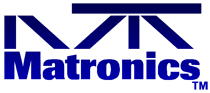 |
Matronics Email Lists Web Forum Interface to the Matronics Email Lists
|
View previous topic :: View next topic |
Author |
Message |
nuckolls.bob(at)aeroelect Guest
|
Posted: Fri Jan 10, 2020 8:35 am Post subject: Lithium BMS and 'load-dump' worries |
|
|
Quote: |
� The recently referenced thread on the Vans Air Force forum proves that it's still the case. The original poster of that thread has been building electronic ignition and electronic injection systems for aircraft for at least a couple of decades, and he stumbled upon the knowledge while doing periodic load testing (that he obviously didn't do before putting the lithium tech battery of choice into service). This was not an EarthX aviation battery; it was one of the offerings from a motorsports company. |
This underscores the value of 'getting the
numbers' . . .
Here is an excerpt from an Enersys-Hawker engineering
data publication.
[img]cid:.0[/img]
No 'hat dancing' no undefined or vague terms. This chart
says that an off the shelf PC680 should deliver hard
values of stored energy depending on (1) discharge
rate or load and (2) condition of the battery [cap check].
In the course of our conversations, I sent a copy of this chart
to EarthX suggesting that until the aviation consumer
had this kind of data they were not serving their customer
well. CRANKING is one thing, ENDURANCE is quite another.
Quote: | � To their credit, EarthX seems to have modified their aviation offerings and increased the cell size (count?) so that total energy does compare with the various SLAs they are marketing against. It did take some rather pointed, public comments on aviation forums for that to happen. |
Good for them . . .and I suspect others but I've
not surveyed the market offerings.
Quote: | On the 'load dump' issue: The BMS in the EarthX (according to EX's own literature, and their rep who posts frequently on VAF) will disconnect the battery under what it considers an overvoltage charge condition . . . |
I've never understood this feature if the
target market is either (1) TC aircraft or
(2) artfully crafted OBAM aircraft. The
ONLY source for an overvoltage condition is
a failed regulator. A fact that has been
recognized and addressed for 70 years by
the application of over voltage detection
and mitigation. They only reason to include it
in the battery's BMS is to cover the instances
where ov protection is NOT provided by the
owner/operator . . . and were I to offer
a lithium product to the non-TC community,
there would be a big sticker on the side of
the battery, "Warranty and Performance claims
are void unless the system is fitted with
ov protection".
Quote: | . . . also when it thinks the battery is in danger of being excessively depleted, |
Yup, EVERY lithium product supplier says
don't discharge below x.x volts per cell . . .
2.8 being a popular number. Again, a condition
very easily addressed at the airframe system
level . . . to include this inside every
battery seems wasteful . . .
Quote: | or too high a current demand is being placed on it. |
Gee, I thought that's what current limiters
were for . . .
Quote: | The very fact that the BMS *can* disconnect the battery (for whatever reason), should, it seems to me, require us to include that fact in failure mode analysis. If the BMS itself fails in a fashion that disconnects the battery, that's a new and different failure mode (which may come as a complete shock if one hasn't done his homework). If the BMS gets confused and thinks the alternator is in an OV condition, it may disconnect from the electrical system> load dump>potential alternator failure>dark airplane. |
I have no doubts that the BMS offered by EarthX,
True Blue and perhaps others perform as advertised
with exceedingly low risk . . . but why all
the so much monkey motion built INSIDE each
delivered unit and repurchased every time
a battery is replaced is a mystery.
Quote: | While load dumps might not be an every day occurrence, they do happen. Many years ago, I killed an alternator with an ill-advised switch flip, so I know it can happen. An EarthX battery mixed with one of those old school IR alternators does up the odds of a dark airplane, if failure modes aren't accounted for. |
Exemplar Load Dump Definition:
Load dump means the disconnection of a powered load. It can cause 2 problems: failure of supply to equipment or customers large voltage spikes from the inductive generator In automotive electronics, it refers to the disconnection of the vehicle battery from the alternator while the battery is being charged. Due to such a disconnection of the battery, other loads connected to the alternator see a surge in power line. The peak voltage of this surge may be as high as 120 V and the surge may take up to 400 ms to decay. It it typically clamped to 40 V in 12 V vehicles and about 60 V in 24 V systems.
