIS
> unit.
>
>
>
> I think you are proposing to run two EDIS electronics and sensors
> but one coil pack of 3 DIS coils. If that is the intention and the
> coils are separate from the electronics then I will address some of
> those issues. This method can quickly turn into a can of worms and
> you will have to decide what failure modes you wish to cater to.
> (solid state electronic failure, coil failure, power source
> failure, wiring failure, all of these)
>
> Assume coils mounted separate from the EDIS driver circuitry. I
> would isolate the EDIS electronics such that a failure of one can't
> take out the second unit otherwise what's the point of having two
> units? That implies feeding the switched side of the coils through
> diodes to each EDIS (6 diodes there). If you do that it suddenly
> becomes OK to run both systems simultaneously. One single pole
> power switch for each EDIS unit. This approach should make it just
> fine to run both simultaneously for takeoff and landing if desired.
> If you have two power sources then yes feed each EDIS unit through
> it's own switch from its own power source. This assumes you can
> power up and run an EDIS system while the engine is already
> running.
>
> The above effectively makes the EDIS electronics (but not the
> coils) redundant. Next issue is whether you want two sources of
> power to the +12 volt side of the coils. If so then you can also
> feed them through diodes from the separately switched and fused
> circuits feeding the EDIS electronics. But what is the risk that a
> shorted coil might blow both fuses? Most folks would ignore that I
> think but if you can maintain flight on two of the three coils,
> you could feed each coil through a separate fuse. That complicates
> running separate 12volt sources of power of course. I'm not
> familiar with the EDIS coil packs. I'd guess that they rarely blow
> a fuse and it may be reasonable to simply feed all 3 coils from a
> common 15 amp circuit.
>
> If you are new to electronics, note that I would consider properly
> sized diodes to be as least as reliable as fuses if you can mount
> them without stressing the leads and allow for a little bit of
> cooling.
>
> And don't neglect ergonomics. On my panel the emergency engine
> procedure is to put all switches in the UP position period. That
> feeds the engine with the second set of electronics (EFI and
> Ignition) fed from a second power source.
>
> If I didn't already say it, I run two DIS systems (GM and Subaru)
> not EDIS. For a new installation I would do a separate coil per
> spark plug.
>
> Ken
Hi Ken, Thanks for your thoughtful reply. I didn't want to use the
Corvair distributor with 2 point sets and dual coils with coil
combiners to try and save some weight. Also, I wanted to modernize
the system and try something different. With the EDIS, I can set
timing using a laptop. I have a dyno for tuning the engine, and I'm
used to working with these things. I am not used to designing
redundant electronic ignition systems and figuring that part out.
Here is a link to some EDIS information.
http://www.dainst.com/info/edis/edis.html
http://www.megamanual.com/ms2/EDIS.htm
I won't use the Megasquirt for timing control, but I'll use something
similar for ignition timing only. The fuel will be by Rotec TBI-40
carb.
Sizing the fuse and buss feed wire size using the coil primary
resistance is a good idea. The three coil primaries measure 1.2 ohms
each so worst case would be about 10 amps draw. Your suggestion of a
15A fuse is right on. The coil pack is separate from the control unit
although on the automotive wiring diagram the coil is powered in
parallel with the EDIS control unit +12V feed. I will have a +12V
source for the coil and separate switched +12V for each control unit.
I do plan on a separate crank sensor and EDIS control unit operating
a single coil pack. The coil packs are quite reliable and even if
one coil failed and I lost two cylinders, the plane would still
remain flyable depending on conditions.
The coil pack is really three separate double ended "dumb" coils in
one potted enclosure. I could use six "coil near plug" units, but
that would be heavier than the 6 pak. The plus side of CNP is that if
one secondary failed, I'd only lose one cylinder rather than two.
Coil on plug units don't lend themselves well to the Corvair engine
due to the placement of the spark plugs. The COP would stick up too
high and too far to the outside.
Using diodes to isolate the EDIS control unit outputs may work just
fine and it would allow use of both units at the same time. Depending
on the EDIS coil drivers, It may be possible to simply connect the
coil driver outputs in parallel to the coils.
I had hoped someone may have been down this road before. I'm thinking
I had better make a test setup using a 36-1 crank trigger wheel, 2
sensors, 2 EDIS units and a single coil pack. Set it up and run it
steady for a few weeks and see what happens.
Two questions. Do you know of a CNP unit that is a simple "dumb"
coil? The Chevy LS1 coils I've worked with are "smart" coils that
trigger with a +5 volt pulse. These don't work with a control unit
like the EDIS. Which GM DIS system do you use? Do you have redundant
control systems, or single thread? I have all the parts for the EDIS,
but it isn't too late to switch systems.
Thanks again.
