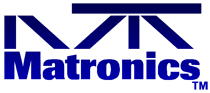 |
Matronics Email Lists Web Forum Interface to the Matronics Email Lists
|
View previous topic :: View next topic |
Author |
Message |
aslink
Joined: 23 Jul 2011 Posts: 25
|
Posted: Sat Jul 23, 2011 6:32 pm Post subject: DRILLING HOLE IN NEW WELDMENT |
|
|
HELP!! HOW DO I DRILL HOLE IN NEW AXLE WELDMENT TO MATCH OLD HOLE IN LANDING GEAR STRUT AND STILL MAINTAIN PROPER TOE-IN? FIRESTAR II.
| - The Matronics Kolb-List Email Forum - | | Use the List Feature Navigator to browse the many List utilities available such as the Email Subscriptions page, Archive Search & Download, 7-Day Browse, Chat, FAQ, Photoshare, and much more:
http://www.matronics.com/Navigator?Kolb-List |
|
_________________ Andy |
|
Back to top |
|
 |
racerjerry
Joined: 15 Dec 2009 Posts: 202 Location: Deer Park, NY
|
Posted: Sun Jul 24, 2011 5:54 am Post subject: Re: DRILLING HOLE IN NEW WELDMENT |
|
|
I am assuming that you are speaking of a new axle weldment or axle shaft at the WHEEL end of the aluminum landing gear leg. The job is not easy. It helps if you
#1 Get lucky
#2 Have a good friend with a machine shop
Let me describe a method which is best done on a rigid Bridgeport mill.
Set up your airplane on a garage / hangar floor with new weldment (axle shaft) in place. Set everything up at the desired toe angle and carefully make an index mark on both weldment and gear leg where they join so that you are able to re-establish the same position after gear leg and weldment are removed from the airplane. You really need some weight on the wheel to get the correct settings, so you may have to re-check by clamping (pinching) the weldment to the gear leg or jam something in the socket to keep it from swiveling.
After your index marks are made, you need to find a steel shaft to act as a guide pin which fits snug but will freely pass through the existing hole in the gear leg. I believe your Firestar uses an AN4 (1/4 inch) bolt to attach the weldment. I recommend a hardened steel dowel pin, but hack sawing the ends off of a long hard grade 8 bolt from the hardware store will work too. The guide pin needs to be hard or it can bend and screw up your setup. The idea is to place the guide pin in the mill’s drill chuck (with mill spindle lowered) and firmly clamp the gear leg to the mill’s table so that the guide pin will pass through the existing hole in the gear leg as the chuck is lowered.
Next, the axle shaft / weldment is placed on the clamped gear leg with index marks lined up and a small pilot hole is drilled into the weldment. You need to start with a small drill bit and work up in steps so that you will put minimum pressure on the clamped gear leg so as to not move it out of position. After each drilling, you may want to remove the weldment and use the guide pin to check that the gear leg has not moved out of position. When you are ready to drill the final (1/4 inch) size, drill the hole so that it just breaks through the first side of the steel weldment tube and does not penetrate into the aluminum gear leg.
You do not want to remove any aluminum with the drill bit. After the first side of the hole is drilled, it is tempting to keep going through to the other side – DON’T!
Again, start with the small drill bits to slowly open up the opposite side of the tube. When you are ready for the final pass with the ¼ inch drill bit, the bit will quickly pass through, with minimum aluminum contact.
I know that friends with Bridgeport mills are hard to come by and you may be tempted to try this procedure on a drill press. If you can at least use a drill press with a wide “production” table, it may give you enough room for a clamping fixture, but the mill is a lot more rigid and easier.
Good luck and remember that if you are flying off a grass strip, your toe settings are not really all that critical.