A load dump event is simply an abrupt
disconnect of near max load from an
alternator. It doesn't need to be a
battery disconnect . . . but if there
is no battery, the dump transient can
be higher.
I've created many a 'load dump' on the test
bench with no battery on line. You load an
engine driven power source with a load equal
to nameplate rating at maximum expected operating
RPM. Then simply disconnect the load and measure
what happens.
The regulator/alternator dynamics determine
the severity of the recovery transient. But
as long as a battery is on line, the transient
is trivial. Further, DO160 qualification parameters
dictate that the righteous accessory is not
at risk for being subjected to such transients.
The likelihood that a deeply discharged battery
being recharged in a system otherwise lightly
loaded becomes disconnected from the bus is
exceedingly low . . .
A 'load dump' transient is short lived . . . a
few hundred milliseconds. It CAN be of significant
amplitude as I described in the last revision to the
chapter on alternators. But to see/measure one
of these critters takes some careful attention
to conditions that generate the event. The Van's
crowd got their nickers in a wad about 20 years
ago when a builder purposefully cycled the alternator
control switch in Figure Z24 into a less than
charged battery. Indeed it zorked his regulator.
The transient WAS NOT conducted onto the bus. It
affected only the alternator's build in regulator.
Van's alternator of choice was of unknown
pedigree and even then, failure of this particular
alternator may have been at the fringes of the
bell-curve. Nonetheless, the event triggered
a flurry of excited and under-informed assertions
and decisions by some members of the OBAM aviation
community.
The 'load dump' condition is poorly understood
and over-worried. Further, it's in a completely
separate basket from BMS considerations in
lithium batteries. The load-dump overshoot
will be greatly mitigated by the presence
of the battery and it's BMS will have no
reason to disconnect.
Bob . . .
| - The Matronics AeroElectric-List Email Forum - | | Use the List Feature Navigator to browse the many List utilities available such as the Email Subscriptions page, Archive Search & Download, 7-Day Browse, Chat, FAQ, Photoshare, and much more:
http://www.matronics.com/Navigator?AeroElectric-List |
|
Description: |
|
Filesize: |
335.76 KB |
Viewed: |
4399 Time(s) |
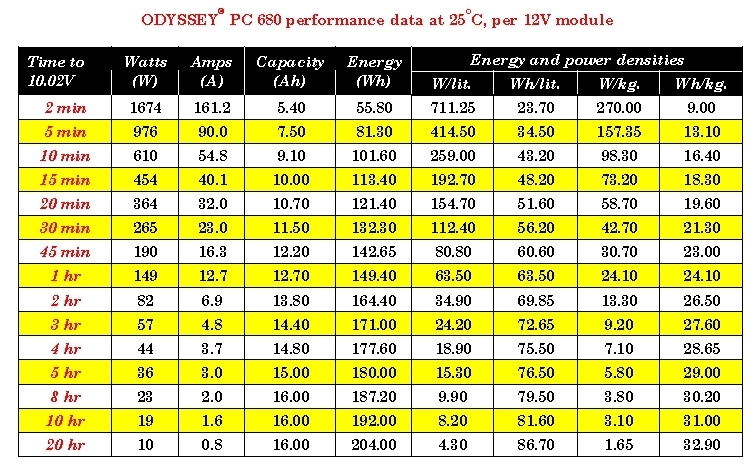
|
|
|
Back to top |
|
 |
ceengland7(at)gmail.com Guest
|
Posted: Fri Jan 10, 2020 9:33 am Post subject: Lithium BMS and 'load-dump' worries |
|
|
On 1/10/2020 10:32 AM, Robert L. Nuckolls, III wrote:
Quote: | Quote: |
� The recently referenced thread on the Vans Air Force forum proves that it's still the case. The original poster of that thread has been building electronic ignition and electronic injection systems for aircraft for at least a couple of decades, and he stumbled upon the knowledge while doing periodic load testing (that he obviously didn't do before putting the lithium tech battery of choice into service). This was not an EarthX aviation battery; it was one of the offerings from a motorsports company. |
� This underscores the value of 'getting the
� numbers' . . .
