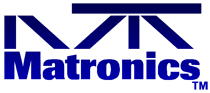 |
Matronics Email Lists Web Forum Interface to the Matronics Email Lists
|
View previous topic :: View next topic |
Author |
Message |
Mauledriver(at)nc.rr.com Guest
|
Posted: Sat Nov 03, 2018 9:12 am Post subject: Dual Battery Dual Alternator Power Distribution System |
|
|
Lance, I've been flying an RV-10 with a Z-14 for over 7 years and 1,000
hours. I think it's the 'Bee's Knees'. I've lost a LR3 controller.
I've slow-killed a few batteries due to some bad management and some
clocks on a battery bus. I have a panel full of yesterday's avionics
with dual feed capabilities. Some people think the Z-14 is overkill but
it has never given me a moment's worry about not having the juice to
complete a flight as planned. In fact, it has enabled me to confidently
plan flights with a dead battery or a dead controller until those
components could be replaced in my home shop.
The main suggestion I would offer is not to start by modifying the
Z-14. Rather implement it as designed. Do it straight up and operate
it as designed. It's a 'belts and suspenders' design in the first
place. You might even be diminishing it's capabilities by modifying it
the ways you have described.
Main power distribution diagram hopefully attached. The thing that
initially caught my eye about the Z-14 is it's simple symmetry - dual
everything with a cross feed.
Some comments made below: (No expert here so take my comments FWIW)
On 11/2/2018 6:48 PM, lwesterlund wrote:
Quote: |
I’m looking for some help in reviewing a draft Dual Battery/ Dual Alternator (DBDA) power distribution architecture for an RV-14A. I started with Bob Nuckolls’ Z-14 system and I’ve attempted to modify it to capitalize on the dual power feed capabilities of the newest generation of avionics.
My mission is IFR in the Pacific Northwest where there’s lot of clouds and lots of rocks in those clouds. Accordingly, the proposed system utilizes two alternators and two EarthX batteries. The 60W primary alternator will handle all normal loads at 60% capacity. The 20-30W accessory-pad mounted auxiliary alternator will handle its normal loads at 50% capacity, and when called upon, all IFR critical loads indefinitely at 66%+ loading. The two batteries provide a third level of redundancy.
The batteries are not wired for cross connection for starting. I removed that from Bob's Z-14 - if I can’t start the engine with just the primary battery, it’s time to get a new battery.
I would include and use the cross connection for starting. I started
|
with the same thought since I mainly wanted to be able to operate my
panel independent of the engine start so I would light up the bus with
most of the avionics on it for flight planning, filing, clearances,
waiting out local wx, then start on other battery. I'm using Odyssey
680s which, when combined with the light weight starter that was a
standard part of the Vans engine package, gave me marginal starts. But
it always started even in the winter. With that said, that's the wrong
way to do it. First, don't use the 'light weight' starter if there is
such an option on the RV14 engine - they turn fast but without much
punch. Second, always start with both batteries. I'm told that's for
good battery health. Then fly with the cross feed disconnected so that
any failures on either side become quickly evident.
Quote: | Power is distributed through two buses:
1. The Primary Bus feeds all dual feed components as well as the non-critical single feed components. I’ve elected to use the Vertical Power X Pro to control these loads. I realize the VPX does somewhat increase the risk of a single point of failure (not withstanding its two independent controllers and two buses) but even if the VPX did go dark, I could still get home on the completely independent Aux Bus with at least as much capability and safety as I get flying spam cans now.
2. The Aux Bus provides redundant power to all critical IFR dual feed components (PFD, ADAHRS) as well as to several always-nice-to-have dual feed components (MFD, AP, Transponder). It also provides sole power to the WAAS GPS/NAV/COM (which only has a single power feed) and several other redundant loads.