P.S. When making the index marks, you don’t want to put deep scribed lines, especially circumferential ones, on the aluminum gear leg. Layout dye or a very light coat of spray paint will allow light scribing without digging into and marring the aluminum. The gear leg is rugged, but we want no excuses for a fatigue crack to start.
| - The Matronics Kolb-List Email Forum - | | Use the List Feature Navigator to browse the many List utilities available such as the Email Subscriptions page, Archive Search & Download, 7-Day Browse, Chat, FAQ, Photoshare, and much more:
http://www.matronics.com/Navigator?Kolb-List |
|
_________________ Jerry King |
|
Back to top |
|
 |
byoungplumbing(at)gmail.c Guest
|
Posted: Sun Jul 24, 2011 1:00 pm Post subject: DRILLING HOLE IN NEW WELDMENT |
|
|
to drill a new weldment into an existing axel.
take a piece of tube that will fit over the axel that is is large enough
to fit over the weldment. split the tube so it could be clamped on the
axel without movement. place a bolt through the hole in the axel. and
slide a small tube over both ends of the bolt these will serve as a drill
alignment jig. weld the small tubes to the end of the tube that is
clamped to the axel. pull the bolt out, then install the weldment at the
proper alignment, now you have a drill alignment tube that is lined up with
the hole in the axel.
to modify this procedure to give you some adjustment,,, when installing
the bolt through the axel.... use a 1/4 do ax 3/16 id tube for a bushing
through the axel, then install a 3/16 inch rod through the bushing and
axel hole, weld a 3/16 inch id drill guide tube to the split, clamped
tube, then drill the weldment with a 3/16 inch drill.. leaving the
bushing in place position the weldment on the plane with a 3/16 " bolt.
check for alignment, if it is ok drill out the hole to fit, if not
file or drill out the hole to correct the alignment then drill to final
size,
the biggest problem with this method is the tapered gear leg. that will
make it harder to clamp to securely. so be careful. it may be necessary
to make 3 or 4 splits and heat the tube so it can be bent to fit the taper.
you can use this jig like a blind rivet hole locater.
boyd young
| - The Matronics Kolb-List Email Forum - | | Use the List Feature Navigator to browse the many List utilities available such as the Email Subscriptions page, Archive Search & Download, 7-Day Browse, Chat, FAQ, Photoshare, and much more:
http://www.matronics.com/Navigator?Kolb-List |
|
|
|
Back to top |
|
 |
rickofudall
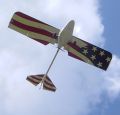
Joined: 19 Sep 2009 Posts: 1392 Location: Udall, KS, USA
|
Posted: Sun Jul 24, 2011 7:23 pm Post subject: DRILLING HOLE IN NEW WELDMENT |
|
|
There's actually a first step to any of these methods and that is to examine the hole in the gear leg. Is it centered? Is it the correct size? Is there any sign that the gear leg has been bent? This is the time to determine if it is in serviceable condition. Maybe you want to replace the gear leg if it's questionable. If you're happy with the old gear leg, here's another way to get a precise hole.
Get a small piece of hardwood, ply wood, or particle board (hardwood is best) about 1" X 3" X 6", a couple of tongue depressors, a small can of Bondo, a 3" C clamp, and a 1/4" transfer punch. Place the new weldment on the landing gear leg and align loosely, say +/- a degree or two. Clamp the block to the gear leg normal to the existing bolt hole with the tongue depressors as spacers so that the new weldment can be taken on and off without disturbing the block. When you're satisfied that the block is close to 90 degrees to the hole and the weldment slides off and on easily, mix a batch of Bondo and glue the block to the gear leg with it. Let harden about 15 minutes. Drill thru the board using the landing gear hole as a guide. Slide the weldment back on to the gear leg and align it carefully. Put the transfer punch through the hole in the board and tap the end with a hammer. Remove the weldment and drill the hole out on a drill press. Start with a smaller drill, say a #40, so you make sure the drill stays centered on the punch mark and work up. Deburr and check that the transfer punch fits nicely in the hole. Put the weldment back on the landing gear leg, align and put the transfer punch through the board, the first hole in the weldment, and the landing gear leg. Check alignment. Tap the transfer punch. Remove the weldment and drill the punch mark, making sure to align drill bit in the center of the first hole. Again, start small and drill up so the drill doesn't push to one side. Remove the clamp, knock the board off, remove the remaining bondo and install the weldment.