� Here is an excerpt from an Enersys-Hawker engineering
� data publication.
[img]cid:part1.4AE0F74C.B8F86A08(at)gmail.com[/img]
� No 'hat dancing' no undefined or vague terms. This chart
� says that an off the shelf PC680 should deliver hard
� values of stored energy depending on (1) discharge
� rate or load and (2) condition of the battery [cap check].
� In the course of our conversations, I sent a copy of this chart
� to EarthX suggesting that until the aviation consumer
� had this kind of data they were not serving their customer
� well. CRANKING is one thing, ENDURANCE is quite another.
Quote: | To their credit, EarthX seems to have modified their aviation offerings and increased the cell size (count?) so that total energy does compare with the various SLAs they are marketing against. It did take some rather pointed, public comments on aviation forums for that to happen. |
� Good for them . . .and I suspect others but I've
� not surveyed the market offerings.
Quote: | On the 'load dump' issue: The BMS in the EarthX (according to EX's own literature, and their rep who posts frequently on VAF) will disconnect the battery under what it considers an overvoltage charge condition . . . |
� I've never understood this feature if the
� target market is either (1) TC aircraft or
� (2) artfully crafted OBAM aircraft. The
� ONLY source for an overvoltage condition is
� a failed regulator. A fact that has been
� recognized and addressed for 70 years by
� the application of over voltage detection
� and mitigation. They only reason to include it
� in the battery's BMS is to cover the instances
� where ov protection is NOT provided by the
� owner/operator . . . and were I to offer
� a lithium product to the non-TC community,
� there would be a big sticker on the side of
� the battery, "Warranty and Performance claims
� are void unless the system is fitted with
� ov protection".
Quote: | �. . .� also when it thinks the battery is in danger of being excessively depleted, |
� Yup, EVERY lithium product supplier says
� don't discharge below x.x volts per cell . . .
� 2.8 being a popular number. Again, a condition
� very easily addressed at the airframe system
� level . . . to include this inside every
� battery seems wasteful . . .
Quote: | or too high a current demand is being placed on it. |
� Gee, I thought that's what current limiters
� were for� . . .
Quote: | The very fact that the BMS *can* disconnect the battery (for whatever reason), should, it seems to me, require us to include that fact in failure mode analysis. If the BMS itself fails in a fashion that disconnects the battery, that's a new and different failure mode (which may come as a complete shock if one hasn't done his homework). If the BMS gets confused and thinks the alternator is in an OV condition, it may disconnect from the electrical system> load dump>potential alternator failure>dark airplane. |
� I have no doubts that the BMS offered by EarthX,
� True Blue and perhaps others perform as advertised
� with exceedingly low risk . . . but why all
� the so much monkey motion built INSIDE each
� delivered unit and repurchased every time
� a battery is replaced is a mystery.
�
Quote: | While load dumps might not be an every day occurrence, they do happen. Many years ago, I killed an alternator with an ill-advised switch flip, so I know it can happen. An EarthX battery mixed with one of those old school IR alternators does up the odds of a dark airplane, if failure modes aren't accounted for. |
� Exemplar Load Dump Definition:
Load dump means the disconnection of a powered load. It can cause 2 problems: failure of supply to equipment or customers large voltage spikes from the inductive generator In automotive electronics, it refers to the disconnection of the vehicle battery from the alternator while the battery is being charged. Due to such a disconnection of the battery, other loads connected to the alternator see a surge in power line. The peak voltage of this surge may be as high as 120 V and the surge may take up to 400 ms to decay. It it typically clamped to 40 V in 12 V vehicles and about 60 V in 24 V systems.
�
� A load dump event is simply an abrupt
� disconnect of near max load from an
� alternator. It doesn't need to be a
� battery disconnect . . . but if there
� is no battery, the dump transient can
� be higher.
� I've created many a 'load dump' on the test
� bench with no battery on line. You load an
� engine driven power source with a load equal
� to nameplate rating at maximum expected operating
� RPM. Then simply disconnect the load and measure
� what happens.
