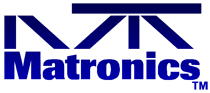 |
Matronics Email Lists Web Forum Interface to the Matronics Email Lists
|
View previous topic :: View next topic |
Author |
Message |
dj_theis
Joined: 28 Aug 2017 Posts: 58 Location: Minnesota
|
Posted: Thu Jan 07, 2021 6:35 pm Post subject: Revmaster R2300 PMA |
|
|
Hello all,
This is a revisiting of the dual integrated PMA that Revmaster (VW derivative) implements on their latest engine design.
There's a lot here so my apologies in advance.
Attached is a scematic of how I've implemented control using a variation of the Z drawings. I've included the current front page with shows the full control scheme with the alternator and a second drawing that I simply redrew to show only the charging circuit. I've done enough checking to convince myself that the regulator / rectifier (R/R) is depicted in a way that at least "losely" shows it's function. Specifically, it is a half wave rectifier with a control circuit controlling an SCR. This SCR opens the path to ground for the alternator to limit charging. The circuit is actually pretty sophisticated in that it will not "turn on" the SCR unless it first senses a battery is present in the circuit. US patent 4,220,909 describes in more detail the safe guards of the circuit that go beyond insuring a battery connection.
My goal with this post is to solicit comments on a failure mode that a few of these engines have had, particularly over the last few years. One strong suggestion the engine supplier has made is to avoid running both stators at the same time AND avoid using the AGM style batteries. My initiial goal was to find evidence (for or against) use of the AGM (Odessey PC680).
The third drawing is the setup I assembled to test the rectifying circuit, independent of the Revmaster alternator. This uses a small 3 phase motor I had along with a 120, single phase input, 3 phase output VFD to drive the motor - coupled to a John Deere, 20 amp 6 pole alternator (very close in performance and characteristics to 1/2 the Revmaster). I plan on expanding testing to verify open circuit and short circuit performance of the full Remaster alternator and RR (in my engine) once I am comfortable withk the design and have enough data to support the use (or not) of an AGM battery.
Sorry for this being so long, almost done setting up the question...
The next two plots are of a couple of the many scope traces I have of the alternator /RR test assembly. The slow speed run up at 30 hz / 875 rpm shows the RR not "turning on" and basically an open circuit voltage measurement of the low rpm alternator with a well charged battery. The 42 hz (1200 rpm) shows the charging circuit just beginning to inject current to the battery at a voltage of 13.52 volts (not this is on the negative trace of the sine wave due to my scope orientation in the charging circuit but it was a positive voltage to the battery.
A few notes. The trace is using a 10x probe. The blue trace is the current measured across the 100 mv (at) 30 amp shunt. The values on the horizontal lines on the scope trace are on the bottom right of the printout.
The John Deere alternator runups were done using a large, wet, lead acid battery (donated by my '64 Pontiac that's resting for the winter). The regulator will not activate without a working battery attached. More on that if anyone is interested.
Finally, the last photo is of one of the stators on the Revmaster engine AFTER it failed. I'm told by the pilot (Glen Bradley) that his two stator failures occurred in flight under higher rpms and after the battery (the Odessey AGM) was worked over during a hard start.
HERE IS MY Thesis: I suspect that the stators are experiencing "turn to turn short circuits." This fault mode was suggested to me by another engineer where I work (experienced in these failures) and in his words, "a short between two adjacent wires in the stator is common and one of the most rapid ways a stator will self destruct." (as opposed to a phase to ground fault on a stator)
After a bit of reading I've come up with what I think are justifying equations that would predict the result of shorting a single loop of the stator wire. A single loop of wire on a permanent magnet alternator experiences a circulating current that is at least an order of magentude greater than the complete coil. This rotating conductor (attached to the upstream and down stream stator wiring at a single point) quickly overheats and initiates a cascading failure of adjacent insulation.
If you look at the photo of the burned stator, the 12 O'clock and 6 )'clock coils are stand a lone stators for the redundent CDI ignition. The right five from 1 O'clock to 5 O'clock make up the right stator for the PMA. The left five from 7 to 11 O'clock are the other PMA stator, making up the dual alternator.
I find it more than interesting that only one of the coils making up the left stator is burned while the other 4 appear perfect. Also, the CDI ignition coil failed as well and of course, it is in no way connected to the AGM battery.