Two potential problems here as I see it. First, by not using a cross
|
feed contactor as laid out in the Z-14, you are bypassing the ability to
run EVERYTHING in your aircraft if there is an alternator or controller
failure. Second, (it may only apply to my particular configuration with
(3) GRT HX MFDs with no on/off switches so I'll save it). But I
initially had my dual input gear (the 3 GRTs and the G430) connected to
both buses but over time came to understand that it was unnecessary
redundancy with the cross feed capability and sometimes it was a
liability. Maybe we can discuss the experiences that led me there later.
Quote: | The Aux Bus will be set to run at a slightly lower voltage than the Primary Bus, so the Primary Alternator will normally carry the full load (excepting the GTN650, stall warning, and optical fuel level detector). Should Primary Bus voltage fall during starting, or due to a Pri Alternator failure, the dual feed components will automatically be picked up by the Aux Bus with no pilot intervention required.
This sounds good. I added a TCW power stabilizer to keep the avionics
|
on during deep discharge starts. The reality as I've experienced it is
that there is no reasonable scenario where power is suddenly lost on one
bus. Rather by monitoring the voltages on each bus during flight (and
assuming batteries don't suddenly blow up) and paying attention to an
alarm saying a bus has dipped below charging voltage, an alternator or
controller failure will become evident with more than enough time to
tuck it away and cross feed the buses to complete the flight as
planned. The battery will keep everything running in the mean time. An
MFD may fail, but that's a different thing.
Think of the Z-14 like a twin engine plane - you don't plan on dual
simultaneous engine failure - you plan on recovery from a single engine
failure. On a Z-14 you identify which side failed, what failed, tuck it
away and hit the cross feed and proceed to your destination. Unlike a
sudden engine failure, the sudden failure of an electrical system
component just causes the voltage to slowly fall on one side. Your
robust battery is your backup until 'the dead foot and dead engine is
identified, feathered, etc'
Quote: |
Regarding the ubiquitous always-hot battery bus, my hypothesis is that it’s no longer necessary given advances in technology. In Z-14 (and earlier in Chapter 17 or The AeroElectric Connection), Bob lists the following loads as worthy of a direct connection to the battery:
• Ignition
• Fuel pump(s)
• Dome light
• Clock
• Radio mem
I totally agree. You may still end up with a so-called battery bus
|
which is really just one or more fuse protected components attached
directly to a battery. The electric fuel pump is a backup device and
doesn't need to be on a direct battery connection. My GRTs use to have
internal clocks that required an always not batt bus which led to some
battery problems. Fortuanately they got rid of the always on requirement
and picked up the time from the GPS(?). Dome lights or a USB power plug
might be nice to have but lights can be left on and USB devices left
plugged in (like my new Sentry) and threaten to kill a battery. Dual
batteries means that it's manageable even on a remote Bahamian island
airport, but a completely unnecessary risk. I have a battery bus with
only a cigarette lighter/power plug left on it and that is mentally
placarded against use.
Quote: |
My initial attempts at developing an architecture included a battery bus for those loads. However, as I started to work through failure modes, the list of battery bus-worthy loads got smaller and smaller. For instance, with dual P-mags (which the manufacturer recommends not connecting to an always hot battery bus) you only need power to one P-mag at start. Above 700 RPM both with self-excite so even in the unlikely event you lose both bus contactors, the plugs will fire and the engine will spin.
The only recommended battery bus load that gives me a little pause is the fuel pump. But, as shown, a simple single pole double throw switch should let me connect to either bus. I would need to lose both buses and the mechanical fuel pump to lose fuel to the engine. Absent battle damage, it seems like the chance of fuel starvation due to an electrical problem is pretty remote.
Regarding bus management, normal operation would be to turn on the G5 (to check G5 back-up battery operation) then the Aux Bus during pre-start to check voltage and set up the avionics. The Primary Bus, electric fuel pump and P-mags would be turned on just prior to engine start-up. If the twirley thingy in front spins, you’re good to go.
When done flying, the procedure would be to turn off the Primary Bus (to confirm load pick-up by the Aux Alt), then secure the Aux Bus, then the G5 which has its own battery, and finally the P-mags.