� The regulator/alternator dynamics determine
� the severity of the recovery transient. But
� as long as a battery is on line, the transient
� is trivial. Further, DO160 qualification parameters
� dictate that the righteous accessory is not
� at risk for being subjected to such transients.
� The likelihood that a deeply discharged battery
� being recharged in a system otherwise lightly
� loaded becomes disconnected from the bus is
� exceedingly low . . .
� A 'load dump' transient is short lived . . . a
� few hundred milliseconds. It CAN be of significant
� amplitude as I described in the last revision to the
� chapter on alternators. But to see/measure one
� of these critters takes some careful attention
� to conditions that generate the event. The Van's
� crowd got their nickers in a wad about 20 years
� ago when a builder purposefully cycled the alternator
� control switch in Figure Z24 into a less than
� charged battery. Indeed it zorked his regulator.
� The transient WAS NOT conducted onto the bus. It
� affected only the alternator's build in regulator.
� Van's alternator of choice was of unknown
� pedigree and even then, failure of this particular
� alternator may have been at the fringes of the
� bell-curve. Nonetheless, the event triggered
� a flurry of excited and under-informed assertions
� and decisions by some members of the OBAM aviation
� community.
� The 'load dump' condition is poorly understood
� and over-worried. Further, it's in a completely
� separate basket from BMS considerations in
� lithium batteries. The load-dump overshoot
� will be greatly mitigated by the presence
� of the battery and it's BMS will have no
� reason to disconnect.
� Bob . . . | No argument with any of the above, *except* this: Saying that there's no reason to have avoidable issues if we do our research, doesn't mean that we'll actually *do* our research. (ex: the recent VAF thread on battery capacity.) I promise you that until Ross (on VAF) posted his endurance report, virtually every person on VAF that's replaced an SLA with lithium tech has *assumed* that because the CCA numbers are equal, the capacity is equal. The RVx guys, as a group, are incredibly resistant to looking at any info source other than VAF. And after years of reading VAF posts giving electrical advice, I can tell you that a lot of it is quite bad. On a related point, SLA capacity numbers are available from a number of different vendors, but for lithium tech, it's much more difficult to find and/or interpret, for a more 'typical' aviator.
My point about 'load dump' is that many of us are still using alternators from that 2 decade old era you reference, and many (likely almost all) of those in that subset have no idea about the research documented here on this list.
I agree that the likelihood of BMS failure in a brand EX battery is unlikely. BUT: IIRC, it's already been documented by someone flying an RVx. Wouldn't you agree that when doing a failure mode analysis of our wiring architecture, we should include that failure mode? I know that the B&C products are immune to 'load dump' issues, but for those of us running alternators of 'unknown pedigree', don't we need to consider the risk of a BMS disconnect also taking out our regulator?
Charlie
| - The Matronics AeroElectric-List Email Forum - | | Use the List Feature Navigator to browse the many List utilities available such as the Email Subscriptions page, Archive Search & Download, 7-Day Browse, Chat, FAQ, Photoshare, and much more:
http://www.matronics.com/Navigator?AeroElectric-List |
|
Description: |
|
Filesize: |
335.76 KB |
Viewed: |
4399 Time(s) |
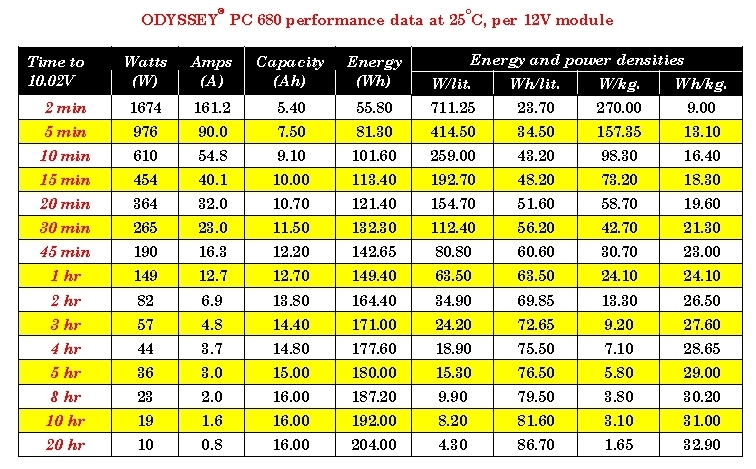
|
|
|
Back to top |
|
 |
nuckolls.bob(at)aeroelect Guest
|
Posted: Fri Jan 10, 2020 1:30 pm Post subject: Lithium BMS and 'load-dump' worries |
|
|
Quote: | The RVx guys, as a group, are incredibly resistant to looking at any
info source other than VAF. And after years of reading VAF posts
giving electrical advice, I can tell you that a lot of it is quite bad. |
That's one of the reasons that the AE-List
came into existence.