I'll stop there and wait for comment
| - The Matronics AeroElectric-List Email Forum - | | Use the List Feature Navigator to browse the many List utilities available such as the Email Subscriptions page, Archive Search & Download, 7-Day Browse, Chat, FAQ, Photoshare, and much more:
http://www.matronics.com/Navigator?AeroElectric-List |
|
Description: |
|
Filesize: |
216.02 KB |
Viewed: |
3064 Time(s) |
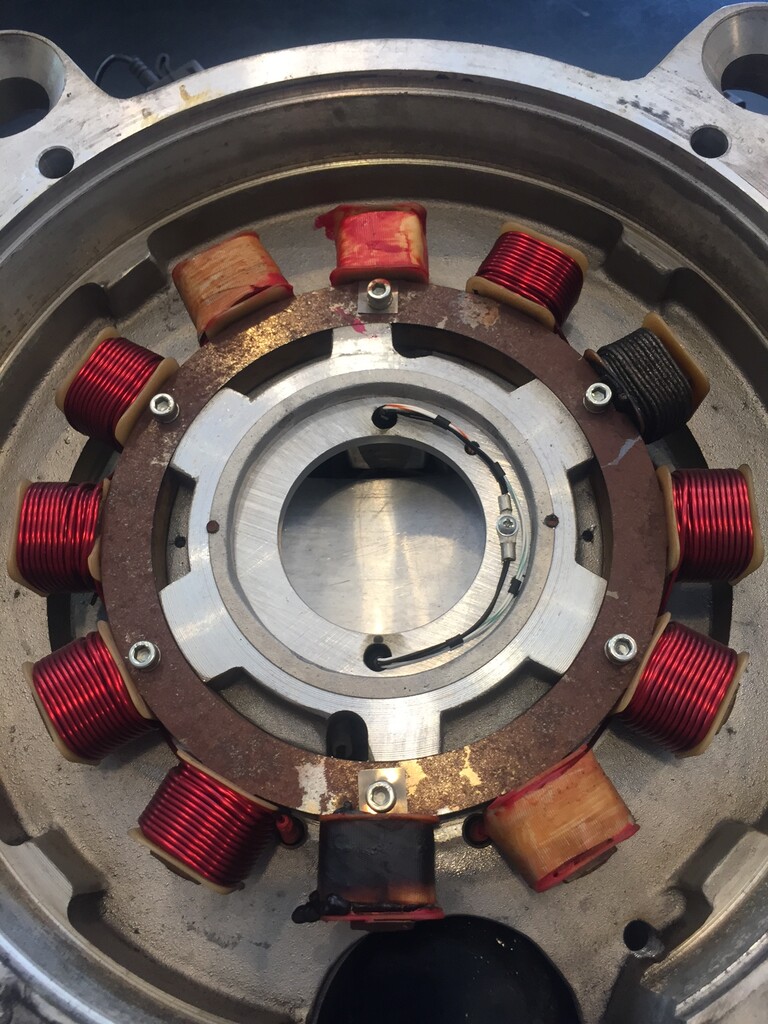
|
Description: |
|
 Download |
Filename: |
42 hz 1200 rpm.pdf |
Filesize: |
893.51 KB |
Downloaded: |
296 Time(s) |
Description: |
|
 Download |
Filename: |
30 hz 875 rpm no charging.pdf |
Filesize: |
30.9 KB |
Downloaded: |
283 Time(s) |
Description: |
|
 Download |
Filename: |
Revmaster R2300 electrical test.pdf |
Filesize: |
28.82 KB |
Downloaded: |
310 Time(s) |
Description: |
|
 Download |
Filename: |
Revmaster 2300 alternator ckt.pdf |
Filesize: |
63.84 KB |
Downloaded: |
326 Time(s) |
Description: |
|
 Download |
Filename: |
Z16M Revmaster 2300 r13-pg1.pdf |
Filesize: |
177.41 KB |
Downloaded: |
289 Time(s) |
_________________ Dan Theis
Scratch building Sonex #1362
Revmaster Alternator problem solved. |
|
Back to top |
|
 |
dj_theis
Joined: 28 Aug 2017 Posts: 58 Location: Minnesota
|
Posted: Fri Jan 08, 2021 7:35 am Post subject: Re: Revmaster R2300 PMA |
|
|
As I re-read my post from last night I realized it was too long and missing some key information. Not to mention a few errors in the text.
There are two issues here. My intent to show the difference in performance of a wet lead acid battery charge vs an AGM. The second is to try and expose the failure mode of the Revmaster alternator.