-------- Louis W. Ott
601XL beginner Quick Build
Louis
|
Actually the only GM DIS coil failure that I've had only failed one
spark plug! There tends to be enough capacitance in the circuit that
pulling one spark plug lead or open circuiting one side of the coil does
not necessarily stop the other plug from firing. And 6 cylinders gives
you a better situation than my 4 cylinder engine should you lose one coil.
I would guess that the EDIS uses the typical open collector driver. If
the LS1 coils need a 5 volt signal you could likely just use a resistor
divider circuit to match them to the EDIS driver. Add a transistor if
the logic needs to be reversed. Alternatively I'm told that there are a
number of dumb Coil Near Plug units used on many power sport engines but
I don't have part numbers.
But I see no reason why your dual EDIS hardware that you already have
would not be satisfactory especially if you are already familiar with
it. I doubt that there is any weight savings compared to a distributor
or CNP units though. Personally I would put in the ability to feed the
coils as well as the EDIS units from two power sources.
It is not just two power sources but also two independent
wiring circuits that comforts me. ie also cater to a bad/corroded
connection or switch or shorted wire. Diodes between the coils and the
EDIS drivers would have to be able to tolerate several hundred volt
spikes of course.
I used a 4 cylinder Chev Cavalier coil pack and module for my second
ignition. A MegaSquirt 2 runs a second set of MPFI injectors. At that
time, MS did not have an ignition option like it does now. Those are
backup systems running off a second electrical system (z-14). All the
electronics run all the time off hot battery busses but I normally only
feed +12volts to one set of injectors and one set of ignition coils at a
time. Dual DIS ignitions are rare. NSI did some based on aftermarket
ecu's but their HV joiners were not very robust. I'm not aware of any
dual EDIS installations.
Ken
| - The Matronics AeroElectric-List Email Forum - | | Use the List Feature Navigator to browse the many List utilities available such as the Email Subscriptions page, Archive Search & Download, 7-Day Browse, Chat, FAQ, Photoshare, and much more:
http://www.matronics.com/Navigator?AeroElectric-List |
|
|
|
Back to top |
|
 |
Louie928
Joined: 15 Nov 2009 Posts: 32 Location: Mosier, OR USA
|
Posted: Mon Nov 29, 2010 10:05 pm Post subject: Re: Ford EDIS-6 current requirement |
|
|
klehman(at)albedo.net wrote: |
Actually the only GM DIS coil failure that I've had only failed one
spark plug! There tends to be enough capacitance in the circuit that
pulling one spark plug lead or open circuiting one side of the coil does
not necessarily stop the other plug from firing. And 6 cylinders gives
you a better situation than my 4 cylinder engine should you lose one coil.
I would guess that the EDIS uses the typical open collector driver. If
the LS1 coils need a 5 volt signal you could likely just use a resistor
divider circuit to match them to the EDIS driver. Add a transistor if
the logic needs to be reversed. Alternatively I'm told that there are a
number of dumb Coil Near Plug units used on many power sport engines but
I don't have part numbers.
But I see no reason why your dual EDIS hardware that you already have
would not be satisfactory especially if you are already familiar with
it. I doubt that there is any weight savings compared to a distributor
or CNP units though. Personally I would put in the ability to feed the
coils as well as the EDIS units from two power sources.
It is not just two power sources but also two independent
wiring circuits that comforts me. ie also cater to a bad/corroded
connection or switch or shorted wire. Diodes between the coils and the
EDIS drivers would have to be able to tolerate several hundred volt
spikes of course.
I used a 4 cylinder Chev Cavalier coil pack and module for my second
ignition. A MegaSquirt 2 runs a second set of MPFI injectors. At that
time, MS did not have an ignition option like it does now. Those are
backup systems running off a second electrical system (z-14). All the
electronics run all the time off hot battery busses but I normally only
feed +12volts to one set of injectors and one set of ignition coils at a
time. Dual DIS ignitions are rare. NSI did some based on aftermarket
ecu's but their HV joiners were not very robust. I'm not aware of any
dual EDIS installations.
Ken |
Thanks for the information. The two separate power sources sounds like a good idea too. You are right. It does get complicated.
| - The Matronics AeroElectric-List Email Forum - | | Use the List Feature Navigator to browse the many List utilities available such as the Email Subscriptions page, Archive Search & Download, 7-Day Browse, Chat, FAQ, Photoshare, and much more:
http://www.matronics.com/Navigator?AeroElectric-List |
|
_________________ Louis W. Ott
601XL-B Corvair |
|
Back to top |
|
 |
|
|
You cannot post new topics in this forum You cannot reply to topics in this forum You cannot edit your posts in this forum You cannot delete your posts in this forum You cannot vote in polls in this forum You cannot attach files in this forum You can download files in this forum
|
Powered by phpBB © 2001, 2005 phpBB Group
|