The way I manage my Z-14 is turn on bus2 to light up the panel and get
|
the IFR stuff going. I light up bus1 so both radios work (there's a
reason), then cross connect for the start and takeoff. I could
disconnect the cross feed so that the voltage readouts would make any
electrical failures apparent but I don't. After takeoff I disconnect
the cross feed for the flight. Just before landing (or whenever I
remember since I don't use a before landing checklist), I reconnect the
cross feed to insure both batteries get a full top off before shutdown.
Landing at night with everything on and the engine at idle will tend to
drain one of the batteries a bit so I cross feed to prevent that.
I don't worry about having one side setup at a lower charging voltage
than the other. I set them at the max recommended by the battery
manufacturer - 14.7 volts. Since I fly with them disconnected, both
alternators are doing whatever they have to do and the both batteries
stay fully charged. If anything dips below say 14.4 volts, even
momentarily while in flight, I get concerned. I think I have the low
voltage alarm on my engine monitor screen is set at 14 volts - the low
voltage light on the LR3 are separate.
Quote: |
In the event of an electrical fire in IMC, opening the Primary Battery relay would dump about 70% of loads and feeds. I would still have a full complement of IFR critical equipment running on the Aux Bus. If opening the Primary Battery Relay doesn’t isolate power to the fire, opening the Aux Battery relay would dump the balance of loads and feeds. At that point, I’d still have self-excite power to run the P-mags and the back-up battery to power the G5 EFIS to keep the plane upright. In VFR conditions, I would dump both Pri and Aux buses immediately.
Here's where I'm probably missing it because I don't really have a plan
|
for an electrical fire in IMC short of shutting everything down except
for my backup instruments which currently include an ADI with it's own
backup and some pnuematics. I may need some education here.
Quote: |
So, what I have I missed? Or misunderstood? Or miscalculated? Does eliminating the battery bus increase risk in some unintended way? I’m 100% sure I’ve missed something small, complex, and nuanced. I’m also pretty sure I’ve missed something really, really big. Any feedback would be much appreciated. Thanks.
Lance
Beaverton, OR, RV-14A - Emp & Fuse Done, Finish Kit in Progress, QB Wings Ordered
|
---
This email has been checked for viruses by Avast antivirus software.
https://www.avast.com/antivirus
| - The Matronics AeroElectric-List Email Forum - | | Use the List Feature Navigator to browse the many List utilities available such as the Email Subscriptions page, Archive Search & Download, 7-Day Browse, Chat, FAQ, Photoshare, and much more:
http://www.matronics.com/Navigator?AeroElectric-List |
|
Description: |
|
 Download |
Filename: |
Main_Power_Distribution_12-16.pdf |
Filesize: |
131.24 KB |
Downloaded: |
411 Time(s) |
|
|
Back to top |
|
 |
lwesterlund
Joined: 02 Nov 2018 Posts: 4 Location: Beaverton, OR
|
Posted: Mon Nov 05, 2018 11:03 am Post subject: Re: Dual Battery Dual Alternator Power Distribution System |
|
|
Mauledriver,
Thanks for the quick and detailed response.
I completely agree that Z-14 is an amazingly robust architecture. The one limitation, as I see it, is that it doesn’t take advantage of the dual power feeds for capable equipment. You wrote:
“But I initially had my dual input gear (the 3 GRTs and the G430) connected to
both buses but over time came to understand that it was unnecessary
redundancy with the cross feed capability and sometimes it was a
liability. Maybe we can discuss the experiences that led me there later.”
Please help me to understand why using the redundant feeds might be a bad idea. Thanks.
Lance
| - The Matronics AeroElectric-List Email Forum - | | Use the List Feature Navigator to browse the many List utilities available such as the Email Subscriptions page, Archive Search & Download, 7-Day Browse, Chat, FAQ, Photoshare, and much more:
http://www.matronics.com/Navigator?AeroElectric-List |
|
|
|
Back to top |
|
 |
Mauledriver(at)nc.rr.com Guest
|
Posted: Thu Nov 08, 2018 2:20 pm Post subject: Dual Battery Dual Alternator Power Distribution System |
|
|
I do actually use the redundant feeds on my GRT screens but each unit is
redundantly connected to 1 bus. One feed goes through a power
stabilizer and the other directly to the bus.