First, some clarity. The scope trace was my first step to compare a lead acid battery to an AGM. I'll repeat the scope trace and post this weekend the "loaded" lead acid battery charge curve with a loaded AGM charge curve, using the JD alternator and RR previously shown. Attached is the summary of the Kv curve and charging with the (pretty much) fully charged wet cell battery. Note tha the currents are "Peak" and not RMS. the half wave rectified amperage curve peak values are dramatically larger than the RMS values. I will include RMS calculations (that my scope can do) with the loaded charge system curves I'll publish this weekend.
A few errors and ommissions I need to correct.
Only the red scope trace from my previous post (channel B) was a 10x probe.
With regard to the image of the burned stator:
Quote: | I find it more than interesting that only one of the coils making up the left stator is burned while the other 4 appear perfect. |
This should have read "right stator" not left.
Hope this helps a bit.
Dan Theis
| - The Matronics AeroElectric-List Email Forum - | | Use the List Feature Navigator to browse the many List utilities available such as the Email Subscriptions page, Archive Search & Download, 7-Day Browse, Chat, FAQ, Photoshare, and much more:
http://www.matronics.com/Navigator?AeroElectric-List |
|
Description: |
|
 Download |
Filename: |
JD AM877577 peak charge amps with unloaded wet cell.pdf |
Filesize: |
201.22 KB |
Downloaded: |
328 Time(s) |
Description: |
|
 Download |
Filename: |
JD AM877577 OCV.pdf |
Filesize: |
212.5 KB |
Downloaded: |
286 Time(s) |
_________________ Dan Theis
Scratch building Sonex #1362
Revmaster Alternator problem solved. |
|
Back to top |
|
 |
Ceengland
Joined: 11 Oct 2020 Posts: 393 Location: MS
|
Posted: Fri Jan 08, 2021 8:35 am Post subject: Revmaster R2300 PMA |
|
|
On 1/8/2021 9:35 AM, dj_theis wrote:
Quote: |
As I re-read my post from last night I realized it was too long and missing some key information. Not to mention a few errors in the text.
There are two issues here. My intent to show the difference in performance of a wet lead acid battery charge vs an AGM. The second is to try and expose the failure mode of the Revmaster alternator.
First, some clarity. The scope trace was my first step to compare a lead acid battery to an AGM. I'll repeat the scope trace and post this weekend the "loaded" lead acid battery charge curve with a loaded AGM charge curve, using the JD alternator and RR previously shown. Attached is the summary of the Kv curve and charging with the (pretty much) fully charged wet cell battery. Note tha the currents are "Peak" and not RMS. the half wave rectified amperage curve peak values are dramatically larger than the RMS values. I will include RMS calculations (that my scope can do) with the loaded charge system curves I'll publish this weekend.
A few errors and ommissions I need to correct.
Only the red scope trace from my previous post (channel B) was a 10x probe.
With regard to the image of the burned stator:
> I find it more than interesting that only one of the coils making up the left stator is burned while the other 4 appear perfect.
This should have read "right stator" not left.
Hope this helps a bit.
Dan Theis
Hi Dan,
|
I read through the earlier post & looked at the images, though I didn't
download the pdf files. I'm certainly no expert, but my thought is that
what your friend said about internal shorting of the coil would be the
most likely failure mode. Heat within a coil would eventually cause
insulation to fail, and once an internal short occurs, there'd be an
avalanche of heat due to the lowered resistance in the shorter path
through the coil.
It seems to me that all the analysis in the world won't help solve the
problem if you can't do anything about the stator itself. Has anyone
done data logging on one of the failed stators prior to, and during, a
real-world in-use failure? Was it asked to deliver more current than the
rated current? Did the associated rectifier/regulator fail at the same
time, or did it survive, and continue to work correctly?
If the rectifier/regulators aren't failing, then you're left with either
an overload (this is what the mfgr is hinting at with the SLA
prohibition), or a rating number that isn't realistic for the stator's
environment (bolted directly to a hot engine block with near-zero airflow).
The brute force cure for stator survival would be to limit output
current with a *current* regulator, set to limit current below the
stator's *real world* capabilities, in its real world environment. The
prohibition on SLA batteries won't solve anything, in and of itself,
because a larger 'wet cell' battery (to achieve the same CCA) could
easily have the same internal resistance as the previous SLA. All
they're really saying is to limit the load current, but they're
apparently unwilling or unable to give a real world number on the
alternator's current capability, in its environment.