Quote: | On a related point, SLA capacity numbers are available from a number
of different vendors, but for lithium tech, it's much more difficult
to find and/or interpret, for a more 'typical' aviator. |
But it's easy to acquire . . . call the
manufacturer. Alternatively, go measure
it . . . or get somebody to do it for you.
Then publish the findings.
If there are any concerns, worries,
uncertainties about system performance
or reliability . . . there is a process
by which they can be resolved. Recorded
measurements under documented test
conditions are pretty solid foundations
for design descisions.
Quote: | My point about 'load dump' is that many of us are still using alternators from that
2 decade old era you reference, and many (likely almost all) of those in that
subset have no idea about the research documented here on this list. |
Has there been more than the one
load-dump failure event that planted the
seeds of concerns, worries, uncertainties?
We know that the triggering circumstance
for the original failure was the builder's
repetitive operation of the alternator
ON-OFF control with a Z-24 ov management
system.
In this case, the battery wasn't disconnected
from the system . . . rather the alternator
b-lead connection was broken. We're not privy
to the state of the battery. For the sake
of argument, let's assume the battery was in
a low state of charge. It's not likely that
there was a large load on the bus.
The alternator has no way of knowing what
is loading the output. All it knows is
total load. So when the b-lead was repeatedly
made and broken, what ever total load was
present contributed to excitation of dump
transient.
No investigation was made for assessing
first failure in the regulator. Nobody knows
if it was an OEM regulator or an after market
device. No failure analysis of consequence was conducted
or even possible. I suggest that factoring this single
event into a couple decades of 'advice' INCREASES
rather than REDUCES risk.
Quote: | I agree that the likelihood of BMS failure in a brand EX battery is unlikely. BUT: IIRC, it's already been documented by someone flying an RVx. Wouldn't you agree that when doing a failure mode analysis of our wiring architecture, we should include that failure mode? |
Sure. So from time of master switch ON to
master switch OFF on any given flight cycle,
what sequence of conditions have to stack up
for a BMS battery disconnect failure to initiate
a potentially risky load dump event?
(1) Engine rpm would have to be high
(2) battery in poor state of charge
(3) BMS (or battery contactor) has to suffer
sudden open circuit. The potential for
battery contactor, wiring and switch
to trigger the event is no different
than BMS failure.
Do we think the failure rate on a solid state BMS
is greater than failure rate on the contactor/wiring/
switch combination? And what is the outcome we're
trying to mitigate? Loss of alternator, runaway
alternator. Are there circumstances other than
loss of contactor/BMS that might trigger the
same condition? How about failure within the
sketchy regulator's components?
Quote: | I know that the B&C products are immune to 'load dump' issues, but
for those of us running alternators of 'unknown pedigree',
don't we need to consider the risk of a BMS disconnect also
taking out our regulator? |
Sure. If it were my airplane and I was flying
an internally regulated alternator of unknown
pedigree, I'd install Z-24 and refrain from
operating the alternator ON/OFF switch at
high rpm and high alternator loads. In this
case, loss of BMS (or contactor) under optimally
unhappy conditions MIGHT take out the regulator.
(a) If the alternator just QUITS, your in-flight decision
making process is no different than if you'd
broken a belt.
(b) If the alternator goes into
RUNAWAY, the OV protection system will
bring it under control.
The alternator switch is ONLY operated at
idle rpm after start up and before shut down.
With this design philosophy and operating
protocol, it doesn't matter what kind of
battery or alternator you've installed.
The lithium battery BMS is of no more
concern than your battery contactor.