One of the things I wanted to be able to do was to run parts of avionics
bus with engine off, without endangering a start by running down my
battery. I knew from my previous IFR flying experience that being able
to run the panel without killing the starter battery was useful in
fllight planning and waitiing out local weather.
I have (3) GRT HX MFDs. They do not have integral on/off switches and I
chose not to add any. They are all on 1 bus along with the the G430.
When that bus is switched on, one battery starts to drain pretty
quickly. When I first installed them I connected them to only 1 bus and
things worked as desired. During some upgrades and load rebalancing I
decided to connect them to both buses without really thinking it
through. I mean, belts and suspenders must be better, right?
That was a mistake because now I could not control where the load from
the (3) MFDs went unless I turned off 1 bus (and during flight planning
and clearance receptions I ideally want the whole panel with dual comms
up and running). But I did add a power stabilizer to avoid brownouts
during tough starts. With that added, I did use the redundant feeds to
connect to the power stabilizer and the bus directly, with both
connections fed from the same bus. That now works as desired.
As as been discussed elsewhere here, the proliferation of backup
batteries can be a problem. Each of those batteries should be
maintained as carefully as the main battery in a single battery system.
What's the use of the backup if it doesn't perform in a predictable way
when needed? So I will soon be running with zero backup batteries and
depending entirely on the robustness of the Z-14. Even my backup EFIS
will depend entirely on the Z-14 for power.
It seems that one key thing I had to understand about the bus
architectures and the Z-14 in particular is that they are designed and
built in a manner as robust as say the control system. There are a few
fat wire connections at a few points with only a few very reliable
components that could possibly fail. The failure of an alternator or
controller is signaled and bypassed while the battery keeps everything
running, etc. With dual buses, batts and alts, having redundant power
feeds on individual components is redundant. One relies on the
redundant bus architecture to handle power failures.
On 11/5/2018 2:03 PM, lwesterlund wrote:
Quote: |
Mauledriver,
Thanks for the quick and detailed response.
I completely agree that Z-14 is an amazingly robust architecture. The one limitation, as I see it, is that it doesn’t take advantage of the dual power feeds for capable equipment. You wrote:
“But I initially had my dual input gear (the 3 GRTs and the G430) connected to
both buses but over time came to understand that it was unnecessary
redundancy with the cross feed capability and sometimes it was a
liability. Maybe we can discuss the experiences that led me there later.â€
Please help me to understand why using the redundant feeds might be a bad idea. Thanks.
Lance
Read this topic online here:
http://forums.matronics.com/viewtopic.php?p=484447#484447
|
---
This email has been checked for viruses by Avast antivirus software.
https://www.avast.com/antivirus
| - The Matronics AeroElectric-List Email Forum - | | Use the List Feature Navigator to browse the many List utilities available such as the Email Subscriptions page, Archive Search & Download, 7-Day Browse, Chat, FAQ, Photoshare, and much more:
http://www.matronics.com/Navigator?AeroElectric-List |
|
|
|
Back to top |
|
 |
lwesterlund
Joined: 02 Nov 2018 Posts: 4 Location: Beaverton, OR
|
Posted: Thu Nov 08, 2018 5:14 pm Post subject: Re: Dual Battery Dual Alternator Power Distribution System |
|
|
Again, thanks for the detailed reply. Your approach certainly makes sense when using a conventional power bus. Afterall, what could possibly go wrong with a solid brass bus bar? It’s darn near bullet-proof.
As I asked in my reply to Bob’s response, what if you are using the VPX system? As robust as it is, it’s still not as failure proof as a solid hunk of metal. Even with dual power feeds, it becomes a single point of failure. Hence my proposed design.