FWIW,
Charlie
--
This email has been checked for viruses by Avast antivirus software.
https://www.avast.com/antivirus
| - The Matronics AeroElectric-List Email Forum - | | Use the List Feature Navigator to browse the many List utilities available such as the Email Subscriptions page, Archive Search & Download, 7-Day Browse, Chat, FAQ, Photoshare, and much more:
http://www.matronics.com/Navigator?AeroElectric-List |
|
_________________ Charlie |
|
Back to top |
|
 |
dj_theis
Joined: 28 Aug 2017 Posts: 58 Location: Minnesota
|
Posted: Fri Jan 08, 2021 9:52 am Post subject: Re: Revmaster R2300 PMA |
|
|
Thanks Charlie,
Quote: | It seems to me that all the analysis in the world won't help solve the
problem if you can't do anything about the stator itself. Has anyone
done data logging on one of the failed stators prior to, and during, a
real-world in-use failure? Was it asked to deliver more current than the
rated current? Did the associated rectifier/regulator fail at the same
time, or did it survive, and continue to work correctly? |
Fully agree. I am working on investigating alternatives (if the failure is primarily due to insufficient vacuum impregnation of the coils). I will be continuing to collect data on my engine before I run it and plan on continued data collection during operation, should if fail.
I do not believe the associated RR failed during the event that led to the burned coil. Also, I don't believe the 30 amp fuses failed either. This is one of the reasons I was looking (and found) the explanation for the inter coil short phenomenon.
In all failures, heat will contribute to the problem and I think there is a sever lack of cooling of the stator. Something else I want to instrument and test with my engine.
Dan Theis
| - The Matronics AeroElectric-List Email Forum - | | Use the List Feature Navigator to browse the many List utilities available such as the Email Subscriptions page, Archive Search & Download, 7-Day Browse, Chat, FAQ, Photoshare, and much more:
http://www.matronics.com/Navigator?AeroElectric-List |
|
_________________ Dan Theis
Scratch building Sonex #1362
Revmaster Alternator problem solved. |
|
Back to top |
|
 |
nuckolls.bob(at)aeroelect Guest
|
Posted: Fri Jan 08, 2021 11:23 am Post subject: Revmaster R2300 PMA |
|
|
Quote: |
The brute force cure for stator survival would be to limit output current with a *current* regulator, set to limit current below the stator's *real world* capabilities, in its real world environment. The prohibition on SLA batteries won't solve anything, in and of itself, because a larger 'wet cell' battery (to achieve the same CCA) could easily have the same internal resistance as the previous SLA. All they're really saying is to limit the load current, but they're apparently unwilling or unable to give a real world number on the alternator's current capability, in its environment.
|
Agreed. I've been pondering this thread periodically
for months. A possible contributor to 'single coil'
failures is the rather large positive temperature
coefficient of copper resistance.
Some months back we discussed the propensity for
a free-air span of copper wire to always burn
in two at or near center of the span . . . and
considered the effects of tempco on the physics
of the melt.
Once a single coil temperature rises above that
of its brothers, electrical energy dissipation within
that coil will climb above the rest with
a positive feedback.
It would be REALLY interesting/useful to mock up this
stator/rotor assembly on a vari-drive to get some
data. I'm not at all comfortable with the notion of
running ONE HALF of a system with demonstrated vulnerabilities
while keeping an equally inadequate half in reserve.
I'm thinking elegant solution might be to run BOTH
coils in a full-wave center tapped supply configuration
to a switchmode power supply fitted with accurate/stable
voltage regulation and calibrated current limiting.
Instead of walking a tight-rope of high probability
failure modes, designing a system that strives for
predictable stress limiting seems more in order.
Generators did it, alternators do it, why not a
PM alternator?
Bob . . .
Un impeachable logic: George Carlin asked, "If black boxes
survive crashes, why don't they make the whole airplane
out of that stuff?"
| - The Matronics AeroElectric-List Email Forum - | | Use the List Feature Navigator to browse the many List utilities available such as the Email Subscriptions page, Archive Search & Download, 7-Day Browse, Chat, FAQ, Photoshare, and much more:
http://www.matronics.com/Navigator?AeroElectric-List |
|
|
|
Back to top |
|
 |
|
|
You cannot post new topics in this forum You cannot reply to topics in this forum You cannot edit your posts in this forum You cannot delete your posts in this forum You cannot vote in polls in this forum You cannot attach files in this forum You can download files in this forum
|
Powered by phpBB © 2001, 2005 phpBB Group
|