Bob . . .
| - The Matronics AeroElectric-List Email Forum - | | Use the List Feature Navigator to browse the many List utilities available such as the Email Subscriptions page, Archive Search & Download, 7-Day Browse, Chat, FAQ, Photoshare, and much more:
http://www.matronics.com/Navigator?AeroElectric-List |
|
|
|
Back to top |
|
 |
yellowduckduo(at)gmail.co Guest
|
Posted: Fri Jan 10, 2020 4:15 pm Post subject: Lithium BMS and 'load-dump' worries |
|
|
There are also a lot of us running PM alternators and there are a lot of
them on rotax engines. Most of those regulators are not terribly robust.
I permanently failed a 20 amp oem John Deere Rectifier/Regulator just by
idling the engine with a flat battery. Yes I knew better but...� Anyway
the voltage immediately went high enough to trip the crowbar OVM. With
an EFI engine I will be staying with VRLA batteries and no BMS for the
time being despite the extra weight.
Ken
On 10/01/2020 4:27 PM, Robert L. Nuckolls, III wrote:
Quote: | > The RVx guys, as a group, are incredibly resistant to looking at any
> info source other than VAF. And after years of reading VAF posts
> giving electrical advice, I can tell you that a lot of it is quite bad.
�� That's one of the reasons that the AE-List
�� came into existence.
> On a related point, SLA capacity numbers are available from a number
> of different vendors, but for lithium tech, it's much more difficult
> to find and/or interpret, for a more 'typical' aviator.
�� But it's easy to acquire . . . call the
�� manufacturer. Alternatively, go measure
�� it . . . or get somebody to do it for you.
�� Then publish the findings.
�� If there are any concerns, worries,
�� uncertainties about system performance
�� or reliability . . . there is a process
�� by which they can be resolved. Recorded
�� measurements under documented test
�� conditions are pretty solid foundations
�� for design descisions.
> My point about 'load dump' is that many of us are still using
> alternators from that
> 2 decade old era you reference, and many (likely almost all) of those
> in that
> subset have no idea about the research documented here on this list.
�� Has there been more than the one
�� load-dump failure event that planted the
�� seeds of concerns, worries, uncertainties?
�� We know that the triggering circumstance
�� for the original failure was the builder's
�� repetitive operation of the alternator
�� ON-OFF control with a Z-24 ov management
�� system.
�� In this case, the battery wasn't disconnected
�� from the system . . . rather the alternator
�� b-lead connection was broken. We're not privy
�� to the state of the battery. For the sake
�� of argument, let's assume the battery was in
�� a low state of charge. It's not likely that
�� there was a large load on the bus.
�� The alternator has no way of knowing what
�� is loading the output. All it knows is
�� total load. So when the b-lead was repeatedly
�� made and broken, what ever total load was
�� present contributed to excitation of dump
�� transient.
�� No investigation was made for assessing
�� first failure in the regulator. Nobody knows
�� if it was an OEM regulator or an after market
�� device. No failure analysis of consequence was conducted
�� or even possible. I suggest that factoring this single
�� event into a couple decades of 'advice' INCREASES
�� rather than REDUCES risk.
> I agree that the likelihood of BMS failure in a brand EX battery is
> unlikely. BUT: IIRC, it's already been documented by someone flying
> an RVx. Wouldn't you agree that when doing a failure mode analysis of
> our wiring architecture, we should include that failure mode?
�� Sure. So from time of master switch ON to
�� master switch OFF on any given flight cycle,
�� what sequence of conditions have to stack up
�� for a BMS battery disconnect failure to initiate
�� a potentially risky load dump event?
�� (1) Engine rpm would have to be high
�� (2) battery in poor state of charge
�� (3) BMS (or battery contactor) has to suffer
������ sudden open circuit. The potential for
������ battery contactor, wiring and switch
������ to trigger the event is no different
������ than BMS failure.
�� Do we think the failure rate on a solid state BMS
�� is greater than failure rate on the contactor/wiring/
�� switch combination? And what is the outcome we're
�� trying to mitigate? Loss of alternator, runaway
�� alternator. Are there circumstances other than
�� loss of contactor/BMS that might trigger the
�� same condition? How about failure within the
�� sketchy regulator's components?