If there’s a better way that leverages that technology, I’m all ears. But I don’t think you can just plop the VPX into the Z-14 architecture without modifying it to resolve the new SPOF.
I appreciate that the more conservative approach from a power system risk management perspective is to simply use Z-14 as published. I’m interested in the VPX because, IMO, it helps to reduce other elements of risk. For instance, it prevents deploying the flaps above Vfe, will detect and alert an open circuit (like the pitot heater), and will control wig-wag lights.
Any thoughts or suggestions or insights on how to include a VPX in a dual bat dual alt system would be much appreciated.
Lance
| - The Matronics AeroElectric-List Email Forum - | | Use the List Feature Navigator to browse the many List utilities available such as the Email Subscriptions page, Archive Search & Download, 7-Day Browse, Chat, FAQ, Photoshare, and much more:
http://www.matronics.com/Navigator?AeroElectric-List |
|
|
|
Back to top |
|
 |
DAVIDSON
Joined: 01 Nov 2017 Posts: 1
|
Posted: Fri Nov 09, 2018 7:35 am Post subject: Re: Dual Battery Dual Alternator Power Distribution System |
|
|
[quote="lAs I asked in my reply to Bob’s response, what if you are using the VPX system? As robust as it is, it’s still not as failure proof as a solid hunk of metal. Even with dual power feeds, it becomes a single point of failure. Hence my proposed design.
[/quote]
I have an RV-7 in gestation. Here is my plan for implementing VPX-Pro in a dual-battery (same) dual-alternator (60A and 20A) EFII-4R system.
1) Both batteries feed to battery bus (copper bar). Each battery contactor has it's own switch.
2) Starter contactor on battery bus. Starter has momentary switch.
3) Battery bus connected to feed bus (copper bar) via 60A shunt.
4) Both alternators feed to feed bus via ANL (60A and 30A). Each alternator field circuit has it's own switch.
5) Feed bus connects through firewall.
6) A 100A relay feeds the X-BUS (VPX-Pro).
7) A 100A relay feeds the E-BUS (12 circuit fuse box).
All circuits are driven by X-BUS.
9) 12 circuits are also driven by E-BUS (essential).
10) The 12 circuits (common to both buses) each feed to a 25A diode bridge rectifier with the plus connection going to the device (sometimes switched).
The 12 common circuits are:
Primary Fuel (switched)
Backup Fuel (switched)
Primary Alt Field (switched)
Primary Alt Vsense
Secondary Alt Field (switched)
Secondary Alt Vsense
Ignition A
Ignition B
ECU A
ECU B
Injectors
Starter (switched)
It is okay to run with both batteries online or I can choose to start engine with both then take one offline in cruise.
It is okay for both X-BUS and E-BUS to be online, but I plan to fly 99% on X-BUS so I can monitor on DYNON SKYVIEW.
It is okay for both alternators to be online. The 60A regulator is set at 14.2V and the 20A regulator is set at 13.7V.
It is okay for both fuel pumps to be on, but 99.9% of time I'll be on one or the other.
The starter switch is hot when E-BUS is closed, but only hot when engine not running when X-BUS is closed.
Feedback welcome.
--kevin--
| - The Matronics AeroElectric-List Email Forum - | | Use the List Feature Navigator to browse the many List utilities available such as the Email Subscriptions page, Archive Search & Download, 7-Day Browse, Chat, FAQ, Photoshare, and much more:
http://www.matronics.com/Navigator?AeroElectric-List |
|
|
|
Back to top |
|
 |
Mauledriver(at)nc.rr.com Guest
|
Posted: Fri Nov 09, 2018 8:39 am Post subject: Dual Battery Dual Alternator Power Distribution System |
|
|
You are welcome! Looks like Bob has responded with a good solution that follows the KISS principle, a hard to adhere to principle when all options are available to the experimental builder.