Rick Girard
On Sun, Jul 24, 2011 at 3:54 PM, b young <byoungplumbing(at)gmail.com (byoungplumbing(at)gmail.com)> wrote:
Quote: | --> Kolb-List message posted by: "b young" <byoungplumbing(at)gmail.com (byoungplumbing(at)gmail.com)>
to drill a new weldment into an existing axel.
take a piece of tube that will fit over the axel that is is large enough to fit over the weldment. split the tube so it could be clamped on the axel without movement. place a bolt through the hole in the axel. and slide a small tube over both ends of the bolt these will serve as a drill alignment jig. weld the small tubes to the end of the tube that is clamped to the axel. pull the bolt out, then install the weldment at the proper alignment, now you have a drill alignment tube that is lined up with the hole in the axel.
to modify this procedure to give you some adjustment,,, when installing the bolt through the axel.... use a 1/4 do ax 3/16 id tube for a bushing through the axel, then install a 3/16 inch rod through the bushing and axel hole, weld a 3/16 inch id drill guide tube to the split, clamped tube, then drill the weldment with a 3/16 inch drill.. leaving the bushing in place position the weldment on the plane with a 3/16 " bolt. check for alignment, if it is ok drill out the hole to fit, if not file or drill out the hole to correct the alignment then drill to final size,
the biggest problem with this method is the tapered gear leg. that will make it harder to clamp to securely. so be careful. it may be necessary to make 3 or 4 splits and heat the tube so it can be bent to fit the taper.
you can use this jig like a blind rivet hole locater.
boyd young
====================================
arget="_blank">http://www.matronics.com/Navigator?Kolb-List
====================================
http://forums.matronics.com
====================================
le, List Admin.
="_blank">http://www.matronics.com/contribution
====================================
|
--
Zulu Delta
Mk IIIC
Thanks, Homer GBYM
It isn't necessary to have relatives in Kansas City in order to be unhappy.
- Groucho Marx
[quote][b]
| - The Matronics Kolb-List Email Forum - | | Use the List Feature Navigator to browse the many List utilities available such as the Email Subscriptions page, Archive Search & Download, 7-Day Browse, Chat, FAQ, Photoshare, and much more:
http://www.matronics.com/Navigator?Kolb-List |
|
_________________ The smallest miracle right in front of you is enough to make you happy.... |
|
Back to top |
|
 |
racerjerry
Joined: 15 Dec 2009 Posts: 202 Location: Deer Park, NY
|
Posted: Mon Jul 25, 2011 6:05 am Post subject: Re: DRILLING HOLE IN NEW WELDMENT |
|
|
Rick & Boyd, I will have to admit that I love your simpler solutions that do not require access to a machine shop for the “fix.” Both are quick solutions to a real problem – I am impressed.
Rick, since Lowe's sells 1 x 2 x 2 foot oak boards for $2.24, I see no excuse for using anything other than the hardwood you suggest. Scrap oak flooring you may have lying around is ideal too.
This discussion leads me to think of the much more common task of replacing a landing gear leg and matching existing holes in the fuselage socket. Here, I think that either of your solutions described here should work great and it should be mentioned in this forum.
| - The Matronics Kolb-List Email Forum - | | Use the List Feature Navigator to browse the many List utilities available such as the Email Subscriptions page, Archive Search & Download, 7-Day Browse, Chat, FAQ, Photoshare, and much more:
http://www.matronics.com/Navigator?Kolb-List |
|
_________________ Jerry King |
|
Back to top |
|
 |
|
|
You cannot post new topics in this forum You cannot reply to topics in this forum You cannot edit your posts in this forum You cannot delete your posts in this forum You cannot vote in polls in this forum You cannot attach files in this forum You can download files in this forum
|
Powered by phpBB © 2001, 2005 phpBB Group
|