> I know that the B&C products are immune to 'load dump' issues, but
> for those of us running alternators of 'unknown pedigree',
> don't we need to consider the risk of a BMS disconnect also
> taking out our regulator?
�� Sure. If it were my airplane and I was flying
�� an internally regulated alternator of unknown
�� pedigree, I'd install Z-24 and refrain from
�� operating the alternator ON/OFF switch at
�� high rpm and high alternator loads. In this
�� case, loss of BMS (or contactor) under optimally
�� unhappy conditions MIGHT take out the regulator.
�� (a) If the alternator just QUITS, your in-flight decision
������ making process is no different than if you'd
������ broken a belt.
�� (b) If the alternator goes into
������ RUNAWAY, the OV protection system will
������ bring it under control.
�� The alternator switch is ONLY operated at
�� idle rpm after start up and before shut down.
�� With this design philosophy and operating
�� protocol, it doesn't matter what kind of
�� battery or alternator you've installed.
�� The lithium battery BMS is of no more
�� concern than your battery contactor.
� Bob . . .
|
| - The Matronics AeroElectric-List Email Forum - | | Use the List Feature Navigator to browse the many List utilities available such as the Email Subscriptions page, Archive Search & Download, 7-Day Browse, Chat, FAQ, Photoshare, and much more:
http://www.matronics.com/Navigator?AeroElectric-List |
|
|
|
Back to top |
|
 |
nuckolls.bob(at)aeroelect Guest
|
Posted: Sat Jan 11, 2020 8:36 am Post subject: Lithium BMS and 'load-dump' worries |
|
|
At 06:13 PM 1/10/2020, you wrote:
Quote: | --> AeroElectric-List message posted by: C&K <yellowduckduo(at)gmail.com>
There are also a lot of us running PM alternators and there are a lot of them on rotax engines. Most of those regulators are not terribly robust.
I permanently failed a 20 amp oem John Deere Rectifier/Regulator just by idling the engine with a flat battery. Yes I knew better but... Anyway the voltage immediately went high enough to trip the crowbar OVM. With an EFI engine I will be staying with VRLA batteries and no BMS for the time being despite the extra weight.
Ken |
This has the 'smell' of a regulator failure
unrelated to type of battery or power generation
device.
What was the time interval for 'immediate'?
If a matter of seconds or a couple minutes, then
I would infer that the battery was soggy . . . i.e.
not accepting what the alternator was capable
of delivering. The alternator/regulator combination
is inherently current limited under ANY condition.
Hence, if the available current pushed battery
voltage above 16v in a short period of time,
the battery was some combination of soggy (worn
out) or already charged.
I'm not reading anything in your narrative that
suggests a short-term transient (load dump) event
or battery disconnect. I can deduce no reason
to suspect that battery technology choices would
have produced a different outcome.
Run of the mill, regulators for PM alternators
are notoriously weak in their design, particularly
with thermal management. With no more data than
what's provided, I'm inclined to call this
an one-of failure of the regulator.
Bob . . .
| - The Matronics AeroElectric-List Email Forum - | | Use the List Feature Navigator to browse the many List utilities available such as the Email Subscriptions page, Archive Search & Download, 7-Day Browse, Chat, FAQ, Photoshare, and much more:
http://www.matronics.com/Navigator?AeroElectric-List |
|
|
|
Back to top |
|
 |
eschlanser
Joined: 08 Apr 2010 Posts: 60
|
Posted: Sat Jan 11, 2020 1:00 pm Post subject: Re: Lithium BMS and 'load-dump' worries |
|
|
Bob,
You wrote, “If it were my airplane and I was flying
an internally regulated alternator of unknown
pedigree, I'd install Z-24 and refrain from
operating the alternator ON/OFF switch at
high rpm and high alternator loads. In this
case, loss of BMS (or contactor) under optimally
unhappy conditions MIGHT take out the regulator.”
I have wired an unmodified, internally regulated Nippondenso 40 amp alternator in my single AGM Odessey PC680 battery, two alternator, modified Z-13/8 system. I used Z-24 as a guide but with a Perhelion L-OVP module. On start-up, I switch the battery on with both alternators off and push the start switch. After the engine starts, I switch the ND alternator on.