Note that I took a fair amount of friendly heat from Bob when I was considering the Z-14 for my '10 back in 2008-9. I think he called my panel 'everything including the kitchen sink' and considered the Z-14 overkill even for a 'kitchen sink' installation. As I mentioned before, I fell for the simple symmetry of the design. But beauty and simplicity are in the eye of the beholder I suppose though it took a few years of operation before I learned to not only to implement the design as specified, but then to operate it in the proper way. Having done the former and slowly adopted the latter, I now can fully appreciate the robustness of the thing.
I'm currently starting an upgrade of my panel to include (1) larger GRT HXr screen and replacement of some pneumatic backup instruments and a Trutrak ADI with the Horis EFIS from kanardia. Your VPX/flap protection caught my eye because of a decision I just made about my flap switch. So I've included that and a few other comments below just for kicks.
On 11/8/2018 8:14 PM, lwesterlund wrote:
Quote: | Quote: | --> AeroElectric-List message posted by: "lwesterlund" <lance.westerlund(at)yahoo.com> (lance.westerlund(at)yahoo.com)
Again, thanks for the detailed reply. Your approach certainly makes sense when using a conventional power bus. Afterall, what could possibly go wrong with a solid brass bus bar? It’s darn near bullet-proof. | | Right. I would note that I don't really have any 'bus bars' per se. I have 2 auto-grade fuse panels with power cables running from the alternators/battery connection. That's all very solid and simple along with crossfeed cabling at the battery mount. Very bullet-proof.
Fuse Panel by RH foot well
Quote: | Quote: |
As I asked in my reply to Bob’s response, what if you are using the VPX system? As robust as it is, it’s still not as failure proof as a solid hunk of metal. Even with dual power feeds, it becomes a single point of failure. Hence my proposed design. | | The first version of the VPX was available for my plane but just like electronic ignition, I decided to keep those things old school; dual Mags and hardwiring of everything in the power distribution systems. If I did it again, I'd probably go with electronic ignition and investigate the VPX again.
Quote: | Quote: |
If there’s a better way that leverages that technology, I’m all ears. But I don’t think you can just plop the VPX into the Z-14 architecture without modifying it to resolve the new SPOF.
I appreciate that the more conservative approach from a power system risk management perspective is to simply use Z-14 as published. I’m interested in the VPX because, IMO, it helps to reduce other elements of risk. For instance, it prevents deploying the flaps above Vfe, will detect and alert an open circuit (like the pitot heater), and will control wig-wag lights. | | Flaps: I currently use physically identical but labeled Honeywell rockers for all my switches including the flap switch. I used physical location to distinguish it from say landing lights.
My Panel with Honeywell Rockers
With this current upgrade I was considering using a more classic flap switch with a big toggle.
Aerosport Flap Switch
But now it's clear to me that it's too easy to accidentally hit that switch in cruise flight. We move around on long flights and my wife sometimes crawls to and from the back seat. The AP disconnect on the stick has been accidentally hit more than once. The trim hat has been hit. But that little Honeywell rocker is pretty much safe from accidental acuation. I'm going to stick with it and just highlight it graphically in case someone else ever flies my plane.
Quote: | Quote: |
Any thoughts or suggestions or insights on how to include a VPX in a dual bat dual alt system would be much appreciated. | | Good Luck, you are going to love the RV-10!
This email has been checked for viruses by Avast antivirus software.
www.avast.com [url=#DAB4FAD8-2DD7-40BB-A1B8-4E2AA1F9FDF2] [/url]
| - The Matronics AeroElectric-List Email Forum - | | Use the List Feature Navigator to browse the many List utilities available such as the Email Subscriptions page, Archive Search & Download, 7-Day Browse, Chat, FAQ, Photoshare, and much more:
http://www.matronics.com/Navigator?AeroElectric-List |
|
|
|
Back to top |
|
 |
|
|
You cannot post new topics in this forum You cannot reply to topics in this forum You cannot edit your posts in this forum You cannot delete your posts in this forum You cannot vote in polls in this forum You cannot attach files in this forum You can download files in this forum
|
Powered by phpBB © 2001, 2005 phpBB Group
|