On occasion, I have forgotten to switch the alternator on and took off. A few minutes later, on climb out with high rpm, I noticed the voltage dropping. Upon troubleshooting, I realized the alternator was off. I didn’t think twice, and switched the alternator on. I had no idea this sequence was at some risk to the regulator. Or was it? Would it be a risk to a lithium battery BMS?
Eric S.
South Haven, MI
| - The Matronics AeroElectric-List Email Forum - | | Use the List Feature Navigator to browse the many List utilities available such as the Email Subscriptions page, Archive Search & Download, 7-Day Browse, Chat, FAQ, Photoshare, and much more:
http://www.matronics.com/Navigator?AeroElectric-List |
|
|
|
Back to top |
|
 |
nuckolls.bob(at)aeroelect Guest
|
Posted: Sat Jan 11, 2020 5:09 pm Post subject: Lithium BMS and 'load-dump' worries |
|
|
Quote: | I have wired an unmodified, internally regulated Nippondenso 40 amp alternator in my single AGM Odessey PC680 battery, two alternator, modified Z-13/8 system. I used Z-24 as a guide but with a Perhelion L-OVP module. On start-up, I switch the battery on with both alternators off and push the start switch. After the engine starts, I switch the ND alternator on.
On occasion, I have forgotten to switch the alternator on and took off. A few minutes later, on climb out with high rpm, I noticed the voltage dropping. Upon troubleshooting, I realized the alternator was off. I didn’t think twice, and switched the alternator on. I had no idea this sequence was at some risk to the regulator. Or was it? |
It is not . .
Quote: | Would it be a risk to a lithium battery BMS? |
No . . .
You can generally turn an alternator on/off at any time
without risk to ship's hardware. Z-24 (b-lead
dis-connector) offers some risk to an
INTERNAL regulator IF the alternator is shut off
at higher than idle rpm AND the alternator is heavily
loaded (probably recharging the battery -AND- grunting
ship's loads).
One COULD deliberately create a load-dump
event into the ship's systems by turning
of the battery . . . again while the battery
is heavily loaded. This is POSSIBLE in ships
like Barons and Bonanzas where alternator and
battery switches are not interlinked and
alternator only ops are permitted. However,
the regulators I designed for the Beech
ships were pretty docile for gross load
dump . . . I don't recall the figures now
(that was about 1978). I do recall that the
dump-transient did not exceed DO160/MIL-STD-704
limits - that was a design goal imperative.
Load dump risks are limited to UNLOADING
an alternator . . . not turning it on/off
(EXCEPT where Z-24 DOES unload an internally
regulated alternator placing ONLY the
internal regulator at risk . . . if at
all). ALL Z-figures recommend progressive
transfer, two-pole switches for OFF/BAT/
BAT+ALT making it impossible to deliberately
or inadvertently initiate a load-dump event.
The suggested protocol for turning the
alternator on/off just after engine start
and just before shut down has to do with
an orderly organization of check list that
ALSO happens to be Z-24 friendly.
Load-dumps are something of a wil-o'-the-whisp
(swamp gas). You gotta work to create one
and 99% of the time they are harmless when
they do occur.
BTW . . . I don't think PM rectifier/regulators
are even capable of creating a significant
load dump transient. They use a cycle-by-cycle
conduction control philosophy that does not
present gain/phase issues present in the
wound field system.
Whether or not the battery is fitted with
a BMS isn't a component of the load-dump
scenario.
Bob . . .
| - The Matronics AeroElectric-List Email Forum - | | Use the List Feature Navigator to browse the many List utilities available such as the Email Subscriptions page, Archive Search & Download, 7-Day Browse, Chat, FAQ, Photoshare, and much more:
http://www.matronics.com/Navigator?AeroElectric-List |
|
|
|
Back to top |
|
 |
|
|
You cannot post new topics in this forum You cannot reply to topics in this forum You cannot edit your posts in this forum You cannot delete your posts in this forum You cannot vote in polls in this forum You cannot attach files in this forum You can download files in this forum
|
Powered by phpBB © 2001, 2005 phpBB Group
|